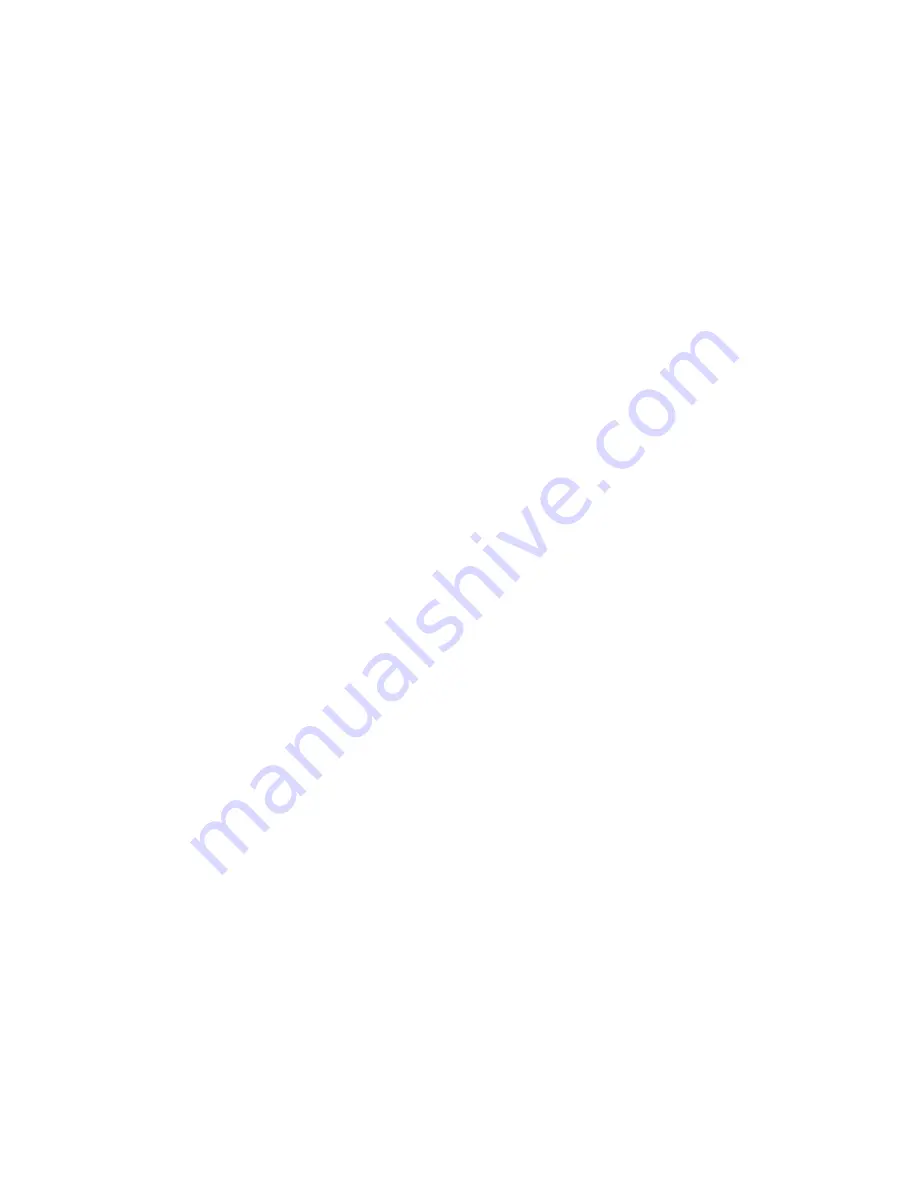
10
4.3 LUBRICANT
1. Oil
Level
Always operate the unit in a level position. Prior to start-up, check the sight glass to ensure the oil in
the pump is at the required level. If the oil level is too low, remove the oil fill plug and
add oil until the
level is at the center of the sight glass
. For approximate oil requirements, see page 14. Do not
overfill or under fill as it could damage the pump.
CAUTION!
The oil level in the pump crankcase
must be checked daily
.
2. Oil
Type
The correct lubricant is essential to the proper operation of your compressor. For single stage or 2-
stage compressors, use
ISO 68, SAE 25 weight oil
. This compressor oil is available at your local
Princess Auto store.
CAUTION!
Do not use motor oil in the compressor pump
.
3. Condensation
Water condensing in the crankcase can occur under certain humid conditions or light duty cycling.
This water must be removed from the pump to prevent damage. Drain the oil and refill.
Condensation can be prevented by allowing the pump to reach its normal operating temperature by
releasing air from the tank and allowing the pump to run, or by using more air, which will cause the
pump to operate more frequently.
CAUTION!
A rise in the oil level and a milky color indicates
that condensation is forming in the crankcase
. This condensation must be drained immediately or
the pump may be damaged.
4.4 PULLEY ALIGNMENT & BELT TENSION
Improper pulley alignment and belt tension are causes for motor overloading, excessive vibration and
premature belt or bearing failure. To prevent this from happening, check the pulley alignment and belt tension
on a regular basis.
Periodically, inspect both the motor and compressor pulleys for oil, grease, nicks or burrs. Clean or replace
pulleys if necessary. Make sure the pulleys are securely fastened. Align the compressor pulley with motor.
The drive belt grooves of both pulleys should be in line with each other. The compressor crankshaft must be
parallel to the motor shaft.
WARNING!
To avoid personal injury, always shut off main power disconnects for the compressor and
relieve all air pressure from the system before performing any service on the air compressor
.
1. Belt
Tension
Proper belt tension and pulley alignment must be maintained for maximum drive efficiency and belt
life. The correct tension exists if a deflection (see A in Figure 4 on the next page) of ½” (13 mm)
occurs by placing 10 lb (4.4 kg) of force (see B in Figure 4 on the next page) midway between the
motor pulley and the pump flywheel. This deflection can be adjusted by the following procedure. The
pulley should be carefully aligned with the flywheel and all setscrews should be kept tight.
Summary of Contents for 11G-2-30H
Page 6: ...6 Figure 3 Compressor Air System...
Page 17: ...17...
Page 30: ...30 8 PUMP PARTS LIST PUMP 10002222 LP205CT USED ON ITEM 8041212...
Page 31: ...31 PUMP 10002222 LP205CT USED ON ITEM 8041212...
Page 32: ...32 PUMP 10002469 LP335SK USED ON ITEM 8120255...
Page 33: ...33 PUMP 10002469 LP335SK USED ON ITEM 8120255...
Page 34: ...34 PUMP 10001977 LPW6548ALHI USED ON ITEMS 8048530 8077513...
Page 35: ...35 PUMP 10001977 LPW6548ALHI USED ON ITEMS 8048530 8077513...
Page 36: ...36 PUMP 10003075 LPSS7550 USED ON ITEM 8120271...
Page 37: ...37 PUMP 10003075 LPSS7550 USED ON ITEM 8120271...
Page 38: ...38 PUMP 10002335 LPV6546ALHI USED ON ITEM 8057739...
Page 39: ...39 PUMP 10002335 LPV6546ALHI USED ON ITEM 8057739...