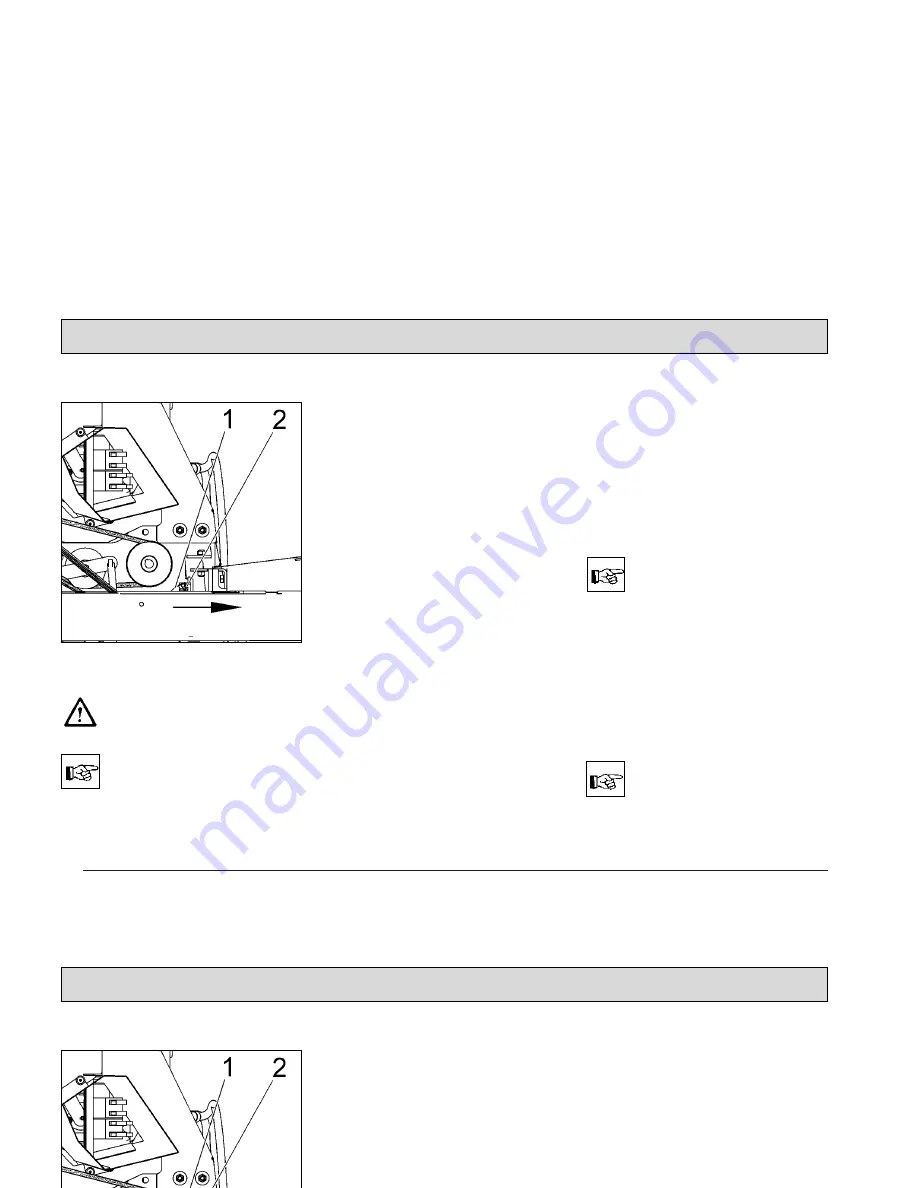
6.9.3 Change Engine Oil
Engine oil changing, right side
of machine
Caution!
Burning hazard at muffler
pipe!
If the machine has not been
used for a longer time, let
the engine run to have the
oil attained appropriate tem-
perature.
Proceed to the following befor
changing engine oil:
- Turn engine off and pull key.
- Secure machine by engaging par-
king brake.
- Open seat hood.
- Loosen quick-release locks (Fig.
20/1).
- Remove cover, filter case (Fig.
20/2).
- Loosen screws at the inside of the
right lateral fairing and remove.
- Lightly tilt lateral fairing to the outsi-
de then remove by pulling up.
- Remove drain hose (Fig. 24/1) from
holding clamp (Fig. 24/2) and lead it
downwards through the vehicle fra-
me.
- Loosen clamp, pull drain plug from
the hose and drain oil.
- Close drain hose (Fig. 24/1) by plug
and protect with clamp.
- Fasten drain hose (Fig. 24/1) at hol-
ding clamp.
- Fill engine oil into check opening
with the machine standing on level
ground.
- Check oil level with dipstick, conti-
nue filling if required
Engine oil: SAE 15 W-40
Filling: approx. 1.1 litre
Use an oil-resistant funnel
for filling engine oil.
6.9.4 Air Cleaner
The air cleaner is located in the engi-
ne's compartment. Clean the foam-
type filter after every 50 hours of ope-
ration and the paper insert after every
100 hours of operation.
Proceed to daily cleaning of
the air cleaner with heavy
dust formation.
48
Maintenance/Service
Fig.24
Direction of travel
6.9.3 Change Engine Oil
Engine oil changing, right side
of machine
Caution!
Burning hazard at muffler
pipe!
If the machine has not been
used for a longer time, let
the engine run to have the
oil attained appropriate tem-
perature.
Proceed to the following befor
changing engine oil:
- Turn engine off and pull key.
- Secure machine by engaging par-
king brake.
- Open seat hood.
- Loosen quick-release locks (Fig.
20/1).
- Remove cover, filter case (Fig.
20/2).
- Loosen screws at the inside of the
right lateral fairing and remove.
- Lightly tilt lateral fairing to the outsi-
de then remove by pulling up.
- Remove drain hose (Fig. 24/1) from
holding clamp (Fig. 24/2) and lead it
downwards through the vehicle fra-
me.
- Loosen clamp, pull drain plug from
the hose and drain oil.
- Close drain hose (Fig. 24/1) by plug
and protect with clamp.
- Fasten drain hose (Fig. 24/1) at hol-
ding clamp.
- Fill engine oil into check opening
with the machine standing on level
ground.
- Check oil level with dipstick, conti-
nue filling if required
Engine oil: SAE 15 W-40
Filling: approx. 1.1 litre
Use an oil-resistant funnel
for filling engine oil.
6.9.4 Air Cleaner
The air cleaner is located in the engi-
ne's compartment. Clean the foam-
type filter after every 50 hours of ope-
ration and the paper insert after every
100 hours of operation.
Proceed to daily cleaning of
the air cleaner with heavy
dust formation.
48
Maintenance/Service
Fig.24
Direction of travel
Summary of Contents for apex 47 g
Page 1: ...Instruction Manual Apex 47 G GH 6502 34 54...
Page 63: ......