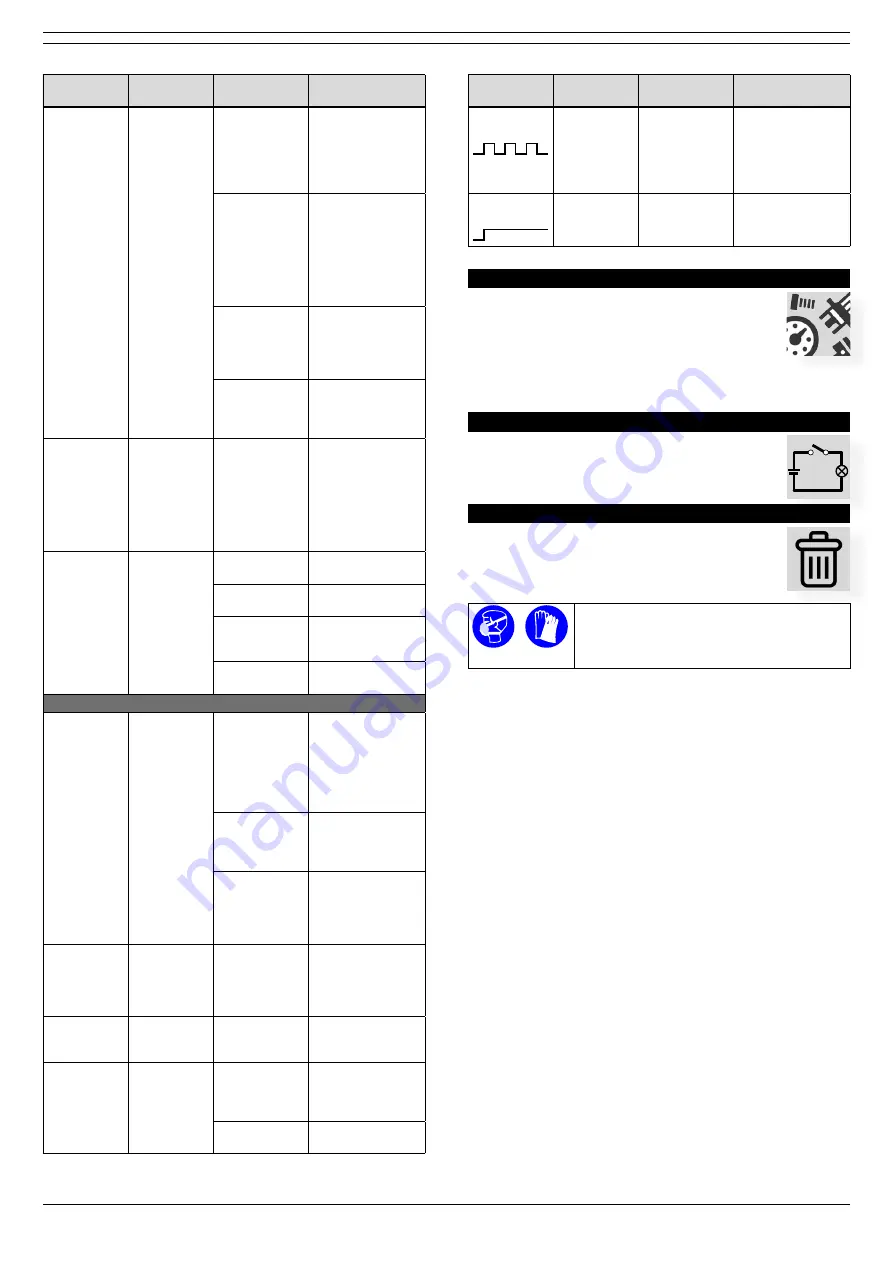
0507060400/010920/M DraftMax Basic | DraftMax Ultra
15
Symptom
Problem
Possible
cause
Solution
Poor
extraction
capacity
Downdraft
table does
not function
properly
Filter cartridges
clogged
Replace both filter
cartridges (refer to
par. 6.2.1).
Replace the HEPA
filter as well (refer
Pressure gauge
defective
(indicates value
below 800 Pa)
Replace the
pressure gauge and
the filter cartridges
(refer to par.
Replace the HEPA
filter as well (refer
Inverted
direction of
rotation of the
motor
Invert the
connection of the
phases to change
the direction of
rotation
Pre and/or
main spark
arresters
polluted
Clean the spark
arresters
Dust or
smoke
coming out of
the outlet
Pollution of
the facility
Filter
cartridge(s)
ripped
Replace both filter
cartridges (refer to
par. 6.2.1) and
clean the outlet
grid.
Replace the HEPA
filter as well (refer
Working light
not working
No light
Main switch off
Turn on main
switch
Cable is not
connected
Connect the cable
Fluorescent
light is
defective
Replace fluorescent
light
Fuse defective
Check fuse F4 and
replace if necessary
DraftMax Ultra only
The fan does
not start
The
downdraft
table does
not function
Automatic
start/stop
(movement
sensor or
welding cable
sensor) not
connected
Connect cable of
automatic start/
Sensor of
movement
sensor
defective
Replace the sensor
Welding cable
sensor not
connected
Connect clamp of
welding cable
sensor to mass
cable of welding
machine
Irregular filter
cleaning
One of the
filter
cartridges is
not being
cleaned
One of the
membrane
valves defective
Replace both
membrane valves
Poor
extraction
capacity
No filter
cleaning
Membrane
valve(s)
defective
Replace both
membrane valves
Button
MANUAL
CLEANING
does not
react
No filter
cleaning
Button
MANUAL
CLEANING
defective
Replace button
MANUAL
CLEANING
PC board
defective
Replace PC board
Symptom
Problem
Possible
cause
Solution
Signal of
alarm light:
Downdraft
table does
not function
properly
Filter cartridges
clogged
Replace both filter
cartridges (refer to
par. 6.2.1).
Replace the HEPA
filter as well (refer
Signal of
alarm light:
Filter cleaning
system does
not function
No compressed
air available
Connect/repair the
compressed air
supply
8
SPARE PARTS
8.1
Filter unit
The following spare parts are available for the
downdraft table;
- refer to exploded view Fig. IV on page 18 and spare parts
9
ELECTRICAL DIAGRAM
Refer to the separately supplied electrical diagram.
10
DISPOSAL
Dismantling and disposal of the downdraft table
must be done by qualified persons.
Personal protective equipment (PPE)
Wear respiratory protection and protective
gloves when you dismantle and dispose of
the unit.
10.1 Dismantling
To safely dismantle the downdraft table, obey the safety
instructions that follow.
Before dismantling of the downdraft table:
- disconnect it from the mains
- disconnect it from the compressed air
- clean the outside
During dismantling of the downdraft table:
-
make sure that the area is sufficiently ventilated, e.g. by a
mobile ventilation unit
After dismantling of the downdraft table:
- clean the dismantling area
10.2 Disposal
Dispose of the pollutants and dust, together with the used
filter cartridges, in a professional manner in accordance with
federal, state or local regulations.