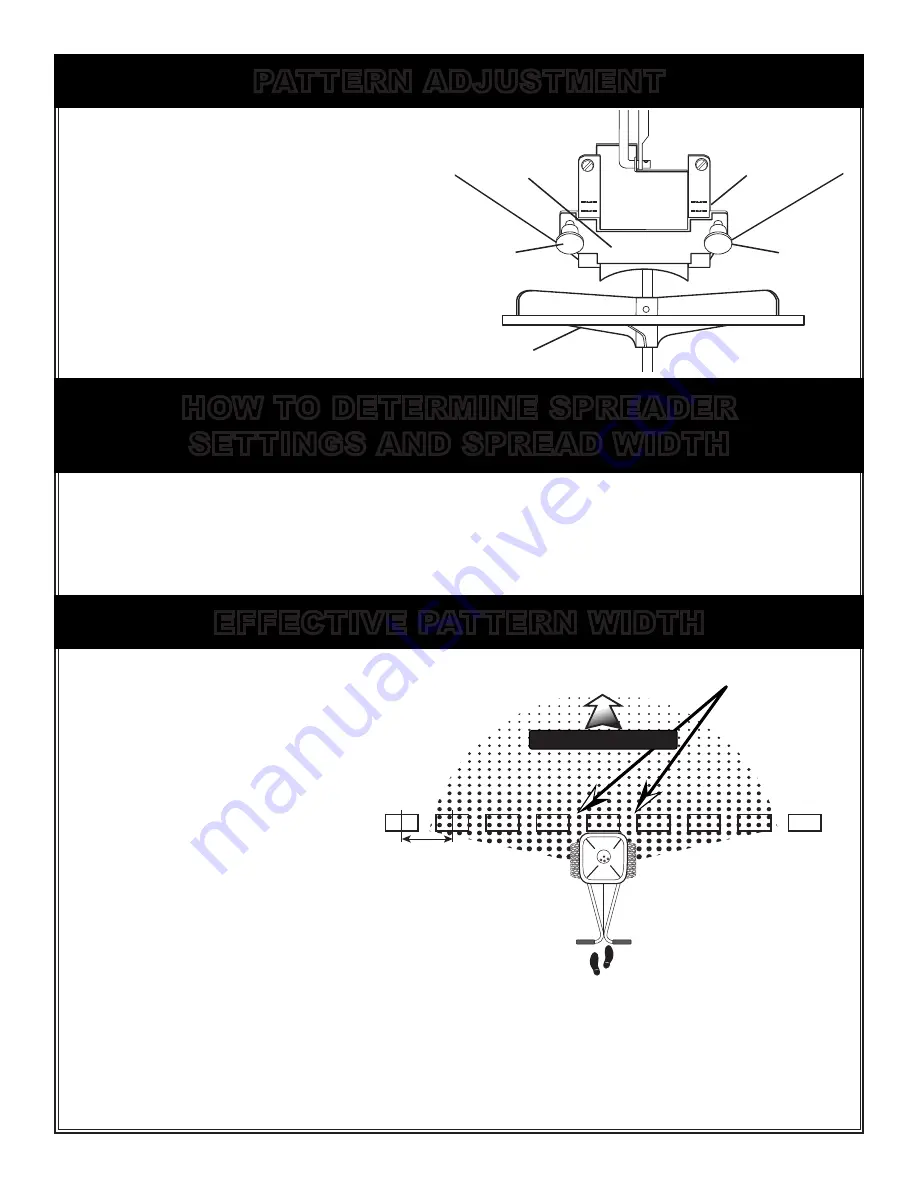
B
A
B
A
Impeller
Knob
Discharge
Chute
Discharge
Chute
Settings
Knob
Two major factors should be considered when determining correct spreader settings of any product:
1.
The product application rate, or the amount of material applied per 1,000 square feet.
2.
The effective pattern width, or the actual width in which material is applied. Label settings are a guide
and can be affected by numerous factors.
Normal spreading of materials requires no
adjustment (factory setting “A”) unless stated on
the package. In those cases where the spread
pattern has shifted, the pattern can be adjusted
left and right by loosening the two knobs on the
discharge chute and moving the chute closer or
farther away from the impeller. Settings of “A, B,
and C” are provided as reference.
A simple visual pattern test can be
made by operating the spreader over a
non-turf area and evaluating the pattern.
A more accurate method is to place a
row of common, disposable, aluminum
cake pans approximately 1 foot on
centers. Set the rate plate at a middle
setting and make 3 or 4 passes in the
same direction as shown. Pour the
material collected from each pan into
individual bottles of the same size. Set
them side by side in order, and visually
inspect their volume. If the pattern is not
centered (example: volume in bottle #2
left not equal to bottle #2 right), adjust
the discharge chute up or down as
described in “
PATTERN ADJUSTMENT
” section above.
Once the pattern is uniform, the effective pattern width can be determined. The effective pattern width is
the distance out from the spreader to a point where the amount of material is 1/2 the average amount in the
center pans. This distance is multiplied by 2 to achieve the total effective pattern width.
Leave space for wheel path
Direction of travel
Space pans 1’
on centers
PATTERN ADJUSTMENT
HOW TO DETERMINE SPREADER
SETTINGS AND SPREAD WIDTH
EFFECTIVE PATTERN WIDTH