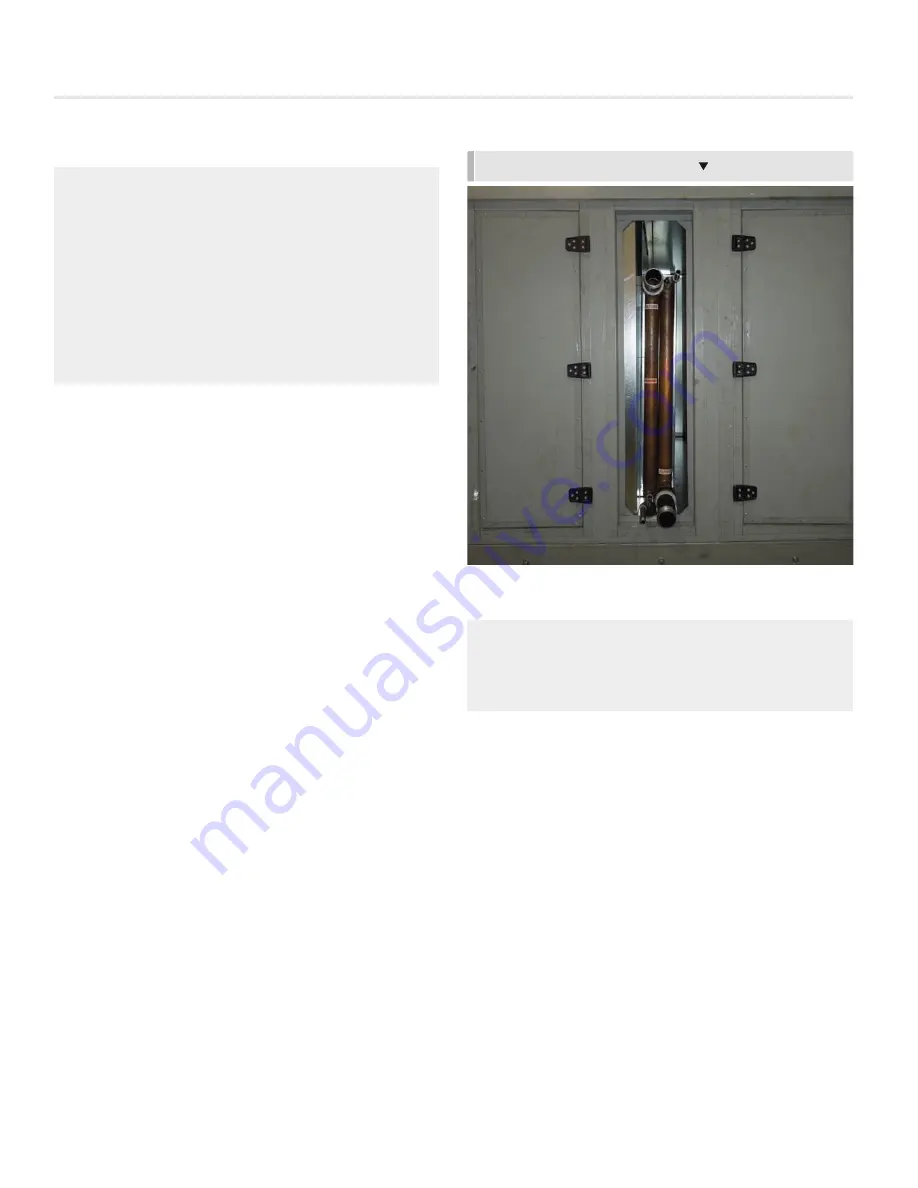
UNIT WITH CHILLED WATER COILS
Cooling Device Condensate Traps
NOTICE - IMPROPER TRAPPING MAY FLOOD UNIT:
Improper
condensate traps may flood the unit leading to damage
of both the unit and the building below. Follow the
instructions below carefully.
The AW-I unit may have an optional DX, chilled water cooling
coil or other condensate producing device in either the
draw through (upstream of the supply fan) or blow through
configuration (downstream of the supply fan) that includes
a condensate pan. Devices that include a condensate pan
will require a field supplied condensate trap. The height
and configuration of the trap will depend on the location
with respect to the supply fan and the supply fan total static
pressure. Particularly in the case of a draw through trap,
improper trapping may stop the condensate from draining and
cause the unit to flood. This can damage both the unit and
building.
Hot Water and Chilled Water Coil Connections
NOTICE - IMPROPER PIPING MAY LEAD TO UNIT AND BUILDING
DAMAGE:
Improper piping on hot water and chilled water
coils may lead to leaks that can damage the unit and the
building. Follow these instructions carefully.
NOTICE - IMPROPER FREEZE PROTECTION CAN LEAD TO
UNIT AND BUILDING DAMAGE:
In climates where freezing
conditions occur, some form of freeze protection must
be followed to avoid coil damage and subsequent leaks
that can damage the unit and the building. Damage from
improper freeze protection will void the warranty.
Some units may include hot water and/or chilled water coils.
Multiple coils may be stacked in the same rack. Indoor
units will have the piping connections stubbed out through
a removable coil access cover. Depending on the unit
configuration, outdoor units will have either a vestibule or
access section with a pipe chase to allow the piping to be
routed into the building. Refer to the submittal drawings for
piping arrangements.
1. All piping connections should be counterflow, with respect
to air flow, with water entering at the bottom and leaving
at the top of the coil. Confirm that the coil can be piped
properly. If not, do not continue piping. Contact your
sales representative.
2. Hot water and chilled water coils are generally not
supplied with any piping or control valves. The installing
contractor is responsible for all field piping and leakage
tests.
3. Stacked coils need to be piped in parallel with reverse
return piping.
4. Route properly-sized piping through the vestibule or pipe
chase to the coils. Include control and isolation valves as
required.
5. Use a backup wrench whenever attaching fittings to the
coils. Failure to do so will damage the coils and void the
warranty.
6. Leak test the unit prior to filling the system. Repair all
leaks and re-test prior to filling the system.
7. Bypass coils during system flush. Failure to do so may
cause debris to be caught in control valves and or the coil.
15
AW-I
INSTALLATION INSTRUCTIONS
priceindustries.com
|
AW-I - Manual