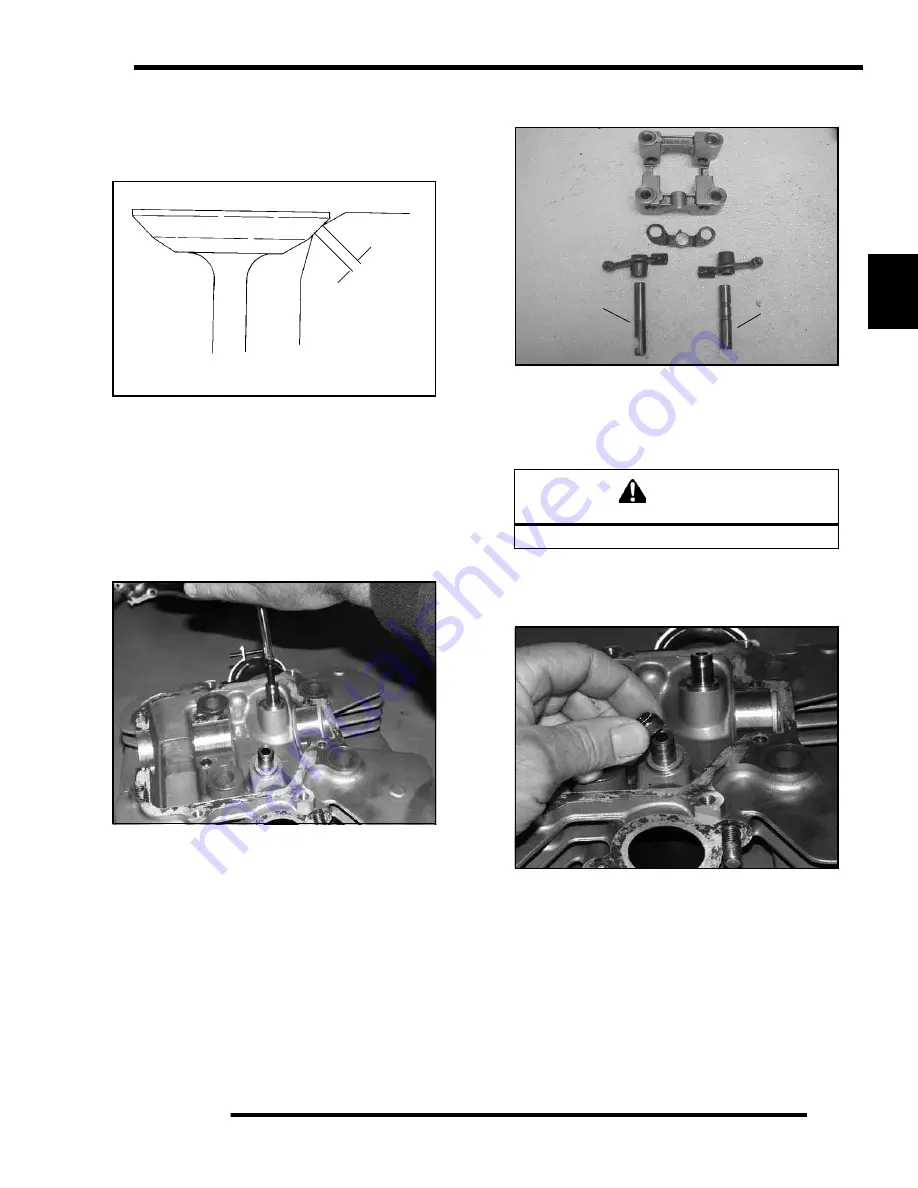
3.21
ENGINE
3
NOTE: When using an interference angle, the seat
contact point on the valve will be very narrow, and is
a normal condition. Look for an even and
continuous contact point on the black marker, all the
way around the valve face.
8.
Clean all filings from the area with hot soapy water, rinse,
and dry with compressed air.
9.
Lubricate the valve guides with clean engine oil, and apply
oil or water based lapping compound to the face of the
valve. Lapping is not required with an interference angle.
10. Insert the valve into its respective guide and lap using a
lapping tool or a section of fuel line connected to the valve
stem.
11. Rotate the valve rapidly back and forth until the cut sounds
smooth. Lift the valve slightly off of the seat, rotate 1/4 turn,
and repeat the lapping process. Do this four to five times
until the valve is fully seated, and repeat process for the
other valve.
12. Clean rocker assembly, cylinder head, valves, and camshaft
oil supply passages thoroughly.
13. Spray electrical contact cleaner into oil passages and dry
using compressed air.
Cylinder Head Assembly
NOTE: Assemble the valves one at a time to
maintain proper order.
1.
Install new valve seals on valve guides.
2.
Apply engine oil to valve guides and seats.
3.
Coat valve stem with molybdenum disulfide grease.
4.
Install valve carefully with a rotating motion to avoid
damaging valve seal.
Seat
Width
CAUTION
Wear eye protection during assembly.
Intake
Exhaust
PartShark.com
877-999-5686
Summary of Contents for R09VA17AA
Page 17: ...2 7 MAINTENANCE 2 RH and LH Side Views P a r t S h a r k c o m 8 7 7 9 9 9 5 6 8 6...
Page 52: ...3 8 ENGINE Oil Flow Diagram P a r t S h a r k c o m 8 7 7 9 9 9 5 6 8 6...
Page 103: ...5 9 BODY SUSPENSION STEERING 5 Body Exploded View P a r t S h a r k c o m 8 7 7 9 9 9 5 6 8 6...
Page 124: ...NOTES BODY SUSPENSION STEERING 5 30 P a r t S h a r k c o m 8 7 7 9 9 9 5 6 8 6...
Page 187: ...WD 1 WIRE DIAGRAM 2009 RANGER RZR 170 P a r t S h a r k c o m 8 7 7 9 9 9 5 6 8 6...