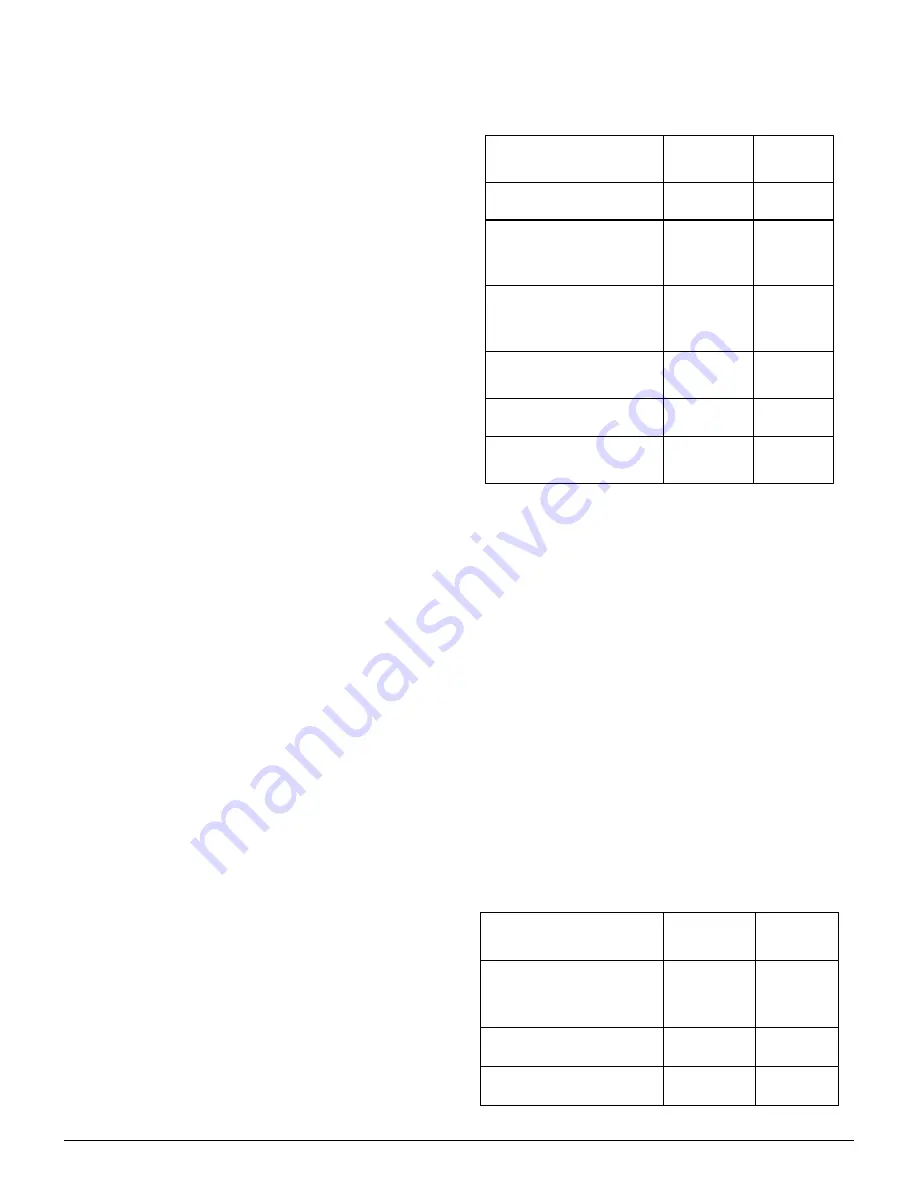
Commissioning - Page 22
3.1 Commission the Boiler
Open Vented Systems -
Remove the pump and flush
the system thoroughly with cold water. Re-fit the pump.
Fill and vent the system then check for leaks.
Sealed Systems - Note:
The system can be filled using
a sealed system filler pump with a break tank or by any
other method approved by the Local Water Authority.
Remove the pump and flush the system thoroughly with
cold water. Re-fit the pump. Fill and vent the system
until the pressure gauge registers 1.5 bar (21.5 lbf/in²)
and check for leaks. Raise the pressure until the safety
valve lifts, this should occur within ± 0.3 bar of the preset
lift pressure of 3 bar. Release water to attain the correct
cold fill pressure.
All Systems
Warning: Before lighting the boiler, ensure that the
outer white case has been correctly fitted and that
the sealing strip fitted to the outer white case is
forming a tight seal with the main boiler chassis.
The controls cover is left off at this stage.
Preliminary electrical system checks. These checks
must be carried out before attempting to light the boiler.
They are:-
Earth Continuity, Short Circuit, Polarity
& Resistance to Earth.
1)
The whole of the gas installation must be checked for
soundness and purged in accordance with BS 6891.
2)
Set the boiler temperature control knob to 'O' Standby.
3)
Turn the boiler gas service cock to the 'On' position and
that the main gas supply is turned 'On'.
4)
Make sure that the system is full of water and that the
pump and radiator isolating valves are open. Vent air
from the system.
5)
Ensure that the main electricity supply is 'On'.
6)
Check that the time control, if fitted, is in an 'On' position
and that the room and cylinder thermostat, where fitted
are set to high temperatures.
First time lighting:
7)
Set the temperature control knob to its maximum setting.
The boiler will attempt to light, if the boiler does not light
within 3 attempts (due to air in the system) the boiler controls
will go to 'Lockout' and the upper Red LED on the control
panel will go to a rapid flashing mode. To re-start the lighting
sequence press the reset button on the control panel. There
will be a short delay before the lighting sequence starts.
When the boiler burner flame has established and the
burner lights the lower Green LED on the user control
panel will be on continuously.
LED Indicators
Status
Green LED
Red LED
Mains ON Only
OFF
ON
Ext. Call for Heat
(Boiler set to STNDBY
Temp. Control set to 'O' Off)
FLASHING
2 Per Sec.
ON
Ext. Call for Heat
(STNDBY switch to ON,
Temp. Control set to Max.)
FLASHING
2 Per Sec.
OFF
Ignition
(i.e. Gas and Sparks ON)
FLASHING
16 Per Sec.
OFF
Boiler Temperature
Control Satisfied
FLASHING
2 Per Sec.
ON
FLAME Detected
ON
OFF
8)
With the main burner running, check for gas
soundness using leak detection fluid.
9)
Allow the system to reach maximum working
temperature and examine for water leaks. Set the
temperature control to 'Standby' and drain the
system whilst still hot.
10) Re-fill and vent the system making a final check for
leaks.
On sealed systems adjust to the correct cold fill
pressure. Set the pressure gauge pointer to the system
design pressure.
If a by-pass circuit is fitted the by-pass valve should be
adjusted with the boiler operating under minimum load
conditions to maintain sufficient water flow through the
boiler to ensure that the overheat thermostat does not
operate under normal conditions.
If the boiler fails to operate
Check the LED indicator fault modes below and refer to
fault finding guide and boiler wiring diagram.
LED Indicators Fault Modes
Status
Green LED
Red LED
Blocking -
Mains Frequency
incorrect or Air Switch
Fault
>1 min. or
Reset
button held
in to force a restart
ON
FLASHING
2 Per Sec.
Earth Fault
or
Mains Reversal
FLASHING
2 Per Sec.
FLASHING
2 Per Sec.
Lockout
OFF
FLASHING
2 Per Sec.
Summary of Contents for Suprima 30
Page 6: ...Installation Requirements Page 6 ...
Page 10: ...Installation Requirements Page 10 Fig 3 Fig 4 ...
Page 12: ...Flue Kits Page 12 ...
Page 13: ...Optional Extras Flues Page 13 Installation instructions included as necessary with each kit ...
Page 14: ...System and Other Kits Page 14 ...
Page 15: ...System and other Kits Page 15 ...
Page 33: ...6 Wiring Diagram Page 33 ...