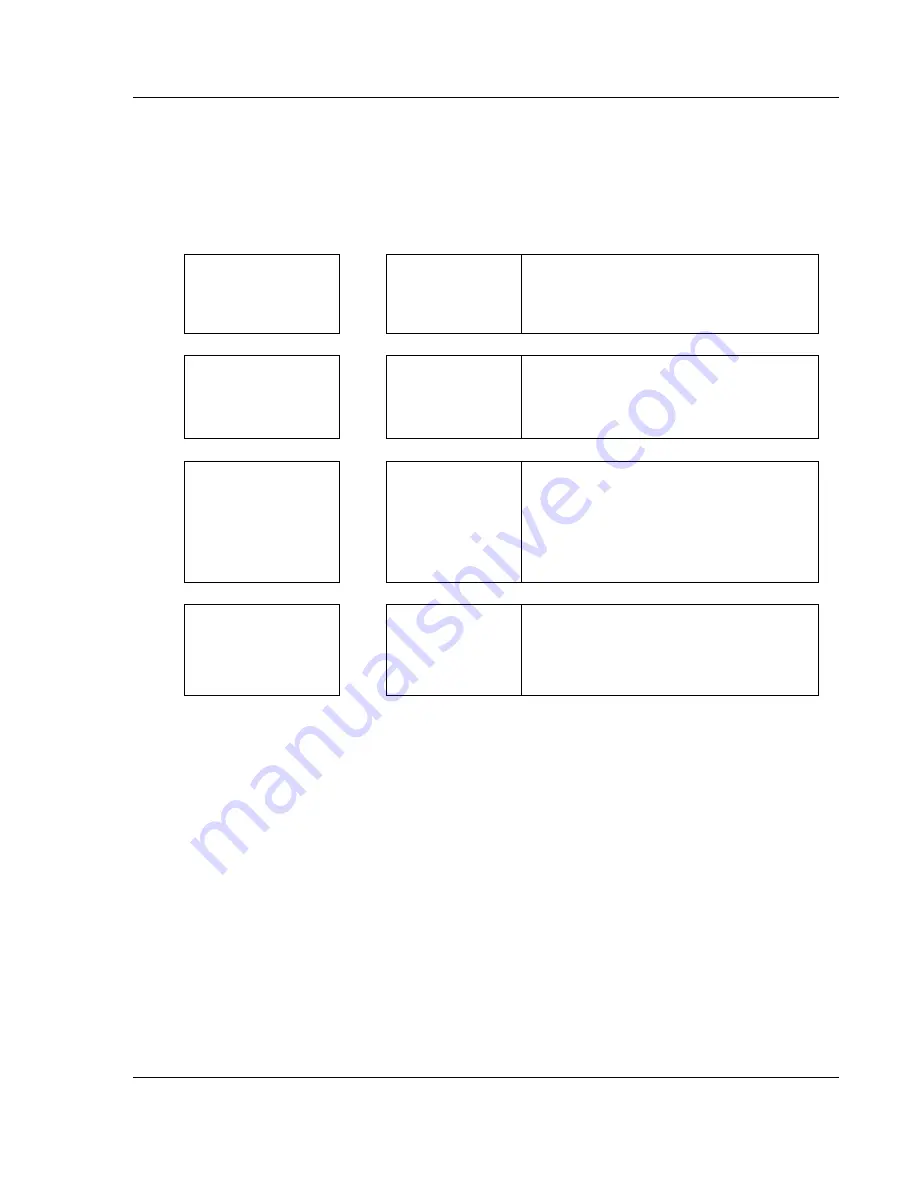
MVI56-HART ♦ ControlLogix Platform
Guide to the MVI56-HART User Manual
HART Multi-drop Master Communication Module
User Manual
ProSoft Technology, Inc.
Page 11 of 171
October 13, 2011
Guide to the MVI56-HART User Manual
Function
Section to Read
Details
Introduction
(Must Do)
Start Here (page 12) This section introduces the customer to the
module. Included are: package contents,
system requirements, hardware installation, and
basic configuration.
Diagnostic and
Troubleshooting
Diagnostics and
Troubleshooting
(page 61)
This section describes Diagnostic and
Troubleshooting procedures.
Reference
Product Specifications
Reference (page 79)
Product
Specifications (page
80)
These sections contain general references
associated with this product and its
Specifications..
Support, Service, and
Warranty
Index
Support, Service
and Warranty (page
161)
Index
This section contains Support, Service and
Warranty information.
Index of chapters.