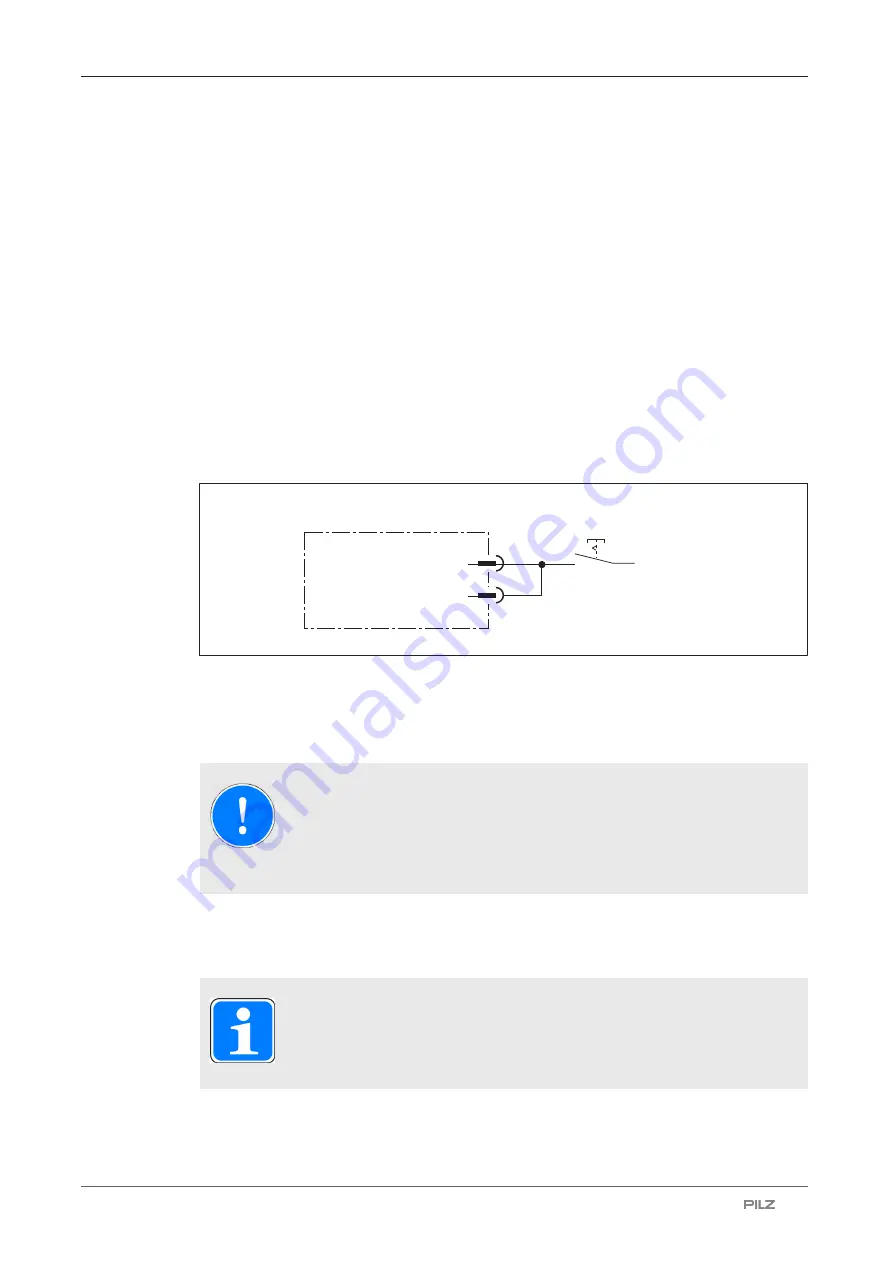
Wiring
Operating Manual PSENvip RL D P Set
1001641-EN-09
| 58
EMC
}
Avoid interference (e.g. from motors, power lines) by laying cables in a way that is EMC-
compliant.
Inputs on the receiver
}
The inputs
Protected field mode 1/Protected field mode 2
are safety-related.
– The CNC or safety system provides the signal. It is only absolutely necessary to con-
nect the inputs to a safety system if communication is needed for tool detection.
– When driven via relay contacts it is the user's responsibility to apply an appropriate
safety concept.
The inputs for protected field mode 1 and protected field mode 2 can be switched directly
via the 24 VDC supply. In this case, both inputs should be linked. Only the following pro-
tected field modes are possible:
– "Standard" protected field mode (switch open, both inputs = "0")
– "Box bending with back gauge" protected field mode (switch closed, both inputs = "1")
Protected field mode 2
Protected field mode 1
X1
3
4
24 V DC
Fig.: Protected field mode 1/2 directly at the 24 V DC supply
}
The input to acknowledge the specified protected field mode can be switched directly via
the 24 VDC supply.
NOTICE
The acknowledgement button for the protected field mode must be posi-
tioned outside the danger zone in such a way that the operator can see all
of the danger zone.
Function test
}
When the wiring is complete the protective equipment will need to undergo a function
test.
INFORMATION
To perform the function test, follow the procedure described in Chapter 7,
"Commissioning", section entitled "Function test of the safety device".