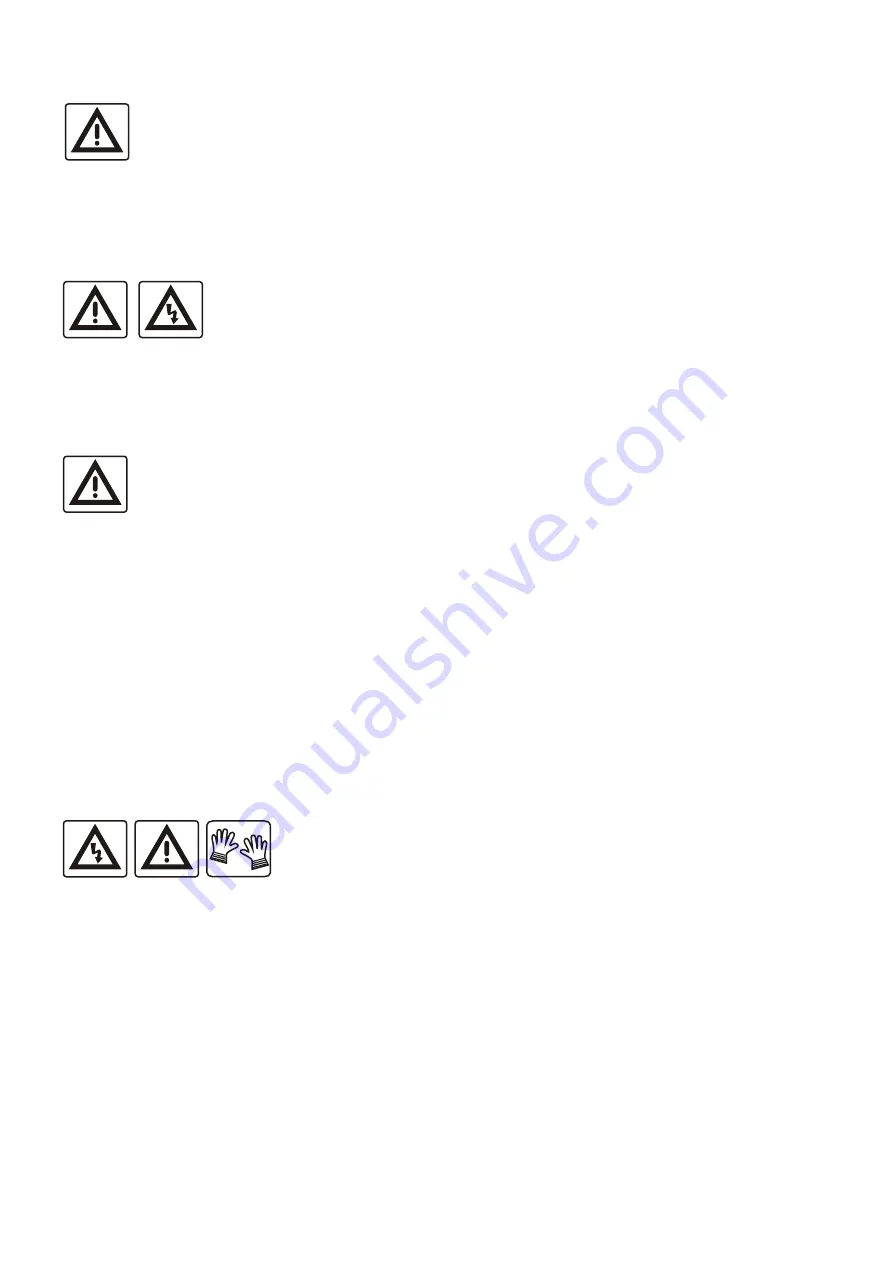
4.2. Machine installation
Failure to observe this causes the bandsaw drive motor and the coolant pump running in wrong
directions. Possibility of machine destruction!
Make sure that the voltage of the electrical grid, voltage protection and connection voltage is according to requirements in chapter 3.
Technical data. When connecting machines into the electrical grid 3NPe, 50 Hz, 400 V, TN-S notice carefully the
colored cables
marking
:
L1
Black,
L2
brown,
L3
black,
N
blue,
P/E
yellow/green.
In case of wrong connection of neutral or protective cable the
machine electric parts may be damaged and injury by electrical current may occur!
The lead-in cable of the machine should be
connected to a protected 16 A socket, in case of a direct connection to the mains the cable should be provided with a lockable main
switch. In case of wrong direction of turning of the motor switch together cables L1 black and L2 brown.
This work may only be carried out by electricians!
4.3. Connection to energy supplies
The machine may be operated in the ambient temperature b5° and +40°C. The average temperature must not exceed
+35°C over the period of 24 hours. In temperatures below +5°C the conventional coolant should be replaced by a fluid working with
respective temperatures.
Protect the machine against humidity, rain and dust!
5. Machine description
5.1. Band guide
Before and after the cut the saw band is guided in two guide heads provided with eccentrically arranged bearings enabling an easy
setting of the band in comparison with the guiding on moving wheels and guided in the hard-metal guides on both sides and on the
upper band edge. The right-hand guide head is fixed. The left-hand guide head mounted on the guide bar is moving and is fed as
close as possible to the work. It is provided with a protective cover as far as the machining zone.
5.2. Band exchange, tensioning and adjustment
Caution! It can only be done when the main switch is off and secured against switching
on again or when the machine is disconnected from the mains.
Caution! Danger of injury by the sharp band teeth. Use protective gloves. Do not
touch the guide wheels and the band.
To achieve perfect cutting function, surface quality and workpiece correct measures, in time band exchange is needed. Blunt blade
may cause higher energy consumption, inclined cuts and cut surface roughness. One of the most important factors for band life time
and the cut quality is the band correct and enough tensioning.
Turn OFF the main switch and secure the machine against switching ON again during band exchange. Close the oil damper valve
(see chapter 5.6.). Raise the arm to position 20 mm above vice fixed jaw. Take off the arm rear cover. Loosen the tensioning handle
and the tensioning wheel and thus the whole band. Take off the band from the running wheels and out of the guide heads (see chapter
5.3.). Insert the new band in the guide heads. Put the band on the running wheels and tighten the tensioning handle so that the
belleville washers will be pressed completely (no light going through them). Close the band cover, turn ON main switch and witch the
speed to the minimum. Press start the button to run the band so it turns one round. Turn OFF a main switch and secure the machine
against running again. Open the band cover and check if the band is correctly guided on the running wheels (see a picture below). If
the band is not correctly set on the running wheels loosen the tensioning handle and with a wheel swing screw correct (see picture
below). Tighten the tensioning handle again. Close the band cover. Exam the band run again. Turn OFF main switch, open band
cover and check the setting of band on the running wheels. According to need repeat this cycle till the band is set on the running
wheels properly. Then close the band cover turn ON main switch and make first cut.