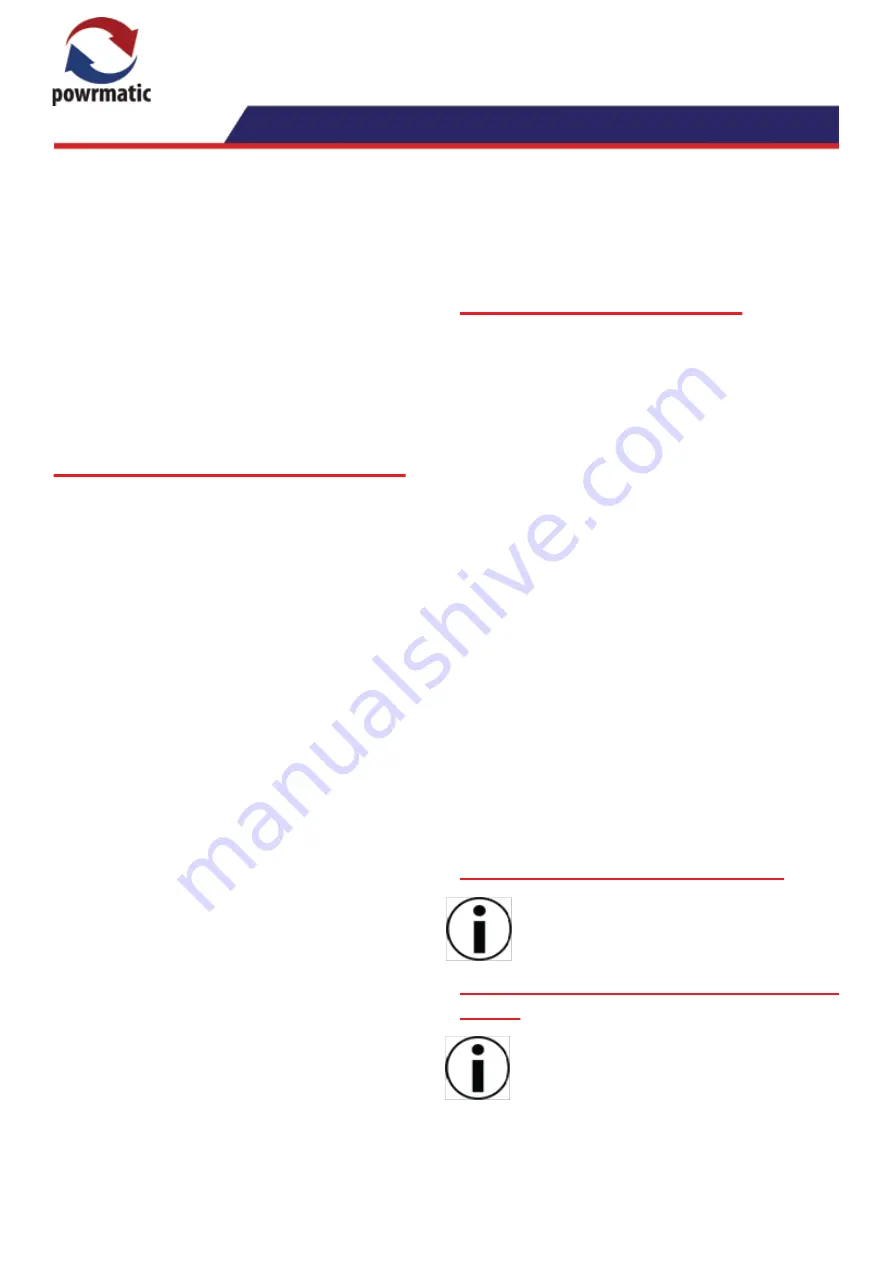
Page 18 NVX Range Users, Instructions & Service Instructions Issue 5.5 August 2015
2.2 Flue/Combustion Air Duct System
The minimum distance between surfaces of the flue pipe
and any surfaces made from combustible materials is
300mm. If it is necessary for the flue pipe to pass through
a structure made from combustible materials a metal
sleeve must be used so that the minimum clearance of
300mm is maintained. The flue and combustion air ducts
supplied with the heater are capable of withstanding their
own weight over the allowable flue lengths. Wall bands
and bracing brackets, or equivalent, must be used to
provide lateral stability and should be used at centres not
exceeding 2.5 metres.
All models are supplied as standard with a rear flue outlet
and the flue outlet and combustion air sockets temporarily
fitted.
2.2.1 Conversion to Top Flue Outlet
1. Remove the two blanking plates from the flue /combus-
tion air openings at the top of the unit.
2. Remove the four screws from the exhaust fan outlet
flange.
3. Remove the screws securing the fan mounting box to
the exhaust header plate.
4. Remove fan assembly and rotate the assembly 90°
anticlockwise.
5 Refit the fan assembly to the exhaust header plate
ensuring that the gasket is not damaged, if necessary
replace or make good with silicon sealant.
6. Secure the exhaust fan outlet flange to the underside of
the top panel and fit the blanking plates to the rear panel.
2.2.2. Fitting Flue/Combustion Air Sockets
1. Apply a bead of silicon sealant around the face of the
flange on the exhaust fan outlet tube that can be seen
from the outside of the heater. Place the flue socket on the
outside of the heater to mate with this flange and clamp
the two flanges together, on either side of the heater panel
using the screws provided. Ensure that the silicon sealant
has sealed between the two flanges.
2. Apply a bead of silicon sealant around the face of the
flange of the combustion air socket, on the same side as
the socket. Passing the socket through the panel from the
inside, position the flange up against the panel. Secure,
from the outside, with the screws provided.
3. If ducted combustion air is not required (see Section
1.2.5. Page 7) fit the mesh inlet plate behind the unused
combustion air inlet hole.
4. Apply silicon sealant and refit blanking plates as
required to seal unused panel holes.
2.2.2. General Requirements
See Figures 1a to 2b, Page 19 & 20 for the different types
of flue installation. In all cases the flue outlet socket must
be connected via the provided flue system to outside air.
The maximum permitted length of flue system is 6m, or
12m if the flue outlet only is used. If an offset is required
two sets of 45° bends should be used each set being
equivalent to 0.5m of flue length. 90° bends may be used
but each set will be equivalent to 1.0m of flue length. The
minimum flue length (end of flue terminal to back or top of
heater) shall not be less than 1.0m for the NVx10 – 50 and
1.3m for the NVx60 - 140.
All outer joints must be finished with the provided locking
bands. A smear of silicon grease to the inside of sockets
will assist in fitting components together. All flue and com-
bustion air ducts must be supported independently of the
air heater. The flue or flue/combustion air terminal must
not be installed so as to be less than:
- 300mm below an opening e.g. window, air brick etc.
- 200mm below eaves or gutter.
- 300mm from an internal or external corner.
- 1200mm from a surface facing the terminal.
- 1500mm vertically from another terminal on the same
wall.
- 300mm horizontally from another terminal on the same
wall.
- 2000mm from ground level.
2.2.3. Installation of Flue System
Note: A terminal guard, as supplied by Powrmatic
Ltd, must be fitted to horizontal flue terminals.
The minimum flue length in all cases is:- 1m
2.2.3.1. Horizontal System - Rear
Outlet
Note: If the outlet is required to the side of the unit
90° bends may be fitted directly onto the inlet/out-
let spigots on the heater.
1. Locate the position of the flue terminal, allowing for a
slight gradient running down from the heater to the termi-
nal of 2° - 3° and cut a hole to suit.
2. Fit the flue terminal, securing via the wall plate and
weather with silicon sealant or similar.
3. Fit the twin to concentric adaptor to the terminal section
and extend the flue and combustion air ducts to the heater
using straight lengths. Fit an adjustable length prior to the
unit, to facilitate flue disconnection for servicing. Extend
the adjustable lengths to make the final connection to the
appropriate heater inlet/outlet spigots.
4. Ensure that internal silicon sealing rings are in place
and that all tubes are pushed fully home. Secure concen-
tric lengths with the locking bands provided.
Notes for all systems.
i) Final overall length of adjustable disconnection
piece must be between 360 - 415mm.
ii) 45° offsets may be used if required. Each set is
equivalent to 0.5m of flue length.
iii) Where NV heaters are used in clean environ-
ments it is permissible to take the combustion air
directly from the heated space. The supplied
mesh intake plate, must be fitted to the combus-
tion air inlet on the rear of the heater.
2.2.3.2. Vertical System - Top Outlet
1. Locate the position of the flue terminal cut a hole in the
roof to suit.
2. Fit the flashing and the flue terminal so that the lower
edge of the outer case is over the top of the flashing.
Weather with silicon sealant or similar.
Fit a condensate drain length into the flue socket on the
heater and an equivalent straight length onto the combus-
tion air socket.
3. Fit the twin to concentric adaptor to the terminal section
and then extend down to the heater using straight lengths.
Fit adjustable lengths as the final connection pieces, to
facilitate flue disconnection for servicing. Extend the
adjustable lengths to make the final connection but do not
exceed the maximum extended length so as to maintain
joint integrity.
Extend the drainage off take of the condensate drainage
length to a suitable gully or drain.
4. Ensure that internal silicon sealing rings are in place
and that all tubes are pushed fully home. Secure concen-
tric lengths with the locking bands provided.
2.2.3.3. Internal Combustion Air
System
1. Complete the run of flue sections from the terminal
spigot to the flue outlet socket of the heater generally as
described in 2.2.3.1. and 2.2.3.2., ensuring that the inter-
nal silicon sealing rings are in place.
2. It is recommended that both air inlets are utilized and
that both are fitted with the mesh inlet plates supplied. In
addition a 90° bend should be fitted to the rear inlet, the
inlet opening of the bend facing to the side of the heater
i.e. away from the main air fan.
2.6.6.1. Standard Units
This is set for the required heat input before despatch. In
the case of Hi/Lo and Modulating units both high and low
pressures are set. Pressures should be checked in the
following manner.
2.6.6.1.1. Standard Units
1. Set external controls to ensure that the main burner is
off.
Open the side access door. Connect a pressure gauge to
the burner pressure test point on the multifunctional
control.
2. Set external controls so as to turn on the main burner.
Compare the measured burner gas pressure to that
stated on the data plate. If necessary adjust the burner
gas pressure by turning the regulator screw anticlockwise
to decrease the pressure, or clockwise to increase the
pressure.
3. In addition it is advisable to check the gas rate using the
gas meter dial pointer. Ensure that no other appliances
supplied through the meter are in operation.
4. If required, after checking or setting the burner pres-
sures, the CO2 content in the flue gases can be checked
by sampling in the first section of flue fitted to the flue
outlet of the unit. Nominal CO2 values are given for guid-
ance in the Table at the bottom of the previous page.
5. Turn off the main burner and disconnect the pressure
gauge and replace the sealing screw. Turn on the main
burner as above and test for gas soundness around pres-
sure test joint using a leak detection fluid e.g. soap
solution.
Governor adjustment screw under cover cap (Honeywell
VK4105A1001B)
Fitted to the NVx 10 to 50
Governor adjustment screw under cover cap
(Honeywell VR4605AB1027)
Fitted to the NVx 60, 75, 90 and 90S
Governor adjustment screw under cover cap (Honeywell
VK425AB1007)
Fitted to the NVx 120 and 140
2.6.6.1.2. High/Lo Regulator
1. Set external controls to ensure the main burner is off.
Open the side access panel. Connect a pressure gauge to
the burner pressure test point on the multifunctional
control.
2. Set external controls to turn on the main burner and
maintain high fire. Compare the measured burner gas
pressure to that stated on the data plate. In addition it
is advisable to check the gas rate using the gas meter dial
pointer ensuring that no other appliances supplied
through the meter are in operation.
3. Repeat 2 above with external controls set to maintain
low fire.
4. If it is necessary to adjust either the high fire or low fire
pressures proceed as follows after levering off the plastic
cover from the Hi/Lo regulator.
Note: High fire setting must be adjusted first after
which the low fire setting can be set. Any adjust-
ment of the high fire setting alters the minimum
setting.
Maximum Setting
With the controls set to high fire use an adjustable or 8mm
spanner to turn the adjustment screw for high fire pres-
sure, clockwise to increase and counter-clockwise to
decrease, until the required pressure is obtained. Turn the
burner On and OFF several times to check the pressure
setting and then turn off.
Minimum Setting
Disconnect electrical connection of high/low regulator and
turn burners back on and wait until the burner pressure
has stabilized. Use a screwdriver to turn the slotted
adjustment screw for low fire pressure, clockwise to
increase and counter-clockwise to decrease, until the
required pressure is obtained. Reconnect high/low regu-
lator and check high fire pressure. Repeat both steps if
necessary and then replace cover cap.
5. Turn off the main burner, disconnect the pressure
gauge and replace the sealing screw. Turn on the main
burner and test for gas soundness around pressure test
joint using a leak detection fluid. Replace access panel.
2.6.6.1.3. Modulating Regulator
1. Set external controls to ensure that the main burner is
off. Open the side access panel. Connect a pressure
gauge to the burner pressure test point on the multifunc-
tional control.
2. Set external controls so as to turn on the main burner
and maintain high fire. Compare the measured burner gas
pressure to that stated on the data plate. In addition it is
advisable to check the gas rate using the gas meter dial
pointer ensuring that no other appliances supplied
through the meter are in operation.
3. Repeat 2 above with external controls set to maintain
low fire.
4. If it is necessary to adjust either the high fire or low fire
pressures proceed as follows after removing the plastic
cover from the Modulating regulator.
Note: Minimum fire setting must be adjusted first
after which the high fire setting can be set. Any
adjustment of the minimum fire setting alters the
maximum setting.
Minimum Setting
Disconnect electrical connection of modulating regulator
and turn burners back on and wait until the burner pres-
sure has stabilized. Turn 9mm adjustment nut for low fire
pressure clockwise to increase and counter-clockwise to
decrease until the required pressure is obtained. Recon-
nect modulating regulator and check high fire pressure,
readjust if necessary.
Maximum Setting
Disconnect electrical connection of modulating regulator
and turn burners back on and wait until the burner pres-
sure has stabilized. Push shaft gently downwards to the
maximum adjustment screw and hold there. Turn 7mm
adjustment nut for high fire pressure, clockwise to
increase and counter-clockwise to decrease, until the
required pressure is obtained. Release shaft. Repeat both
settings if necessary and then replace cover cap.
5. Turn off the main burner, disconnect the pressure
gauge and replace the sealing screw. Turn on the main
burner and test for gas soundness around pressure test
joint using a leak detection fluid. Replace access panel.
2.6.6.2. Modulating Interface Board
Fig 8 Modulating Interface Board
The MIB interfaces between a 0-10VDC control signal
and the modulating regulator. The following are applicable
to this application.
1. The setting of the slide switches 1 & 2 should both be
to OFF.
2. Potentiometer P1 (Default setting 100%)
The control current of the V7335A is controlled by P1,
varying between 50% and 100% of the input signal.
E.g.
-When P1 is set at 100% (fully clockwise) maximum
power (165mA @ 22VDC) is provided to the modulation
coil with a 10VDC input control signal.
-When P1 is set at 50% (fully anticlockwise) maximum
power (165mA @ 22VDC) is provided to the modulation
coil with a 5VDC input control signal.
3. Potentiometer P2
Controls the minimum drop-out voltage between 0% and
40% E.g.
- When P2 is set at 0% the drop-out voltage with an input
control signal of 0-10V-DC is 0.3V-DC.
- When P2 is set at 40% the drop-out voltage with an input
control signal of 0-10V-DC is 4.0V-DC.
4. Potentiometer P3 (Default setting 100%)
Controls the maximum hold-in voltage. Its proportional
value is added to the P2 setting E.g.
- When P2 is set at 0% and P3 is set at 5%, the hold-in
voltage of the burner relay is adjustable between 5% and
100% of the input control signal. If the input control signal
is set at 0-10V-DC the hold-in voltage of the relay is
0.5V-DC.
- When P2 is set at 40% and P3 is set at 5%, the hold-in
voltage of the burner relay is adjustable between 45% and
100% of the input control signal. If the input control signal
is set at 0-10V-DC the hold-in voltage of the relay is
4.5V-DC.
The following table shows the relationship between P2
and P3 settings.
2.6.6.2. Flame Current
1. To measure the flame current connect a multimeter
capable of measuring micro amps as shown in the follow-
ing diagram.
2. Minimum current reading is 0.5mA and normal value
should be 1.5mA or higher.
Fig 8 Flame Current Measurement
2.6.6.3. Air Heater Controls
1. Close the gas service tap and ensure that the gas valve
is heard to close within 1 second and that the lockout light
is illuminated. Note that the heater may attempt five re-ig-
nitions before going to lockout. Open the gas service tap
and reset the unit from lockout.
2. Check that the room thermostat and all automatic
controls are operating satisfactorily.
2.6.7. Fan/Limit Thermostat
Thermostat settings:-
Fan Off
Fan On
Limit
NVx 10-140 86°F/30
o
C 122°F/50
o
C 212°F/100°C
Note: NVx 10 to NVx 75 units have one fan/limit
thermostat whereas NVx 90 to NVx 140 units
have two. The second thermostat is at the oppo-
site end of the heater to the burner/controls end.
The fan circuits are wired in parallel (either
thermostat will turn on the fan) and the limit
thermostats are wired in series (either thermostat
will shut down the burner)
2.6.8. Handing over the Air Heater
Hand these instructions to the user or purchaser for reten-
tion and instruct in the efficient and safe operation of the
air heater and associated controls. Adjust the automatic
controls to those values required by the User.
Finally, advise the user or purchaser that, for continued
efficient and safe operation of the air heater, it is important
that servicing is carried out annually.
In the event that the premises are not yet occupied turn
off the gas and electricity supplies and leave instructional
literature adjacent to gas meter.