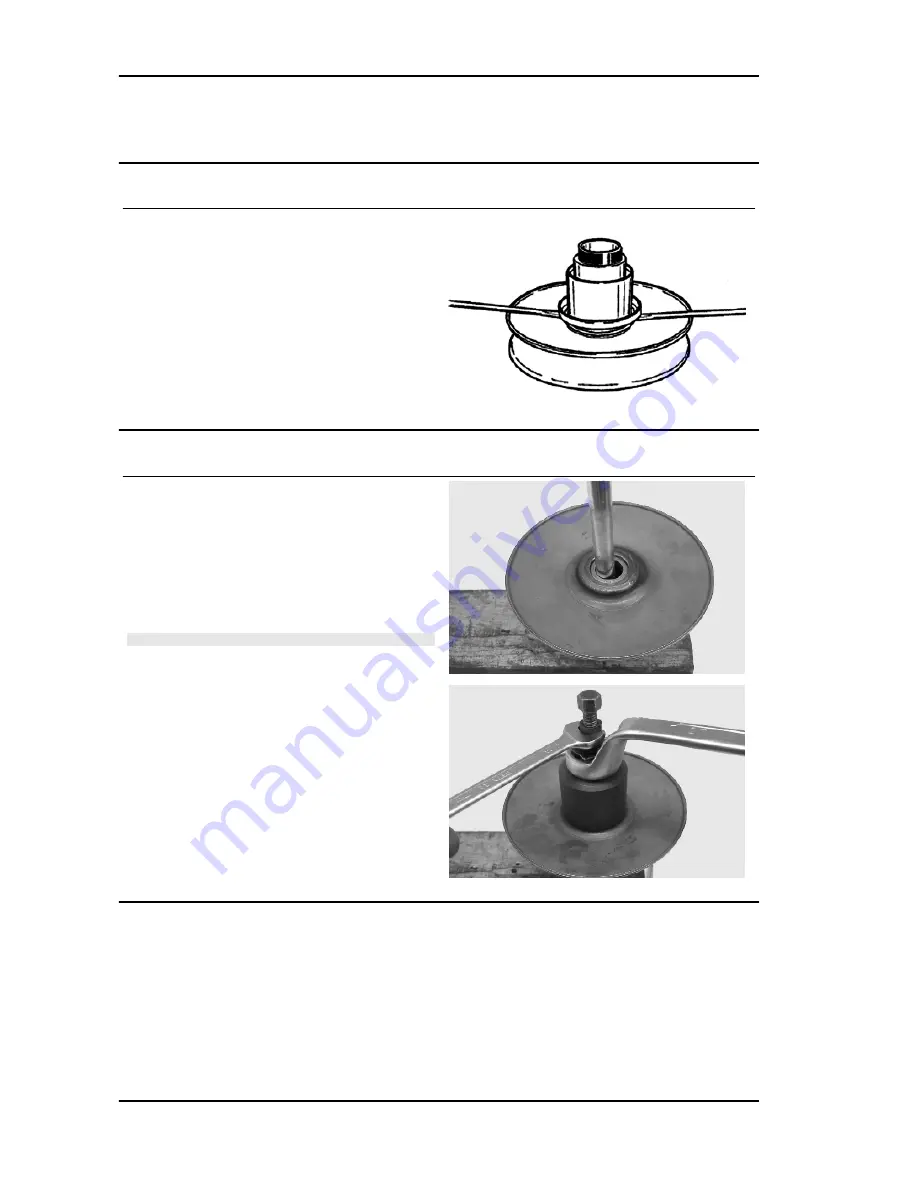
1 mm
Pin retaining collar
- Remove the collar with the aid of 2 screwdrivers.
- Remove the 3 guide pins and the movable half-
pulley.
Removing the driven half-pulley bearing
- Remove the retaining ring using two flat blade
screwdrivers.
- Using a hammer and pin, knock the ball bearing
out as shown in the figure.
- Remove the roller bearing using the specific ex-
tractor.
N.B.
REST THE HALF-PULLEY ON A WOOD SURFACE TO
AVOID DAMAGING THE THREADED RINGLET OF THE
DRIVEN PULLEY UPON REMOVING IT.
Specific tooling
020375Y
Adaptor 28 x 30 mm
020376Y
Adaptor handle
020439Y
17 mm guide
Engine
Liberty 125 - 200 4tempi
ENG - 70
Summary of Contents for Liberty 125
Page 1: ...WORKSHOP MANUAL 633120 Liberty 125 200 4tempi...
Page 4: ......
Page 6: ...INDEX OF TOPICS CHARACTERISTICS CHAR...
Page 18: ...INDEX OF TOPICS TOOLING TOOL...
Page 28: ...INDEX OF TOPICS MAINTENANCE MAIN...
Page 34: ...INDEX OF TOPICS TROUBLESHOOTING TROUBL...
Page 40: ...INDEX OF TOPICS ELECTRICAL SYSTEM ELE SYS...
Page 61: ...INDEX OF TOPICS ENGINE FROM VEHICLE ENG VE...
Page 64: ...INDEX OF TOPICS ENGINE ENG...
Page 116: ...Conceptual diagrams Engine Liberty 125 200 4tempi ENG 116...
Page 138: ...INDEX OF TOPICS SUSPENSIONS SUSP...
Page 144: ...INDEX OF TOPICS BRAKING SYSTEM BRAK SYS...
Page 152: ...INDEX OF TOPICS CHASSIS CHAS...
Page 165: ...INDEX OF TOPICS PRE DELIVERY PRE DE...
Page 169: ...INDEX OF TOPICS TIME TIME...
Page 184: ...Transmission cover Starter motor Time Liberty 125 200 4tempi TIME 184...