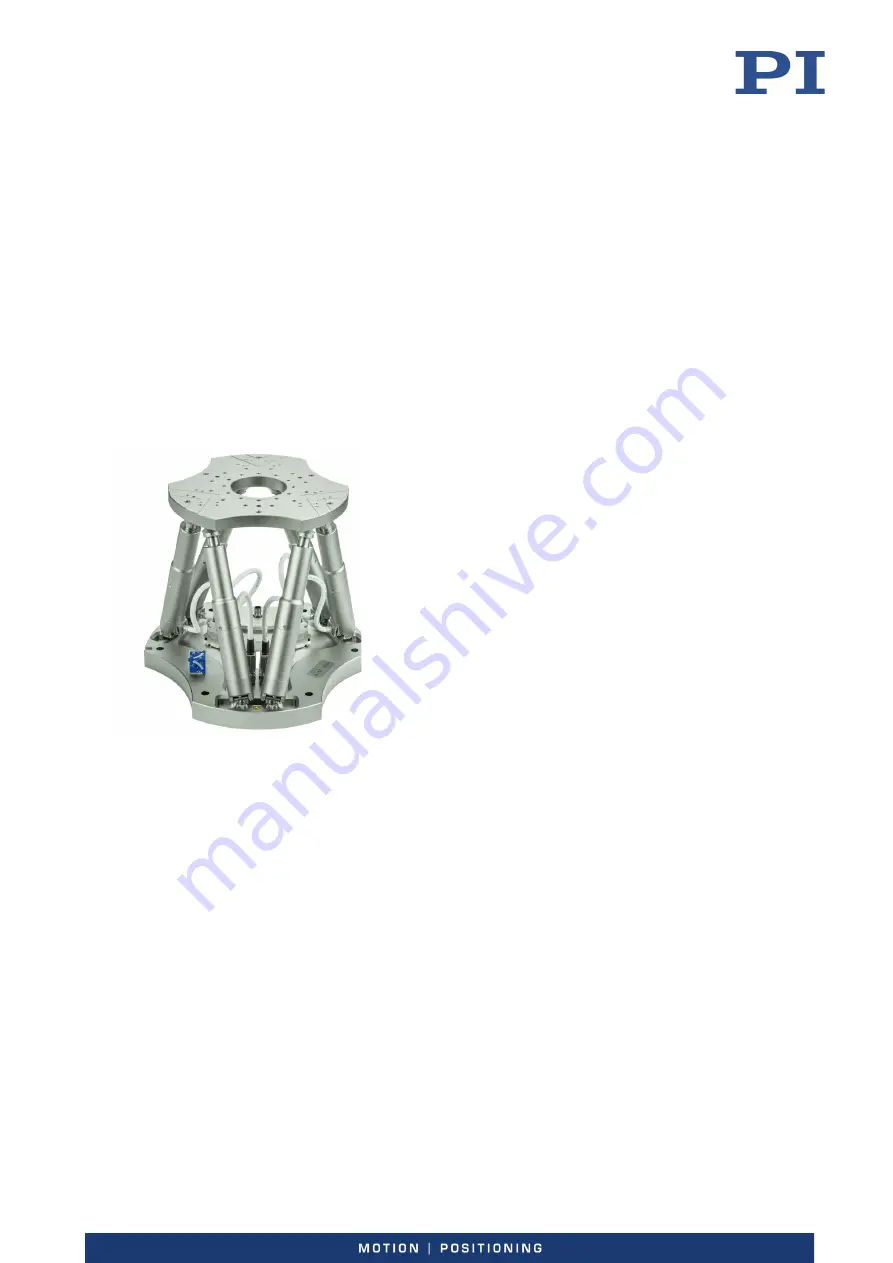
Physik Instrumente (PI) GmbH & Co. KG, Auf der Roemerstrasse 1, 76228 Karlsruhe, Germany
Phone +49 721 4846-0, Fax +49 721 4846-1019, Email [email protected], www.pi.ws
MS201E
H-840 Hexapod Microrobot
User manual
Version: 2.5.1
Date: 20.09.2022
This document describes the following hexapod
microrobots:
H-840.G2A
H-840.G2I
H-840.G2IHP
H-840.D2A
H-840.D2I