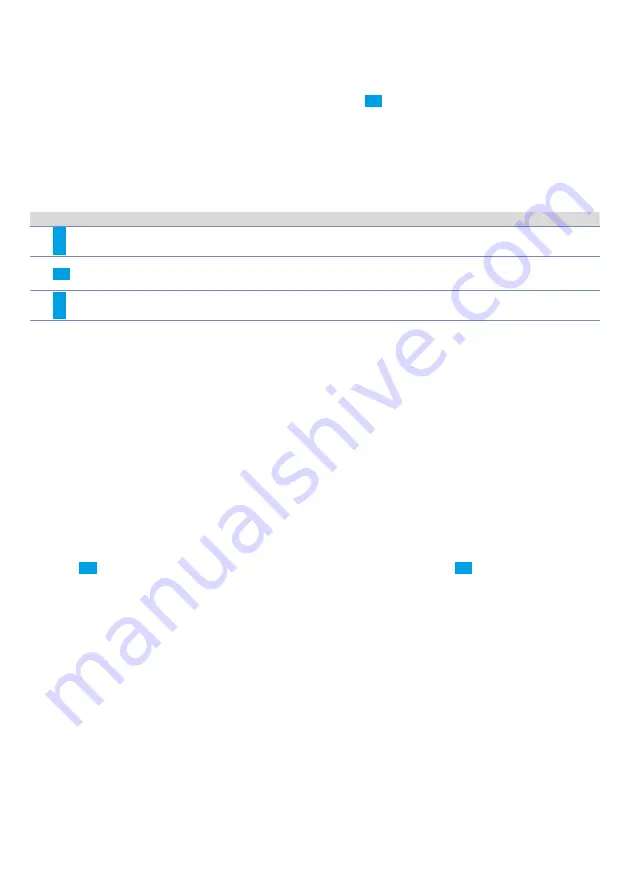
14 - ATR244 -
User manual
7.3
Remote setpoint by serial input
It is possible to enable remote setpoint function selecting
en.ser.
or
en.se.t.
on par. 56
rem.s.
The
remote setpoint must be written on the word modbus 1249 for the command 1 and 1250 for the
command 2 (with tenth of degree if the command process is a temperature sensor).
It is possible to switch from remote to local sepoint pressing
SET
for 1 second. In remote setpoint mode
the led
REM
is ON (if there is serial communication), it flashes when switching to local setpoint mode.
At restarting the controller keeps set in remote setpoint mode (the setpoint value is initialized to 0).
8
Controller Functions
8.1
Modification of main and alarm setpoint value
Setpoint value can be modified from keyboard as follows:
Press
Display
Do
1
Value on display 2 changes.
Increases or decreases the main setpoint
value.
2
SET
Visualizes the other setpoints on display 1.
Display 2 shows the setpoint type.
3
Value on display 1 changes.
Increases or decreases the alarm setpoint
value.
8.2
Automatic Tune
Automatic tuning procedure allows a precise regulation without delving into the PID regulation
algorithm. Selecting Auto on par. 73
tun.1
(for the regulation loop 1), or on par. 98
tun.2
(for the
regulation loop 2), the controller analyzes the proces oscillations and optimizes the PID parameters.
Led
TUN
flashes.
If the PID parameters are not yet selected, at the device switch-on, it is automatically launched the
manual Tuning procedure described into the next paragraph.
8.3
Manual Tune
Manual procedure allows the user greater flexibility to decide when to update
PID algorithm parameters. During the manual tuning, the device generates a step to analyze the
system inertia to be regulated and, according to the collected data, modifies PID parameters.
After selecting
Manu.
on par. 73
tun.1
, or on par. 98
tun.2
, the procedure can be activated in three ways:
• Running Tuning by keyboard:
Press
FNC
until display 2 shows tunE with display 1 on dis. and then press
SET
: display 1 shows Enab.
Led
TUN
switches ON and the procedure starts.
• Running Tuning by digital input:
Select t
unE
on par. 231
d.i.1.F.
(or on par. 239
d.i.2.F.
, par. 247
d.i.3.F.
, par. 255
d.i.4.F.
). At first activation
of digital input (commutation on front panel) led
TUN
led switches on and at second activation
switches off.
• Running Tuning by serial input:
Write 1 on word modbus 1216 (command 1) or 1217 (command 2): led
TUN
switches ON and the
procedure starts. Write 0 to stop the tuning.
To avoid an overshoot, the treshold where the controller calculates new PID parameters is determined
by this operation:
Tune threshold = Setpoint -
“Set Deviation Tune”
(par. 74
s.d.t.1
or par. 99
s.d.t.2
)
Ex.: if the sepoint is 100.0∞C and the Par.32
s.d.t.1
is 20.0∞C the threshold to calculate PID parameters
is (100.0 - 20.0) = 80.0∞C.
For a greater precision on PID parameters calculation it is suggested to start the manual tuning
procedure when the process deviates from the setpoint.
Summary of Contents for ATR244
Page 1: ...ATR244 Controller Regolatore Quick start guide Guida breve all installazione...
Page 2: ......
Page 132: ...132 ATR244 Manuale d uso...
Page 146: ...146 ATR244 Manuel d utilisation Notes Mises jour...
Page 147: ......