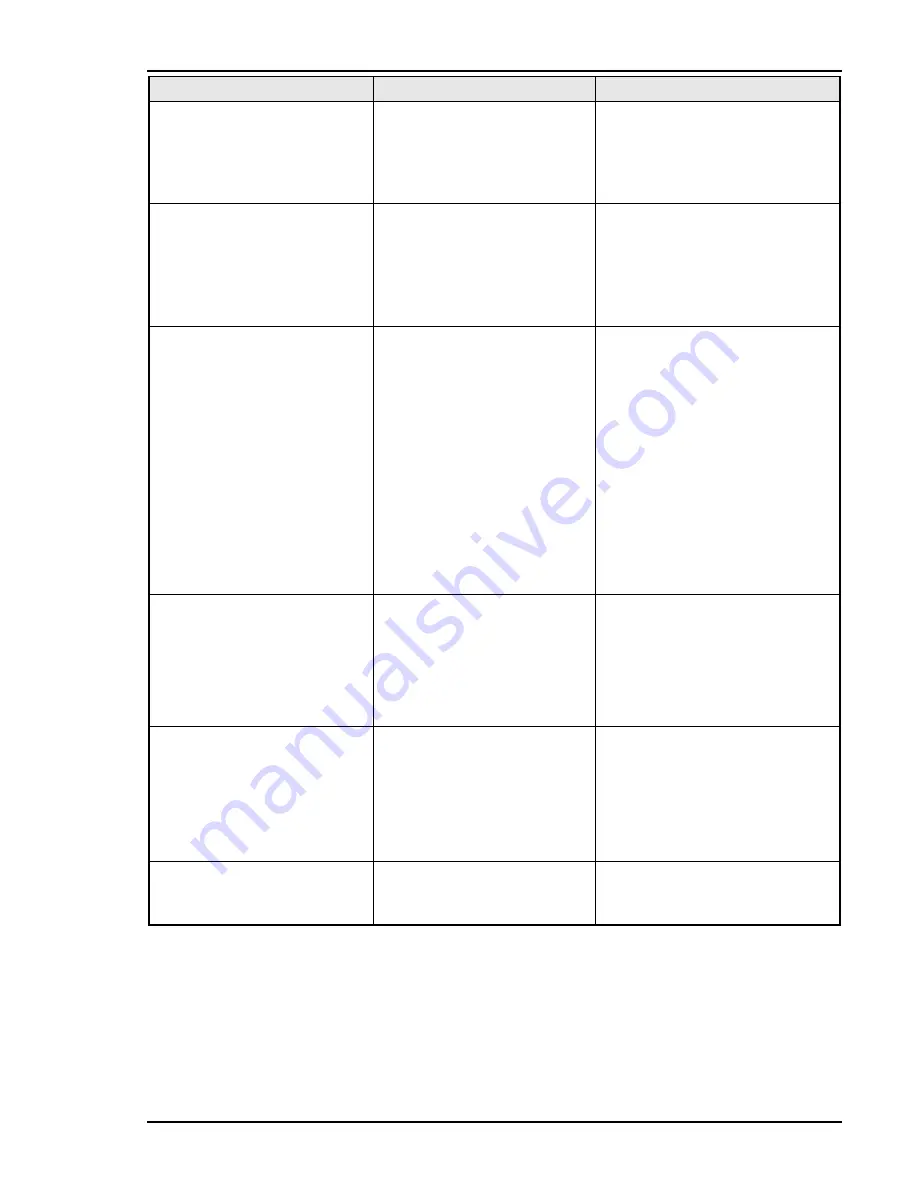
TROUBLESHOOTING and MAINTENANCE
© 2018 Global Welding LLC
Page
31
Operating Manual No: PWOM-215/250MP-001
Description
Possible Cause
Remedy
8.
Welding Wire bird nest.
A
Excessive Drive Roll pressure
B
Incorrect or blocked Liner.
C
Incorrect contact tip size or contact tip
overheating.
D
MIG Gun cable kinked.
A
Decrease pressure on the Drive Roll by turn-
ing Pres-sure Device counter clockwise.
B
Replace Liner to suit Welding Wire.
C
Replace contact tip to suit Welding Wire.
D
Straighten out MIG Gun cable.
9.
Burnt Back onto the contact tip.
A
Burn Back control is not set correctly.
B
Improper stick out.
C
Erratic wire feed.
D
Incorrect or blocked liner.
E
Contact tip overheating.
F
MIG Gun cable kinked.
A
Adjust the Burn Back control.
B
Increase Stick-Out length to 3/8”-1/2”.
C
See No. 10 Erratic Wire Feeding or Welding
Arc.
D
Replace the Liner to suit the Welding Wire.
E
Replace contact tip.
F
Straighten out MIG Gun cable.
10.
Erratic Wire Feeding or Welding Arc
A
Excessive Drive Roll pressure.
B
Incorrect Drive Roll size.
C
Worn Drive Roll.
D
Incorrect or blocked liner
E
Gaps at liner/contact tip junction or wire
guide junctions.
F
Incorrect or worn contact tip size or
contact tip overheating.
G
Spatter adhesion on end of contact tip.
H
MIG Gun cable kinked.
I
Poor Ground Clamp or cable connec-
tions.
J
Weld joint area dirty.
A
Decrease pressure on the Drive Roll by turn-
ing Pres-sure Device counter clockwise.
B
Fit a suit size and type of Drive Roll that suits
the welding wire.
C
Replace the Drive Roll that suits the welding
wire.
D
Replace the Liner to suit the Welding Wire.
E
Reduce the gaps at liner/contact tip junction
or wire guide junctions.
F
Replace contact tip to suit Welding Wire.
G
Replace contact tip to suit Welding Wire.
H
Straighten out MIG Gun cable.
I
Inspect Ground Clamp/cable connections for
discoloration or damage then repair/replace.
J
Clean joint before welding.
11.
Irregular weld bead shape.
A
Incorrect Voltage and Wirefeed Speed
settings.
B
Wire is wandering.
C
Incorrect shielding gas.
D
Insufficient or excessive heat input into
weld puddle.
A
Adjust Voltage and Wirefeed Speed by ad-
justing the Voltage control and the Wirefeed
control.
B
Replace contact tip to suit Welding Wire.
C
Check that you have welding grade correct
shielding gas.
D
Change Wirefeed Speed and/or change
Voltage or change MIG Gun travel speed.
12.
Weld metal cracking.
A
Weld beads too small.
B
Weld penetration narrow and deep.
C
Excessive weld stresses.
D
Excessive Voltage.
E
Weld metal cooling rate too fast.
A
Decrease MIG Gun travel speed.
B
Reduce Wirefeed Speed / Voltage and in-
crease MIG Gun travel speed or select a
lower penetration shielding gas.
C
Change weld joint design.
D
Decrease Voltage.
E
Slow cooling rate by preheating base metal.
13.
Cold weld puddle.
A
Loose welding cable connection.
A
Check all welding leads electrical connec-
tions for defects like burnt or discoloration
connections. Replace/replace electrical con-
nections or welding leads.