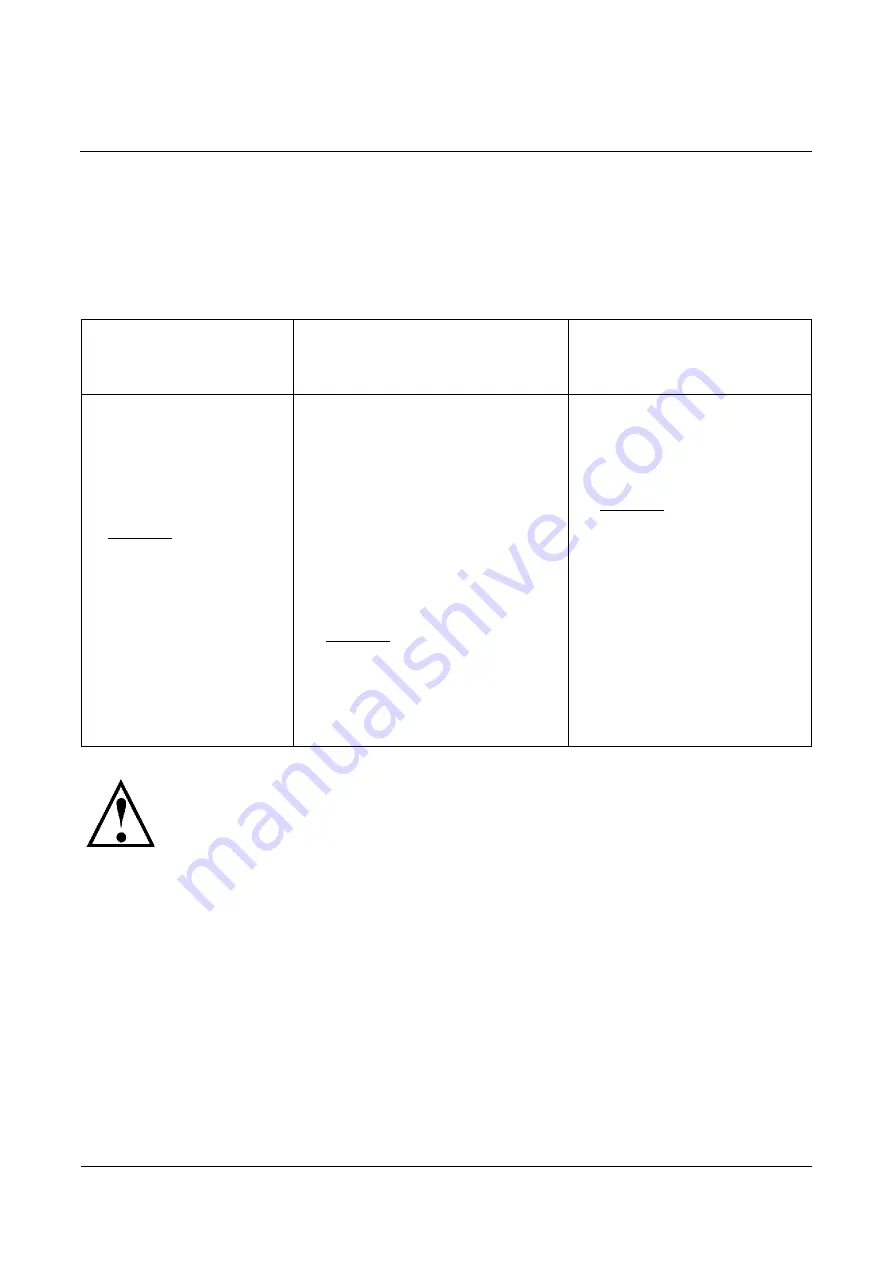
PONNDORF Gerätetechnik GmbH
Leipziger Strasse 374
D - 34123 Kassel
Operation Manual
Hose Pump Series
P_delta / PD-S
Page 23 of 29
Version 003_GB / 04.2021
7.2
Maintenance / Service
To guarantee a constant elasticity of the pump hose it must be lubricated with Ponndorf
Special Grease every 300 hours of operation. To do this remove the casing cover and put
some grease through the opening onto the running surface of the pump hose (e.g. by using
a screw driver).
Outer surface of
the pump hose
Rotor bearings
Teflon rollers
• check on the grease
film (enough grease
on the running surface
of the hose?)
• Interval:
every 300 hours of
operation
• check on proper
seat of bearings
(no radial play!)
• check on unusual
heat generation
• check on unusual
and noticeable
bearing noises
• Interval:
every time when
changing the pump
hose respectively
every 500 hours of
operation
• check for proper seat (no
seized, not worn out)
• Interval:
every 500 hours of
operation
If the rotor bearings / Teflon rollers show the wear characteristics
mentioned above they need to be replaced.
7.3
Cleaning
After pumping media which tend to deposit, the pump hose must be rinsed out when
pumping is finished.
When changing the pump hose the inside of the pump casing should be cleaned properly.
Summary of Contents for P delta 15
Page 1: ...Hose Pump Series P_delta PD S Operation Manual...
Page 2: ......