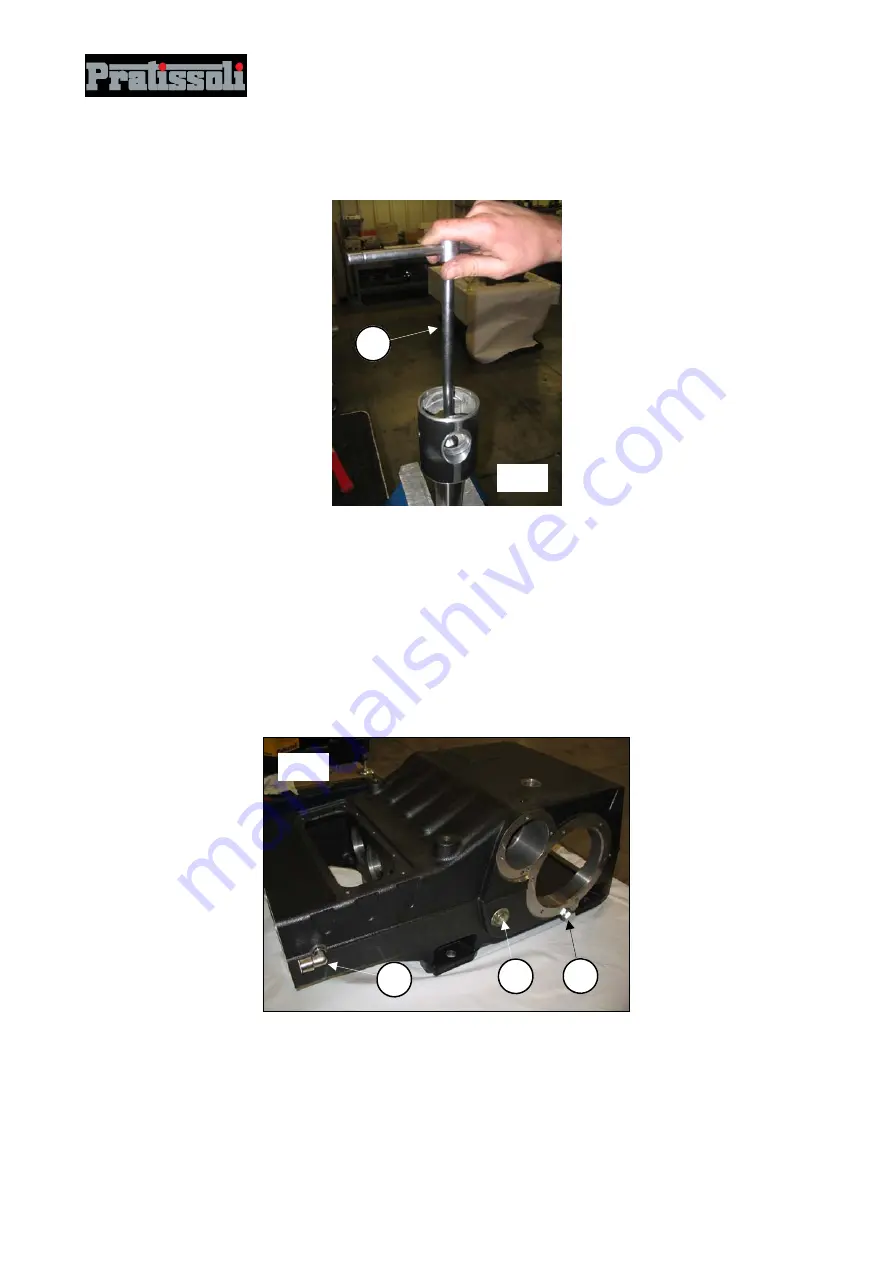
SK
16
To separate the stem from the piston head, it is necessary to unscrew the hexagonal-head M10 screw using
a no. 17 socket wrench (pos.
c
, fig.47).
Complete the dissassembly of the mechanical part by removing the oil level lights, the eyebolts and the 90°
quick-fit connection.
2.1.2 Assembling the mechanical part
Proceed with the assembly, following the reverse of the procedure shown in 2.1.1.
The correct sequence is as follows:
Attach the two oil level lights, the two oil drain plugs and the 90° quick-fit connection (pos.
c
,
d
and
e
fig.48).
fig. 47
1
fig. 48
2
1
3
Summary of Contents for SK Series
Page 1: ...SK 1 SK Series Repair Manual Menu ...
Page 2: ...SK 2 ...