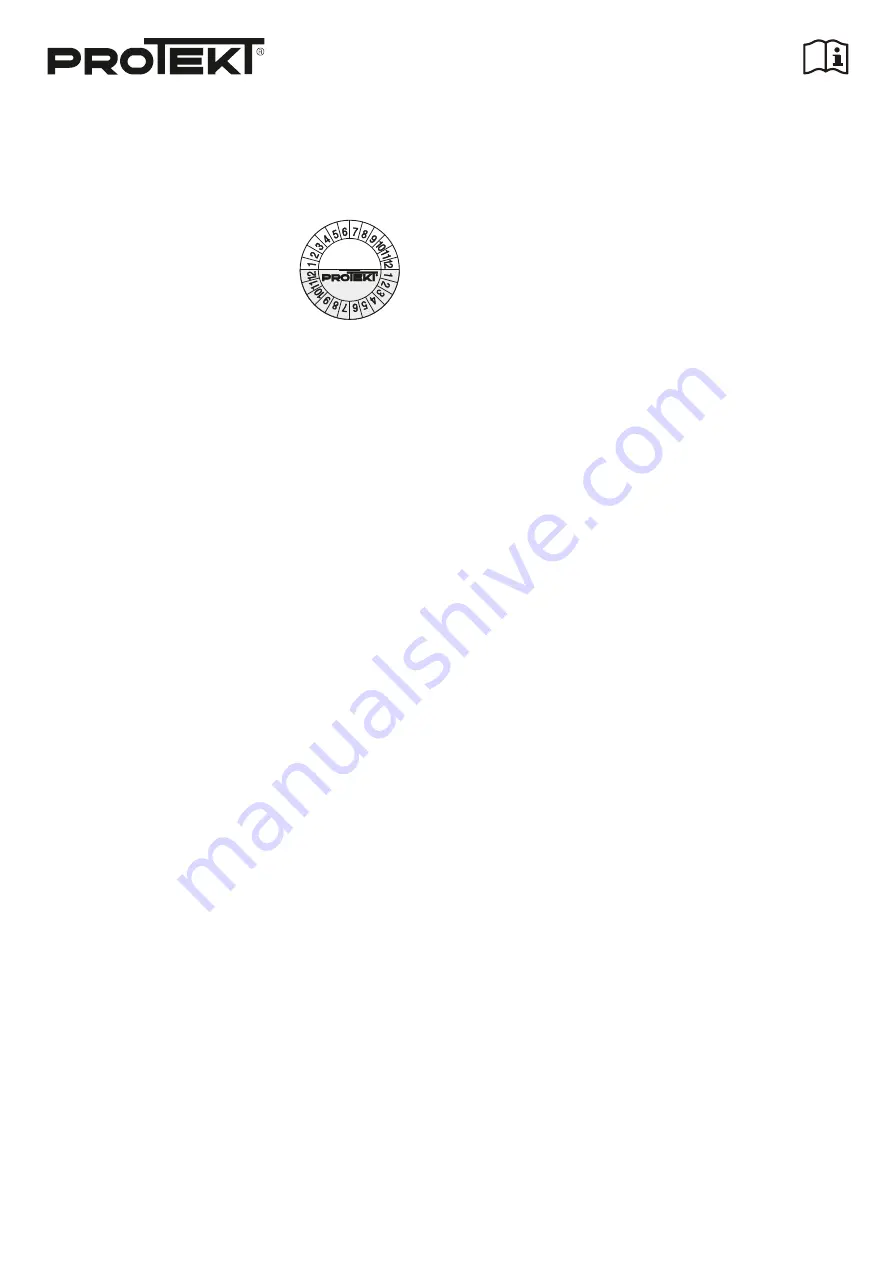
When using the system, pay special attention to risks affecting the protective equipment operation or the user’s safety, and in
particular to kinks and rope movement on sharp edges, oscillatory falls, electricity, influence of extreme temperatures, equipment
damage, negative influence of environmental factors, chemical substances and contamination.
Do not modify, repair components of the system or replace them with non-original spare parts.
It’s recommended to mark the device with the date (month and year) of next inspection date using a special sticker – see it below.
Attention: Before the first use mark
the date of the first inspection
(date of first use +12 months).
Don't use the device after this date.
5. Device marking
See fig. 3
6. Installation of anchor point
• Before anchor point AT150 is installed, it must be stored in a place which is: clean, free from any vapours of corrosive substances, and
in conditions preventing its mechanical damage. Also please take into account environmental conditions present in the place of
installation which may cause corrosion of anchor point and fasteners.
• Installation of the anchor point must be carried out in accordance with rules of fixing on steel structures or concrete elements. When
fixing on metal surfaces use bolts M12 of any length and tension grade of no less than A2/70. When fixing on concrete surfaces use
throughbolts M12 or chemical anchors M12.
• Installation with use of anchors should be carried out in accordance with guidelines specified by the manufacturer of these elements.
• Follow general rules for use of personal fall protection equipment in accordance with EN 795:2012.
• For installation on a concrete surface using throughbolts or mechanical anchors the required strength of these surfaces should be
greater than 20MPa,
• Anchor point AT 150 should be installed above the workplace.
• Example installations are shown in figures
7. Installation on steel and concrete surfaces
Anchor point may be installed on steel structure the thickness of which is more than 3mm. Drill two holes of 12.5-13mm in diameter
spaced 100mm with possible error margin of up to 5mm. Figure no. 4. Strength of steel structure to which anchor point is to be
installed should be calculated and be no less than 12kN.
Fix anchor point AT150 in the drilled holes using M12 bolts of adequate length and strength class, accordingly:
• for galvanized bolts – strength class no lower than 8.8
• for stainless steel (A2) and acid resistant steel (A4) bolts – strength class no lower than 70. (Figure 5)
Bolts should be tightened using a torque wrench by applying a torque of no more than 40Nm. Increasing the torque may damage
aluminium structure of anchor point AT150 or break it in case of unevenness of contact surface (Figure 6).
Anchor point AT150 is suitable also for installation in concrete structures using mechanical anchors (throughbolts) or chemical anchors
of 12mm in diameter. For installation using mechanical and chemical anchors, keep closely to recommendations given by
manufacturers of these anchors (drilling depth, drill bit diameter, anchor torque).
Concrete structure should be dense and have no surface cracks or chips.
Mechanical strength of concrete should be no higher than 20MPa.
Before installation on concrete structure assess the surface for unevenness. If any unevenness greater than 2mm is found (Figure 7) on
anchor point installation line, use special EPDM rubber pad (PS150) to reduce stresses in aluminium structure of the anchor point
(Figure 8). In the case of a minor unevenness the rubber pad is not necessary.
Drill two holes of 12mm in diameter and depth of approx. 120mm, spaced 100mm +/- 5mm (Figure 9).
Fasteners, as anchors, should be placed in such holes using a hammer (in accordance with instructions for installation of anchors
(Figure 10).
Anchors should be tightened using a torque wrench with a torque value specified by the manufacturer (usually 40Nm) (Figure 11).
8. Connecting fall protection system to the AT 150
Fall protection system should be attached the AT150 with EN362 connectors only.The system should be connected to the AT150 in such
a way the function of any component of the system is not affected by, or interferes with the function of any other. See figure 12.
9. Essential principles for use of personal fall protection equipment
• Anchor point AT150 must be used in accordance with instruction manuals for personal fall protection equipment and standards:
- EN 361 - Full body harness
- EN352-3; EN355; EN360 - Personal fall protection equipment
- EN362 - Connectors
- EN 795 - Anchor points
NASTĘPNY PRZEGLĄD
20xx
20xx
3/5
READ AND UNDERSTAND INSTRUCTION MANUAL
BEFORE USING THE EQUIPMENT