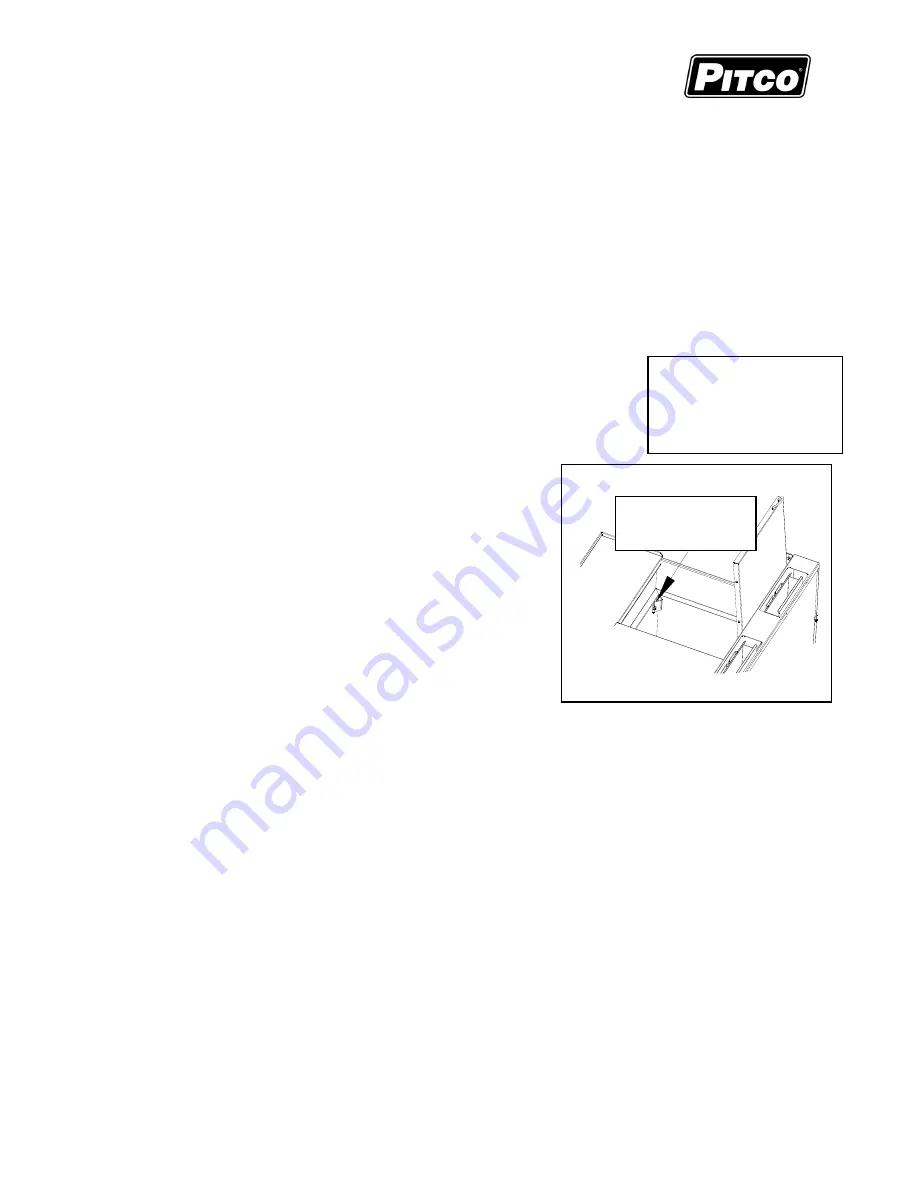
PREVENTATIVE MAINTENANCE
20
L20-376, rev. 1 (08/18)
WARNING
The power supply must
be disconnected before
cleaning and servicing
this appliance!
3.2.1. DELIMING
1. Read the “operation” section of this manual prior to filling or operating the appliance.
2. Following the manufacturer’s de-liming instructions, remove deposits from the tank’s interior.
3. When cleaning is complete, rinse the inside of the tank and its components thoroughly with
cool water. Continue to rinse at least twice or until the cleaner has been completely and
thoroughly rinsed from the tank.
4. Using a clean dry cloth, wipe out all of the water.
3.3. ANNUAL/PERIODIC
PREVENTATIVE MAINTENANCE AND INSPECTION
This section should ONLY be performed by a qualified service technician as part of a regular kitchen
maintenance program. This inspection should take place a minimum of once a year by a Pitco
Authorized Service Technician. It may be necessary perform this inspection more then once a year.
3.3.1. TEMPERATURE PROBE & HIGH LIMIT PROBE SENSORS
Verify probes are in good working condition. Check for damage
and that the fasteners securing the sensors to the tank are tight,
see page 9.
Verify compression fittings are leak free.
Check wiring for damage and loose connections.
3.3.2. CONTROLLER
Perform the following inspection if the appliance is
equipped with a temperature controller.
Verify that the controller is in good operating
condition. Check all lights, displays and switches to
ensure that they are working properly. Ensure the
overlay surface is free of damage.
Check for loose electrical connections.
Verify simmer temperature at 1” above controller
probe, if necessary check probe resistance.
Check liquid level control to ensure that the appliance
stops heating when the water level is low. When the
water level is low, the appliance should automatically
refill to the sensors.
3.3.3. CONTROL PANEL & ELECTRICAL COMPONENTS
Verify that all components (transformer, terminal block, relays, switches, etc.) are in good
condition. Verify all wiring is free from damage, and that there are no loose connections.
Verify that all electrical components are free of any water damage or contamination.
Verify that all covers and panels are free of damage and are properly installed.
Verify power cord is in good condition. Verify that the insulation is in good condition and the
connection to the appliance is tight.
3.3.4. TANK
Verify that the tank is in good condition. Check for scale build up and inspect for signs of
corrosion. Verify that tank is leak free. Check drain overflow (if equipped) for scale build up
and debris blockage.
3.3.5. DRAIN
SYSTEM
Verify that drain valve is in good condition. Check for leaks in the seal area and fitting region.
Verify that drain lines are leak free, kink free and in good condition. Check for scale build up
and debris blockage. Verify that the clamps and connections are securely tightened.
3.3.6. GAS COMBUSTION SYSTEM
Check for gas leaks.
Check and clean vent tube on gas valve pressure regulator.
Check burners, clean debris and grease from pilot and pilot orifice tips.
Check and adjust burner manifold gas pressure to information plate rating.
Liquid Level
Sensors