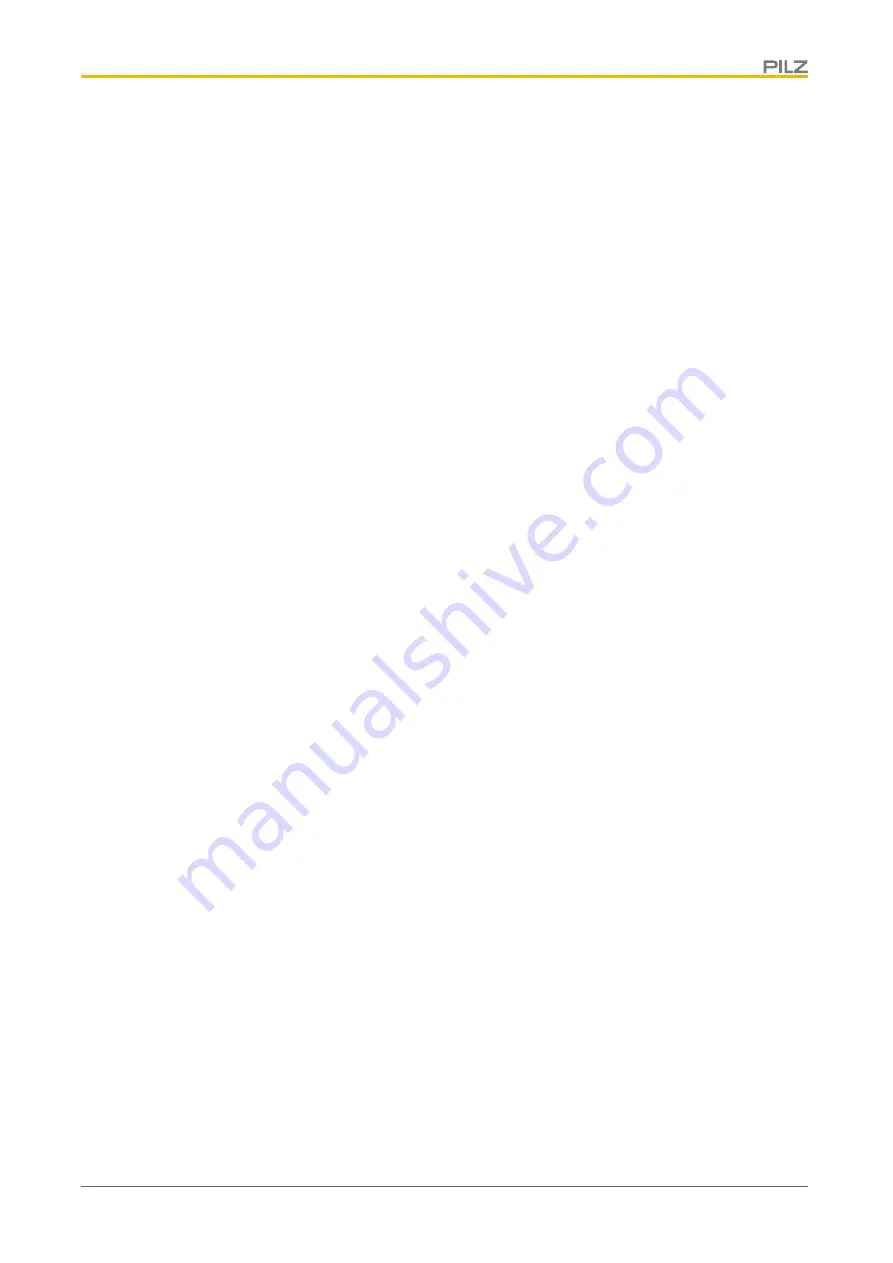
Wiring
Operating Manual PMI v704e/v707e
1003980-EN-02
24
6
Wiring
6.1
General wiring guidelines
}
Electrical or electronic components which could cause interference (contactors, thyris-
tors, relay coils and solenoid valve coils) should be physically separate from data lines.
We recommend you use a sheet metal (MU metal) bulkhead between both areas.
}
Data lines and power lines should be laid separately to avoid capacitive and inductive
interference (recommended minimum distance = 10 cm/3.94")
}
Shielded data cables should also be laid in a different cable duct to the main power
cables.
}
Power cables should be as short as possible.
}
Power cables should be twisted pair cables.
}
Use only a max. length of 3 m for the USB cable, to guarantee reliable data transfer.
}
UL requirement: Only use copper wiring that will withstand 60/75°C for the supply
voltage; maximum torque setting: 0.5-0.6 Nm.
6.1.1
Shielding
}
Connect the network cable shields with low impedance to earth.
}
Use shielded data lines only.
}
Use equipotential bonding cables.
}
Perform a potential isolation.
}
Data line shielding should be connected to a cable shield bus bar.
}
The connection between the cable shield bus bar and the control cabinet/system should
be as short as possible and with low impedance.
}
Fasten the braided screening to the bus bar over a largest surface area as possible
(e.g. with metal hose clips or polyurethane (PU) cable clips).
6.1.2
Measures to protect against interference voltages
}
Wire-up inductive loads (e.g. contactor coils, relay coils and solenoid valve coils) using
suppression elements (e.g. RC networks). This is particularly important if these induct-
ive loads are very close to the power supply or are fed from the same supply.
}
If strong magnetic fields are present, we recommend you use a bulkhead separator, i.e.
metal sheet (MU-metal).