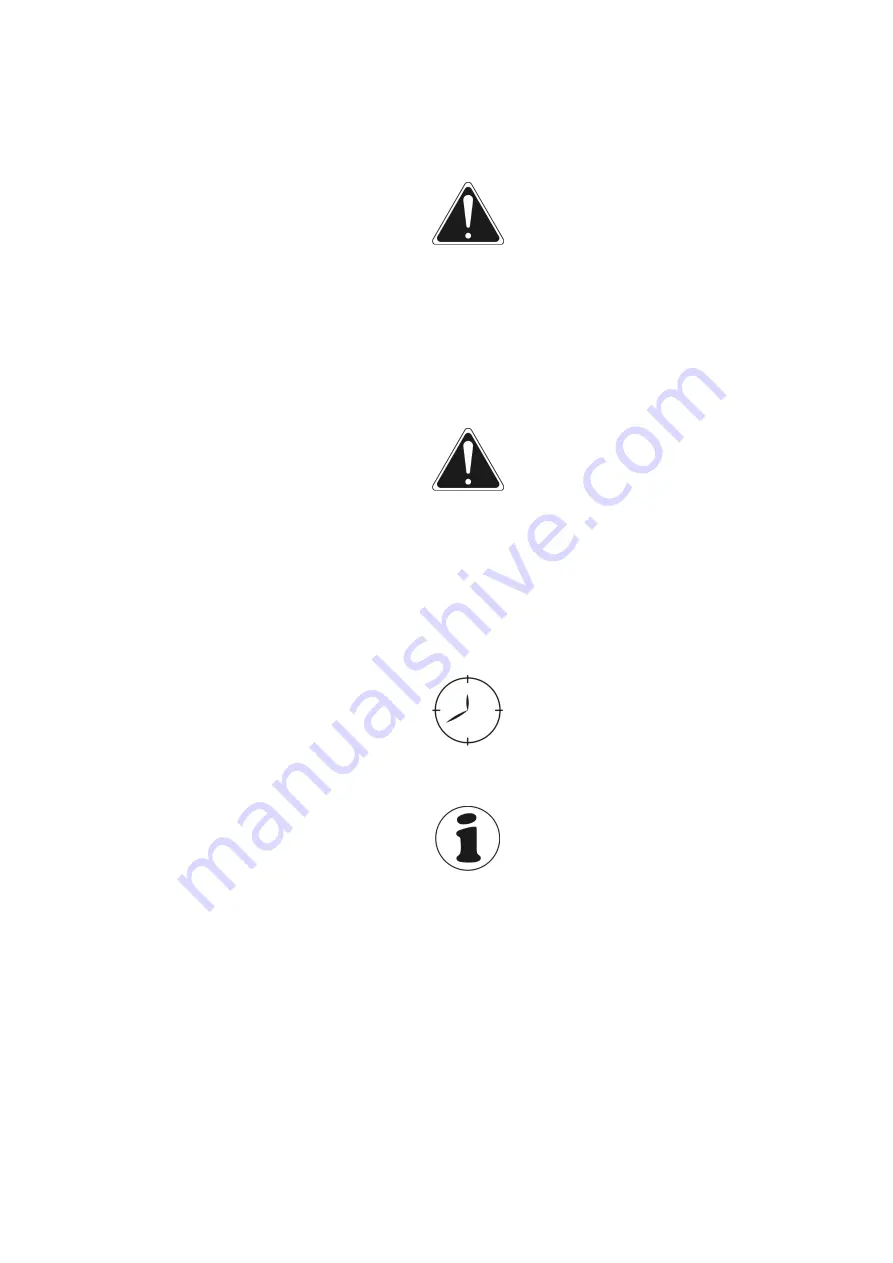
SYMBOLS APPEARING IN THIS OPERATOR'S MANUAL
Information, descriptions of danger and precautions and also recommendations and prohibitions
associated with user safety instructions are marked:
and also preceded by the word "DANGER”. Failure to observe the instructions may endanger
the machine operator's or other person's health or life.
Particularly important information and instructions, the observance of which is essential, are
distinguished in the text by the sign:
and also preceded by the word "ATTENTION". Failure to observe the instructions may lead to
damage to the machine as a result of improper operation, adjustment or use.
In order to focus the user's attention on the need to perform maintenance, the relevant section
of the Operator's Manual is marked with the pictogram:
Additional tips and advice for machine operation are marked with the sign:
and also preceded by the word "TIP".
DIRECTIONS USED IN THIS OPERATOR'S MANUAL
Left side – side to the left hand of the operator facing in the direction of machine's forward
travel.
Right side – side to the right hand of the operator facing in the direction of machine's forward
travel.
Summary of Contents for PWP900
Page 2: ......
Page 3: ...ROTARY TEDDER PRONAR PWP900 MACHINE IDENTIFICATION SYMBOL TYPE SERIAL NUMBER ...
Page 6: ......
Page 7: ......
Page 8: ......
Page 11: ...SECTION 1 BASIC INFORMATION ...
Page 21: ...SECTION 2 SAFETY ADVICE ...
Page 33: ...SECTION 3 DESIGN AND OPERATION ...
Page 35: ...SECTION 3 PRONAR PWP900 3 3 3 2 DESIGN AND OPERATION FIGURE 3 1 General design ...
Page 39: ...SECTION 4 CORRECT USE ...
Page 58: ...PRONAR PWP900 SECTION 4 4 20 ...
Page 59: ...SECTION 5 MAINTENANCE ...
Page 67: ...SECTION 5 PRONAR PWP900 5 9 FIGURE 5 3 Positions of the tedder s lubrication points ...
Page 72: ...PRONAR PWP900 SECTION 5 5 14 ...
Page 73: ...NOTES ...
Page 74: ......