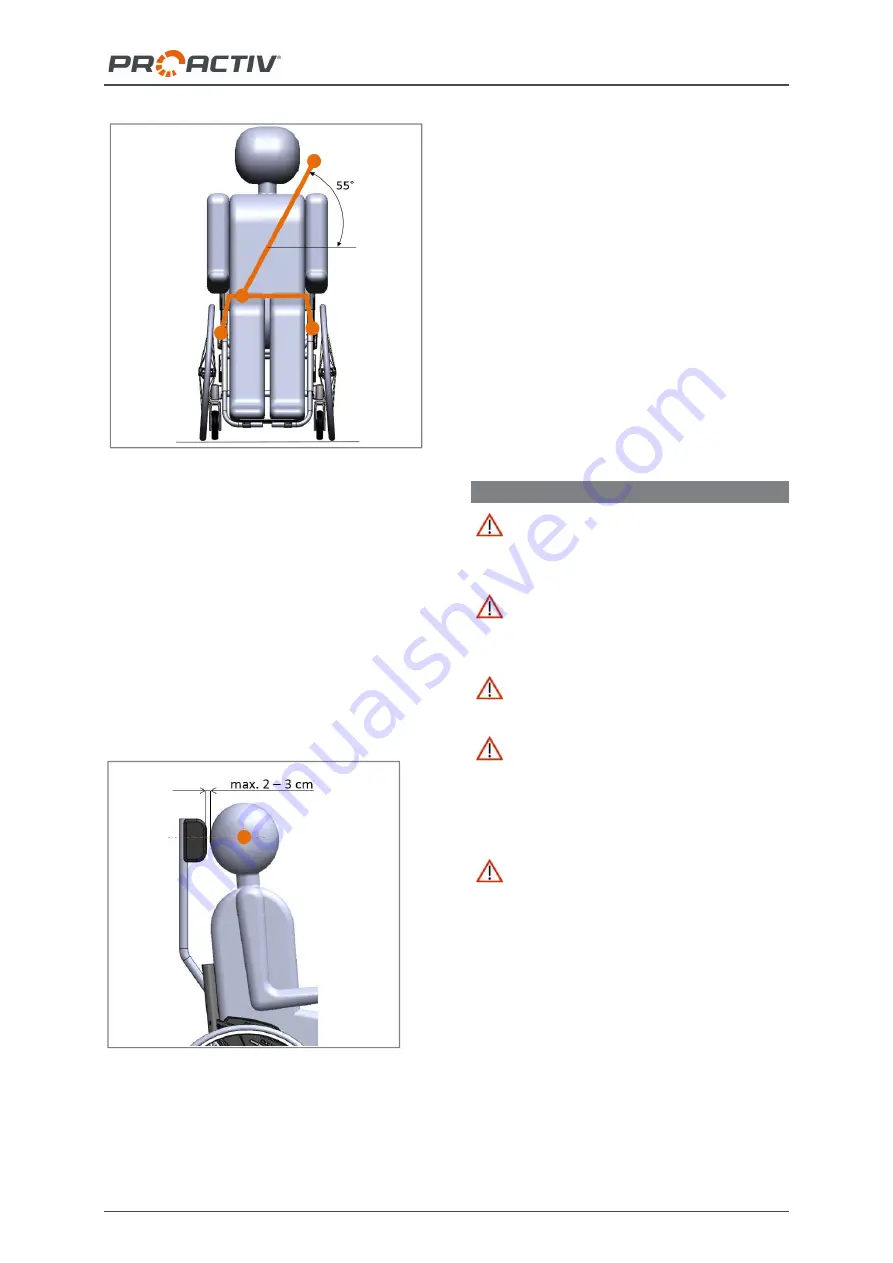
Usage instructions SPEEDY 4all & 4you & 4teen
73
Figure 216: Run of the lap and diagonal shoulder
belt with the respective connecting points (view from
the front)
Adjustable-inclination backrests must be set to
the most vertical position in order to ensure
upright sitting.
The height and distance of the headrest to the
head must be set so that the centre of gravity
of the upright head is in the middle of the head-
rest and the distance between the head and
headrest padding must be kept as little as pos-
sible (max. 2-3 cm).
Figure 217: Setting a headrest with regard to the
height and distance from the head
To ensure that the wheelchair user is ade-
quately protected against collisions with vehi-
cle parts and panels, the following clearances
must be adhered to around him:
To the front, at least 65 cm (95 cm for use
of a lap belt without a diagonal shoulder
belt) measured from the front edge of the
head
To the rear, at least 45 cm measured from
the rear edge of the head
Upwards, at least 120 cm for a small, fe-
male adult, or at least 155 cm for a large,
male adult, each measured from the vehi-
cle floor.
27.6 Safety instructions
You must be able to hear all links engag-
ing in the buckles. Belts must not be twisted
and not run crossed-over.
For belt systems (hip, diagonal shoulder
belt, retractors), the instructions for use of the
respective manufacturer must be observed.
During transport, the parking brake of the
product must be applied.
Loose parts of the wheelchair (therapy
tray, crutches, etc.) must be removed prior to
the journey and stowed securely in the vehicle
to prevent injuries to the vehicle occupants in
the event of a collision.
Wheelchairs and restraint systems that
have been exposed to an impact must be re-
placed. They may no longer be used as a seat
or for securing in motor vehicles.