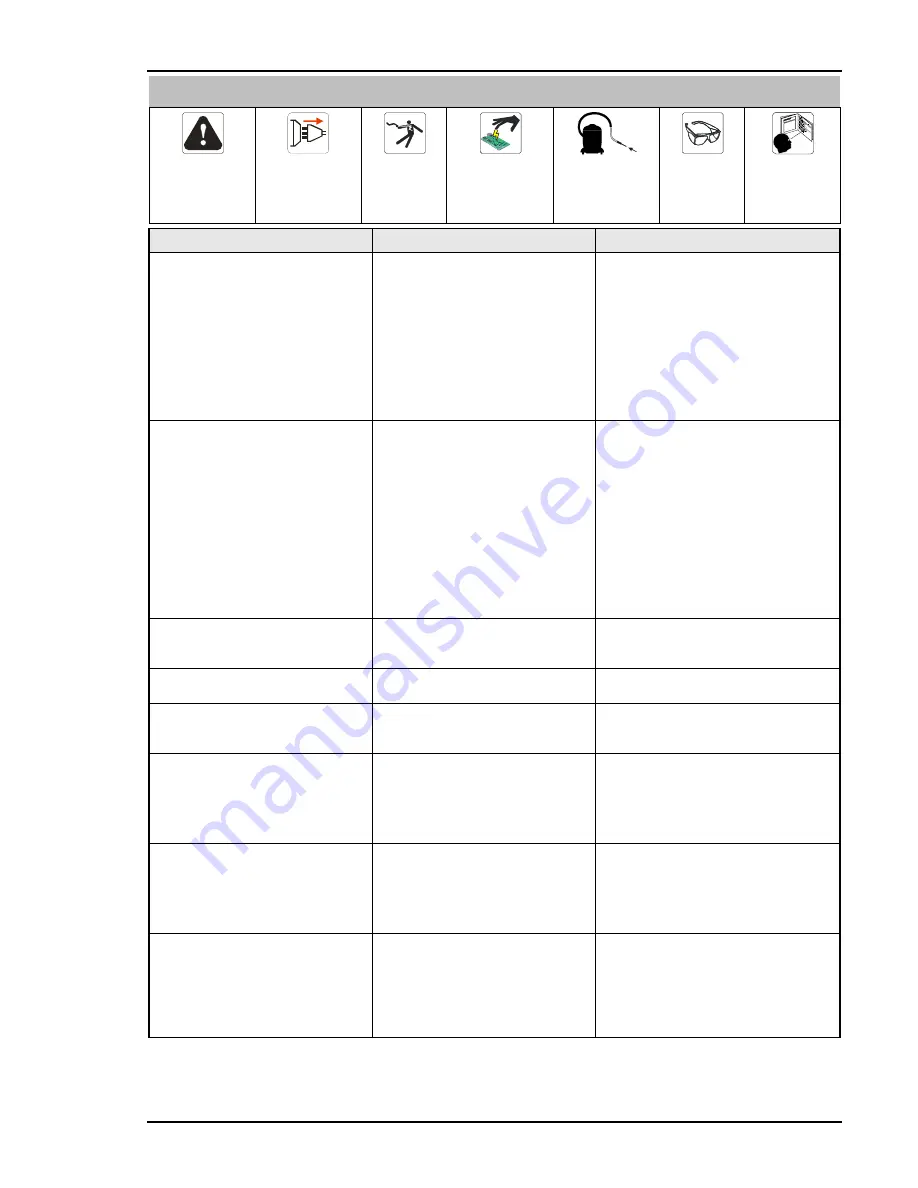
TROUBLESHOOTING and MAINTENANCE
© 2018 Global Welding LLC
Page
35
Operating Manual No: PWOM-215/250MP-001
6.5
P
RO
-
TEC
215MP / 250MP Power Source Troubleshooting
Danger! Extremely
dangerous voltages
inside Power
Source
Disconnect Input
Power Supply be-
fore opening Power
Source
Electric shock
can kill
Electrostatic dis-
charge can damage
PC Boards
Remove any metal-
lic particles / dirt
using vacuum
cleaner
Flying metal or
dirt can injure
eyes
Read Operating
Manual
Description
Possible Cause
Remedy
1.
The welding arc cannot be established.
A
The Input Supply Voltage isn’t switched
ON.
B
The Power Source switch is switched
OFF.
C
Loose connections internally.
D
No Open Circuit Voltage in Stick or Lift
TIG mode.
A
Switch ON the Input Supply Voltage.
B
Switch ON the Power Source.
C
Have an approved Service Provider repair the
connection. Refer to SECTION 7 – PRO-TEC
WARRANTY POLICY.
D
Have an approved Service Provider inspect
then repair. Refer to SECTION 7 – PRO-TEC
WARRANTY POLICY.
2.
The welding arc cannot be established
when the Fault Indicator is on
A
The Power Sources duty cycle has been
exceeded or a fault has occurred.
B
Internal component failure.
C
Fan not working.
A
Wait for the Indicator to go out then reduce
welding time or get approved Service Provider
to repair. Refer to SECTION 7 – PRO-TEC
WARRANTY POLICY.
B
If Fault indicator does not go out after 10
minutes then have an approved Service Pro-
vider inspect then repair the welder. Refer to
SECTION 7 – PRO-TEC WARRANTY POLICY.
C
If fan is clogged with dust then remove dust.
If fan does not rotate then have an approved
Service Provider inspect then repair the weld-
er. Refer to SECTION 7 – PRO-TEC WARRAN-
TY POLICY.
3.
Maximum output Welding Amperage
cannot be achieved with nominal Input
Supply Voltage.
Defective control circuit
Have an approved Service Provider inspect then
repair the welder. Refer to SECTION 7 – PRO-TEC
WARRANTY POLICY.
4.
Welding Amperage reduces when weld-
ing.
Poor work lead connection to the work piece. Ensure that the work lead has a positive electrical
connection to the work piece.
5.
Circuit breaker (or fuse) trips during
welding.
The circuit breaker (or fuse) is under size.
Refer to Section 4.6 and Section 4.7 for the rec-
ommended circuit breaker (or fuse) size for the
Input Supply Voltage used.
6.
Difficult to establish an arc in Stick
mode.
A
Loose connections in welding leads.
B
Metal is contaminated with oil or rust or
grease or dirt.
A
Check all welding leads electrical connections
for defects like burnt or discoloration connec-
tions. Replace/replace electrical connections
or welding leads.
B
Clean metal to remove contamination.
7.
The arc wanders away from the joint
during welding (Arc Blow).
A
Air movement is pushing the arc.
B
The coating on the stick electrode isn’t
even around the metal core.
C
Welding Amperage passing thru the metal
sets up a magnetic field which pushes the
arc.
A
Shield the weld zone from the air movement.
B
Use a new electrode from another batch.
C
Reposition the Earth Clamp position to reduce
this affect.
8.
Wire feeds out of MIG Gun but no shield-
ing gas flows.
A
Gas cylinder empty.
B
Gas regulator closed.
C
Faulty solenoid or electronics.
D
Restriction in MIG Gun cable.
A
Change to a full gas cylinder.
B
Open gas regulator.
C
Have an approved Service Provider repair the
connection. Refer to SECTION 7 – PRO-TEC
WARRANTY POLICY.
D
Straighten out MIG Gun cable.
Disconnect