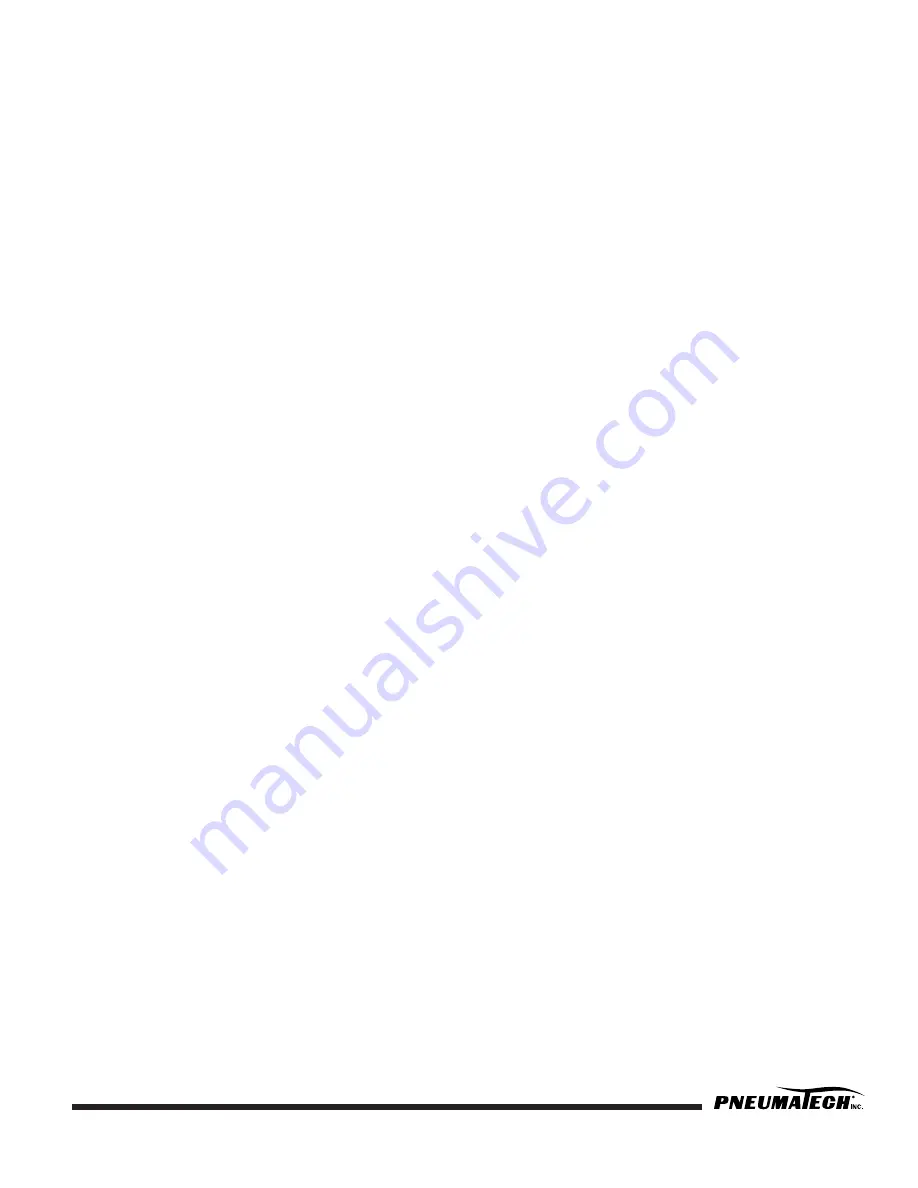
Pub. No. OM-A-10E — April 2004
7
PE & EE SERIES HEAT REACTIVATED AIR
DRYER INSTALLATION & OPERATION
General
1.
Install dryer on a level base, indoors or under a shed.
2.
During shipment, flange and connecting bolts can
come loose. All bolts should be checked and
tightened as needed.
3.
Make sure when the piping is in place that no undue
stress is placed on dryer connections. Union joints or
flexible connections are recommended to relieve
stress. Also, properly support the pipes as needed
with hangers or brackets. Air piping must be
installed by an experienced pipe fitter.
4.
Equip dryer with inlet and outlet isolation valves and
a bypass valve for ease of servicing and start-up.
5.
Connect electric power to the dryer through a
properly sized fused disconnect switch.
6.
Reactivation exhaust may be piped away from the
dryer, making sure proper pipe size is used. The
pipe size should be increased by one size at the
valve, and one additional pipe diameter size for
every ten-foot run to reduce back pressure.
7.
ELECTRICAL CONNECTIONS:
Follow the
recognized local and municipal electrical codes. All
components must be load rated as approved by
NEC, NEMA, CSA and UL.
8.
During shipment, wire connections may become
loose. Per U.L. specification, torque screws inside
enclosure to 20 in-lbs.
9.
GROUNDING:
It is mandatory that the dryer be
grounded. Use an adequate ground with the
conductor sized to NEC.
10.
STORAGE:
In case of extended storage period
before the installation, follow these simple
procedures:
a. Seal or cover all the parts
b. Wrap the electrical enclosure
c. Wrap the mufflers
d. If the desiccant is shipped loose, store it inside to
avoid any rain or water damage.
e. Prior to start-up, check the heater element
resistance. The element (phase) to ground should
exceed the resistance value by 20 megohms. If
this value is not indicated, energize the heater at
low voltage to drive the moisture from the
element insulation. Remove the cover to vent the
moisture from the heater terminal enclosure.
11.
STEAM CONNECTIONS:
For units with optional
steam heat exchanger, the steam connections are
supplied as flanges for both inlet and condensate
return.
12.
WATER CONNECTIONS:
For units with optional
watercooled aftercooler, connect the water supply
and drain lines.
13.
LOW PRESSURE SHUTDOWN FEATURE:
The
electrical control on the air dryer system is set up
with low pressure shutdown switch. The controls and
the heater shall stay de-energized as long as the
dryer system is not pressurized above 50 PSIG. This
feature safeguards the system against the loss of air
flow.
14.
LEAK TEST:
All the dryers are tested at the factory
for any leaks before shipment. An air leak could
develop during transportation or installation.
Pressurize the system and check for any leaks.
Start-Up Procedure
1.
Leave the power switch in the OFF position.
2.
Keeping the dryer isolation outlet valve closed,
slowly pressurize both the adsorbent chambers to the
line pressure.
3.
Check for any leaks in the system.
4.
When both adsorbent chambers are at line pressure,
turn the power switch to the ON position.
5.
One inlet valve will close, and one purge valve will
open and depressurize one adsorbent chamber. This
may take as long as 10 minutes.
6.
Adjust the purge pressure to the recommended setting,
and lock the valve locking mechanism in place.
7.
Slowly open the dryer isolation outlet valve to
pressurize the downstream system.
8.
To check proper operation of the dryer, use the
manual advance button to cycle the dryer through
the valve sequences. When an event occurs (i.e.
valve opening or closing) wait until complete before
again manually advancing the cycle.