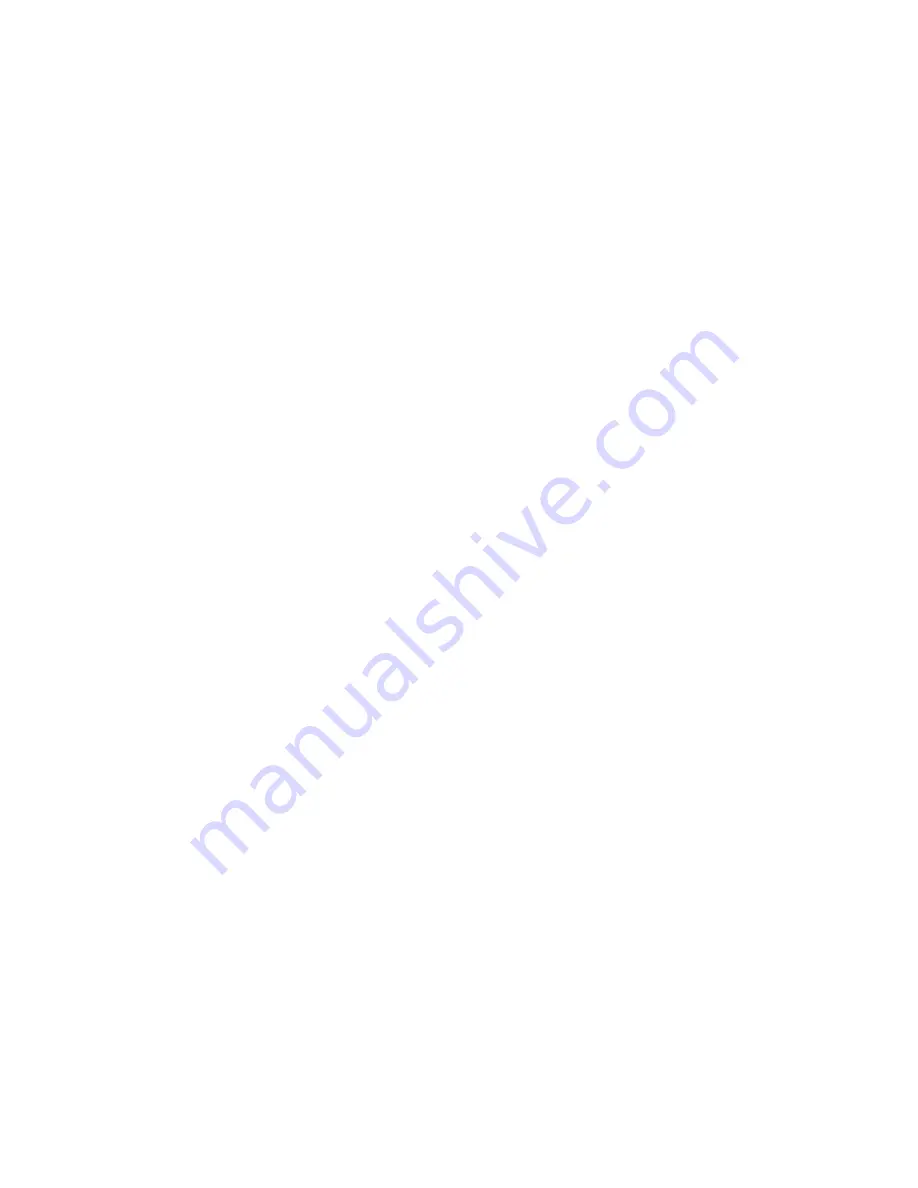
2:5 MEASURING CRANKSHAFT DEFLECTION
a)
Make sure that the cable is properly connected to the instrument.
b)
Select and assemble the required extension bar(s) to achieve the correct length,
tighten firmly by hand and screw into the fine adjustment end of the transducer.
c)
Push OK button. Date and time is shown on the display, accept by pushing OK.
d)
Number of documents stored will appear on the display for 2 seconds (see 2:7).
e)
A New Document will be given a new number consisting of 8 digits.
The first two digits being sequential numbers followed by six date digits.
Together these digits will form the new document number.
f)
Accept crankshaft measurement by pressing OK
g)
Select engine type with left/right arrows ( < / >), or choose USER DEFINED.
To accept press OK. When USER DEFINED is selected, the screen will show “1”.
Click > (“1” flashes slowly) and then OK to start text editor (“1” flashes fast).
To produce your own engine ID, press the > button repeatedly until the first
required letter/number appears, press OK, continue until ID is complete.
Use ^ button for space. Should an error occur, use the < button to step
backwards to correct it. Restart the process with the > button. When the last
letter/number is entered, press OK three times to leave edit mode and go
further to next level. To step backwards to previous menu you have to delete all
letters with the < button to the first position, then press ^ button.
h)
The screen will automatically display ”Engine No 1”, to accept press OK.
Alternatively, to generate your own engine number, use arrow buttons as
described above (g).
i)
Select engine condition ‘warm / cold’, to accept press OK.
j)
Enter correct temperatures (ambient, lubricating oil and cooling water) using
arrow buttons. To accept each temperature, press OK.
k)
Select clockwise / anti clockwise, press OK.
l)
Enter the total number of cylinders (max 24) by using < > arrows, press OK.
m)
Choose the cylinder you want to start with and press OK.
n)
Accept RESET by pressing OK. This reset is to ensure that the instrument collect
a true value from the transducer.
o)
Position the transducer between the webs ensuring the end tips are located
in existing punch marks. Adjust the final length using the fine adjustment
thread until the instrument indicates b / - .500, tighten with locking
ring to maintain fixed length.
p)
Set the instrument to ZERO by pressing OK.
q)
Select position ‘A’ for clockwise rotation and ‘E’ if anti clockwise. With instrument
reading 0,000 mm, rotate the crankshaft to next position and accept the
reading by pressing OK. Continue through the remaining positions of rotation.
r)
When all positions are complete, the instrument will display the next cylinder in
line order, press OK to accept. Alternatively, should you wish to select any other
cylinder number press < / > arrows, then OK.
s)
To remove the transducer, apply pressure against the spring loaded tip of the
transducer, this should allow the extension bar end to be freed from the web
punch marks.
t)
Fit to the next cylinder by compressing the spring loaded end of the transducer
into the punch mark and relocate the bar end tip.