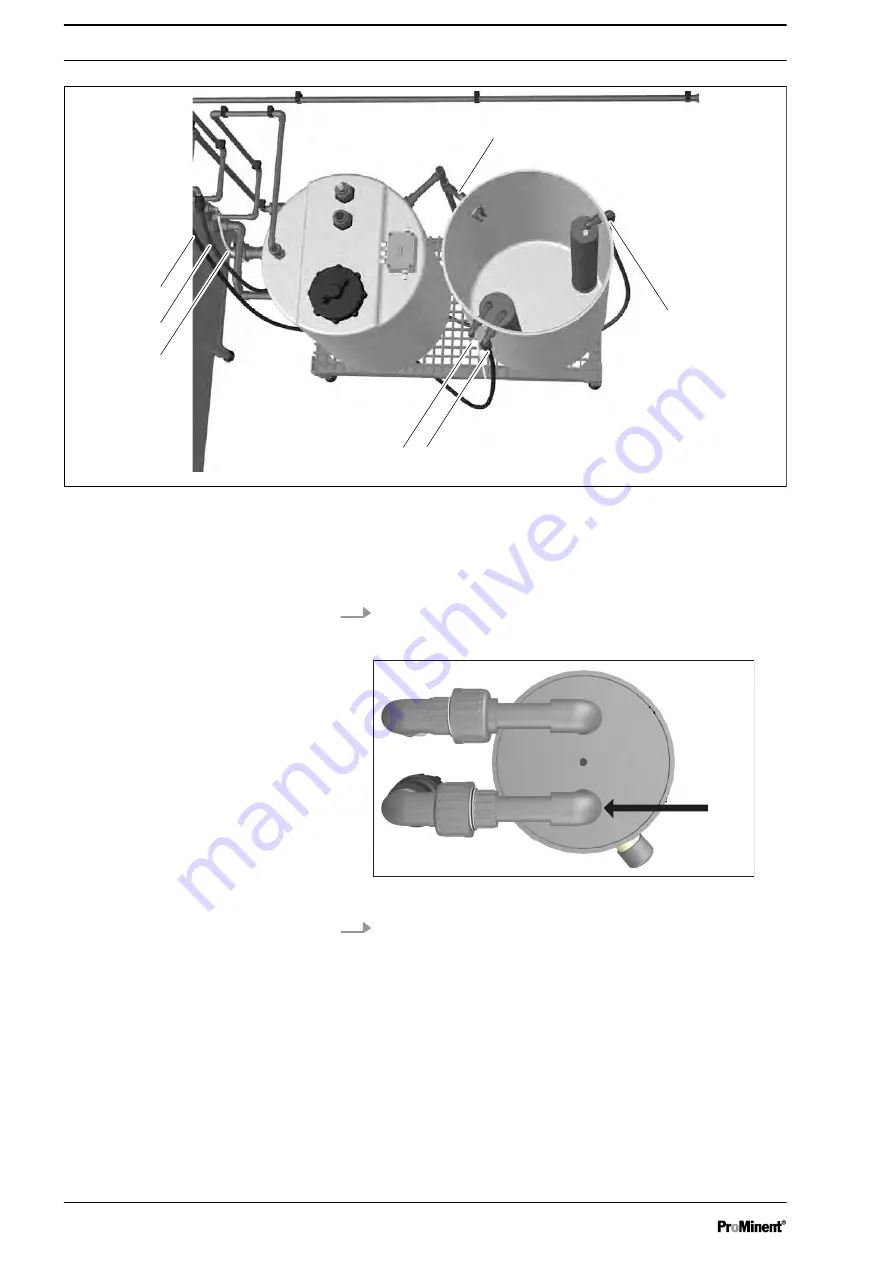
2
1
3
1 2
3
B0956
4
Fig. 17: Couplings
1. Coupling for "Brine softener" hose, transparent
2. "Brine membrane cell" PE coupling, blue
3. "Fill brine tank" PE coupling, red
4. "Brine tank overflow" coupling
28. Use the black PE hose (Ø16 mm x 1.8 mm) from the brine
tank to join the "Fill brine tank" connector (3) on the system
to the Ø16 mm connector on the brine tank.
Fig. 18: "Brine membrane cell" connector
29. Use the (Ø16 mm x 1.8 mm) PE hose to join the "Brine mem‐
brane cell" connector on the system to the Ø16 mm con‐
nector on the brine tank.
Installation and assembly
28