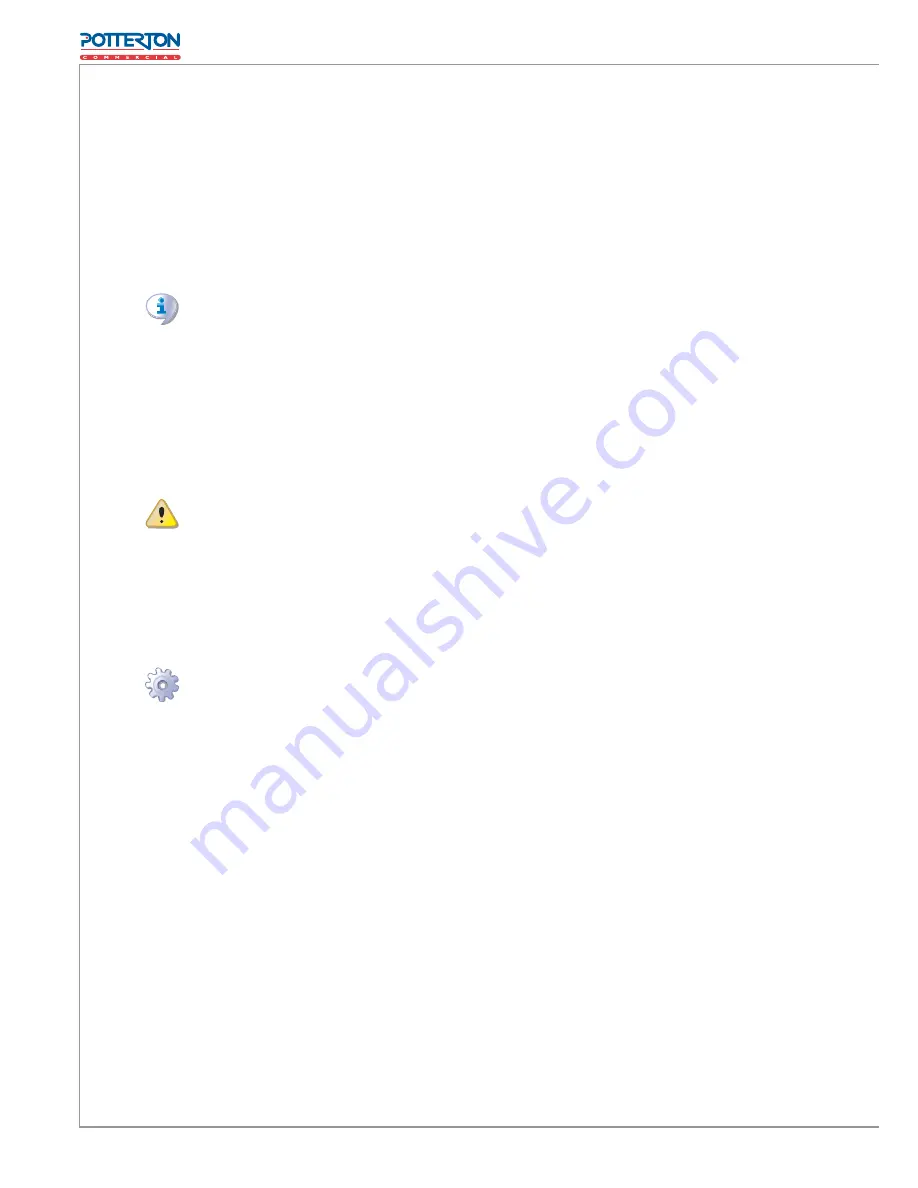
32
• implemented with material capable of resisting a degree of acidity equal to 3 - 5
pH;
• sized to ensure a slope of 10mm per metre of length; if this slope cannot be achieved, a
condensate pump (available as an accessory) must be installed near to the discharge
- see Section 7 ACCESSORIES on page 65;
• implemented in such a way as to prevent the condensate icing in the expected
operating conditions;
• mixed, for example, with domestic effl
uent (washing machine, dishwasher, etc.),
usually of base pH, so as to form a buff er solution before discharge into the sewer.
Do not discharge the condensate into the guttering, since it may ice and corrode the
materials normally used for gutters.
LOADING THE SIPHON
Proceed as follows to load the siphon:
1. Connect the condensate discharge pipe to a drain.
2. Pour 0.2 litres of water di rectly into the fumes discharge pipe and check that the
siphon is full (detail B in Figure 4.3 Position of condensate discharge and manual
reset fumes thermostat on page 31).
If the appliance is operated with the siphon empty, there is a risk of leaks of combusted
gas.
4.6
FILLING OF HYDRAULIC CIRCUIT
After having completed all the connections of the hydraulic, electrical and gas supply
plants, the hydraulic system installation technician can proceed with fi lling the hydraulic
circuit, observing the following stages:
You will need:
the appliance connected hydraulically and electrically.
1. Activate the automatic air bleeding valves present in the plant and open all
thermostatic valves.
2.
Fill the hydraulic circuit, ensuring the minimum water content in the plant,
and adding, if necessary, to the plant water (free of impurities) a quantity of
monoethylene glycol in proportion with the minimum winter temperature in the
installation zone (see table 4.2 Percentage of monoethylene glycol on page 33).
3. Check the fi lter on the return pipe for impurities; clean it if necessary.
4. Check that the siphon on the condense drain has been fi lled with water as indicated
in the relative paragraph.
5. Bring the plant to the correct pressure, making sure that the water pressure is not
less than 1 bar and not over 2 bar, and run the circu lation pump for at least 30
minutes. Check the water fi lter again and clean it if necessary.
To facilitate the operation of bleeding air from the hydraulic circuit, the appliance is
equipped with an additional manual air bleeding valve.
Possible use of glycol antifreeze
Glycols, normally used to lower the freezing point of water, are substances in an
intermediate state of oxidisation which, in the presence of oxidising agents such as
oxygen, are transformed into corresponding acids. This transformation into acids increases
the corrosive nature of the fl uid contained in the circuit. For this reason, mixtures that
are commercially available almost always contain inhibiting substances that are able to