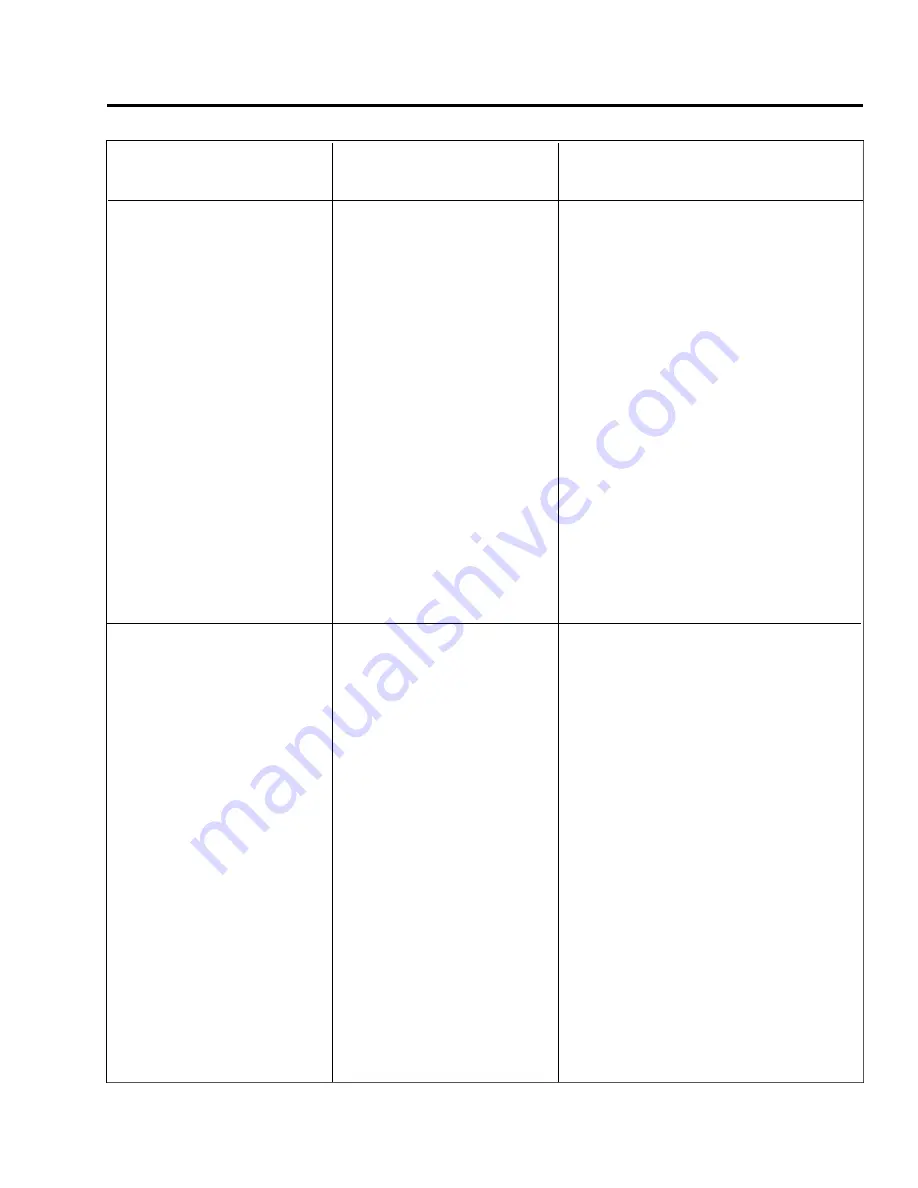
Trouble
Cause
Remedy
Failure of engine to
Incorrect carburetor idle
Adjust throttle stop to obtain
idle properly.
adjustment.
correct idle.
Idle mixture.
Adjust mixture. Refer to engine
manufacturer's handbook for
proper procedure.
Leak in the induction system.
Tighten all connections in the
induction system. Replace any
parts that are defective.
Low cylinder compression.
Check cylinder compression.
Faulty ignition system.
Check entire ignition system.
Open primer.
Lock primer.
Improper spark plug
Check spark plug gap.
setting for altitude.
Dirty air filter.
Clean or replace.
Low power and uneven
Mixture too rich; indicated
Check primer, Readjustment
running engine.
by sluggish engine operation,
of carburetor indicated.
red exhaust flame and black
smoke.
Mixture too lean, indicated
Check fuel lines for dirt
by overheating or backfiring.
or other restrictions. Check
fuel supply.
Leaks in induction system.
Tighten all connections.
Replace defective parts.
Defective spark plugs.
Clean or replace spark plug.
Defective thermostats.
Replace.
Defective temperature gauge.
Replace gauge.
Excessive blow-by.
Usually caused by weak or
stuck rings. Overhaul.
Improper engine operation.
Check entire engine.
PIPER AIRCRAFT
PA-28-161 CADET
AIRPLANE MAINTENANCE MANUAL
Issued: FEBRUARY. 28, 1989
POWER PLANT
1K16
TABLE Vlll-ll. ENGINE TROUBLESHOOTING CHART (cont)