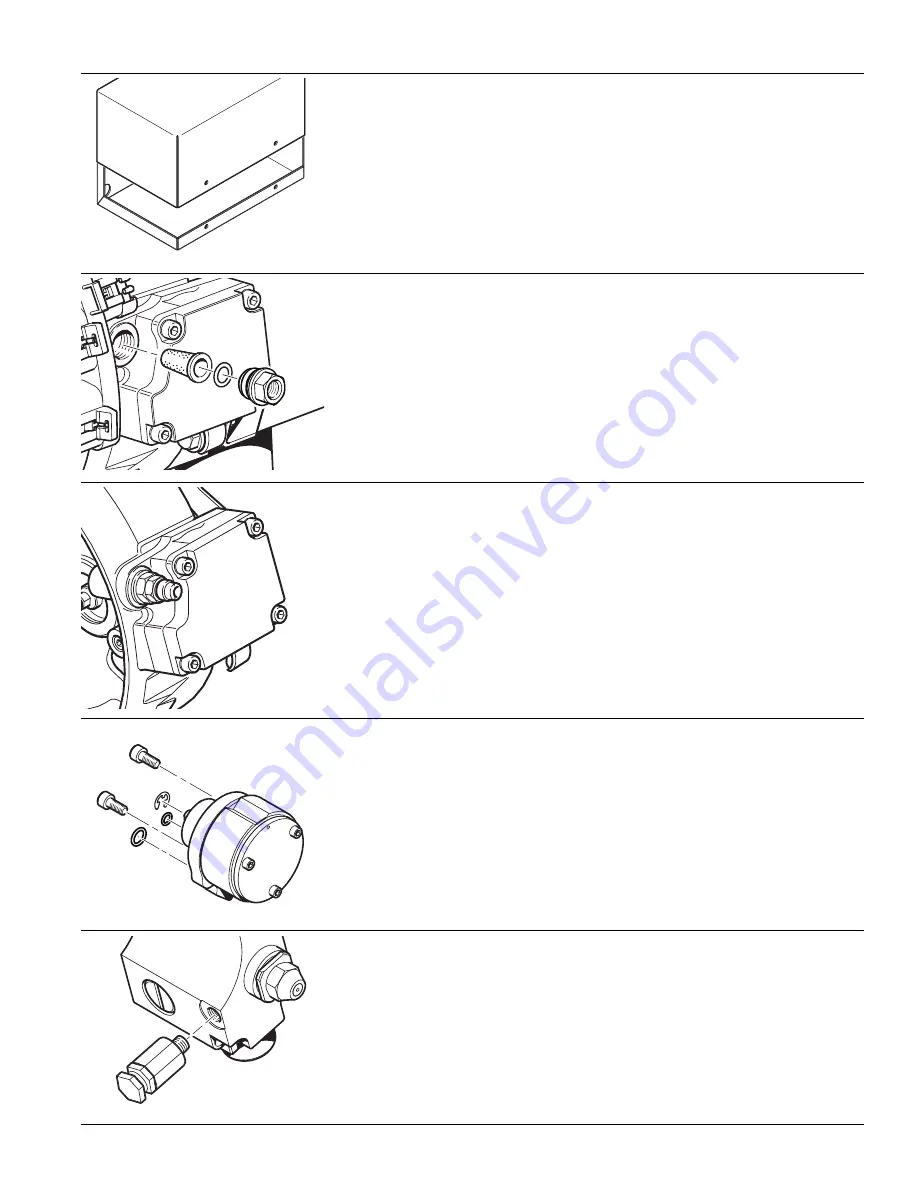
Enclosure Lid
(Optional)
•
Torque screws (4) to 100 in. lbs. ± 10 in. lbs. (11.6 Nm ± 1.1 Nm).
Fuel Filter Fitting
•
Install O-ring onto fitting.
•
Torque fitting to 100 ± 10 in. lbs. (11.3 ± 1.1 Nm).
Rotary Vane Compressor ONLY
Serial Numbers 500000 – 699999
•
Install O-rings into burner flange.
•
Install compressor into burner flange. (Ensure correct alignment—refer to
Compressor Replacement’ on page 5-7.)
•
Torque screws (2) to 75 in. lbs. ± 3 in. lbs. (8.5 Nm ± 0.3 Nm).
Relief Valve
– for Use with Rotar y Vane Compressor ONLY
Serial Numbers 600000 – 699999
•
Torque to 25 in. lbs. ± 3 in. lbs. (2.8 Nm ± 0.3 Nm).
Diaphragm Compressor ONLY
Serial Numbers 70000 and above
•
Install O-rings in to cylinder head and valve cover (not shown).
•
Ensure connecting rod is at BDC and ensure the diaphragm is concentric
to the diaphragm opening (not shown).
•
Torque to 27 in. lbs +/- 3 in. lbs using a crisscross pattern.
1-11
PROHEAT M-SERIES G-II PCM SERVICE MANUAL
Summary of Contents for M105 G-II PCM
Page 7: ...PROHEAT M SERIES G II PCM SERVICE MANUAL B 2 ...
Page 11: ...PROHEAT M SERIES G II PCM SERVICE MANUAL D 2 ...
Page 25: ...PROHEAT M SERIES G II PCM SERVICE MANUAL 1 12 ...
Page 35: ...2 10 PROHEAT M SERIES G II PCM SERVICE MANUAL ...
Page 77: ...PROHEAT M SERIES G II PCM SERVICE MANUAL 4 40 ...
Page 89: ...6 2 PROHEAT M SERIES G II PCM SERVICE MANUAL ...