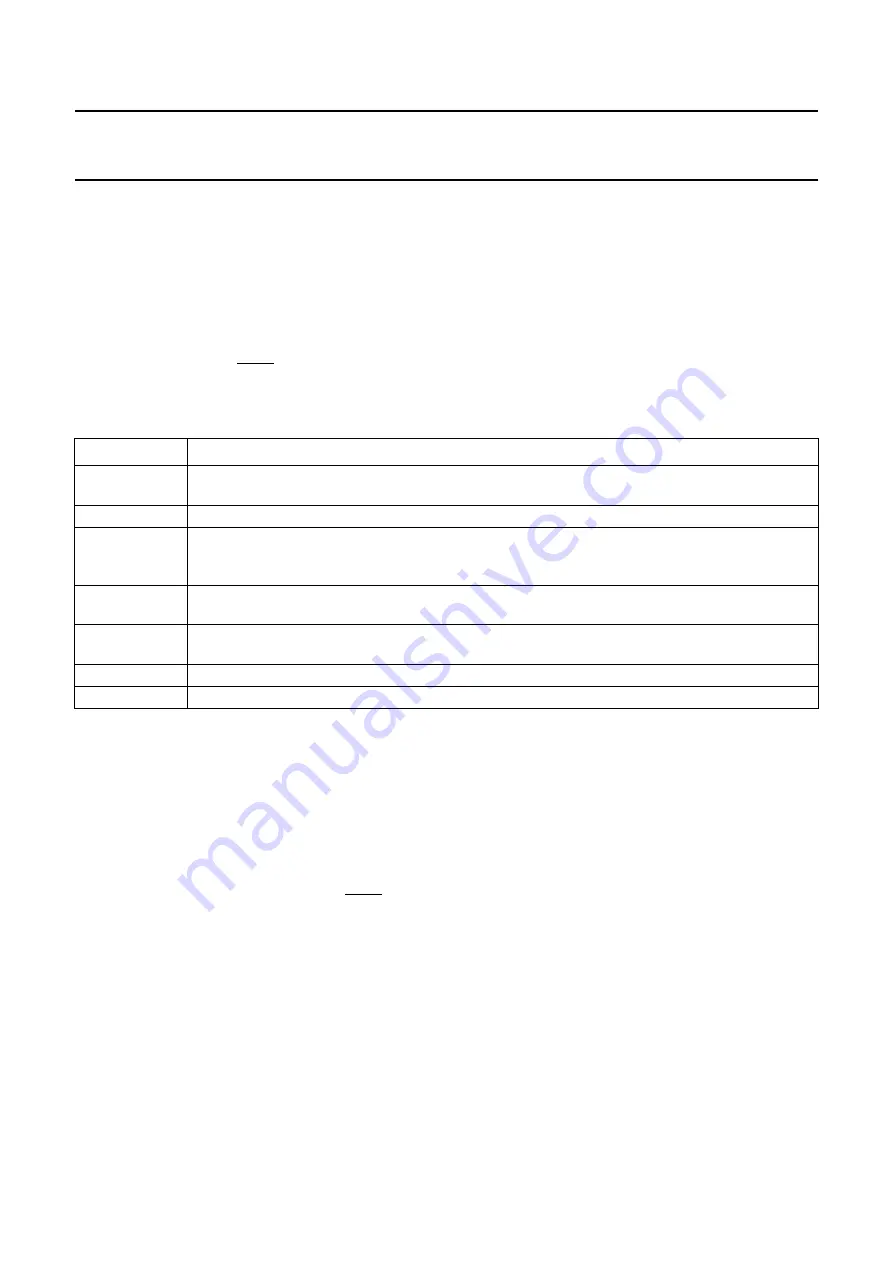
2004 Mar 01
61
Philips Semiconductors
Product specification
Digital video encoder
SAA7102; SAA7103
8
BOUNDARY SCAN TEST
The SAA7102; SAA7103 has built-in logic and 5 dedicated
pins to support boundary scan testing which allows board
testing without special hardware (nails). The SAA7102;
SAA7103 follows the
“IEEE Std. 1149.1 - Standard Test
Access Port and Boundary-Scan Architecture” set by the
Joint Test Action Group (JTAG) chaired by Philips.
The 5 special pins are Test Mode Select (TMS), Test
Clock (TCK), Test Reset (TRST), Test Data Input (TDI)
and Test Data Output (TDO).
The Boundary Scan Test (BST) functions BYPASS,
EXTEST, INTEST, SAMPLE, CLAMP and IDCODE are all
supported; see Table 112. Details about the
JTAG BST-TEST can be found in the specification “
IEEE
Std. 1149.1”. A file containing the detailed Boundary Scan
Description Language (BSDL) of the SAA7102; SAA7103
is available on request.
Table 112 BST instructions supported by the SAA7102; SAA7103
INSTRUCTION
DESCRIPTION
BYPASS
This mandatory instruction provides a minimum length serial path (1 bit) between TDI and TDO
when no test operation of the component is required.
EXTEST
This mandatory instruction allows testing of off-chip circuitry and board level interconnections.
SAMPLE
This mandatory instruction can be used to take a sample of the inputs during normal operation of
the component. It can also be used to preload data values into the latched outputs of the
boundary scan register.
CLAMP
This optional instruction is useful for testing when not all ICs have BST. This instruction addresses
the bypass register while the boundary scan register is in external test mode.
IDCODE
This optional instruction will provide information on the components manufacturer, part number and
version number.
INTEST
This optional instruction allows testing of the internal logic (no support for customer available).
USER1
This private instruction allows testing by the manufacturer (no support for customer available).
8.1
Initialization of boundary scan circuit
The Test Access Port (TAP) controller of an IC should be
in the reset state (TEST_LOGIC_RESET) when the IC is
in functional mode. This reset state also forces the
instruction register into a functional instruction such as
IDCODE or BYPASS.
To solve the power-up reset, the standard specifies that
the TAP controller will be forced asynchronously to the
TEST_LOGIC_RESET state by setting the TRST pin
LOW.
8.2
Device identification codes
A device identification register is specified in
“IEEE Std.
1149.1b-1994”. It is a 32-bit register which contains fields
for the specification of the IC manufacturer, the IC part
number and the IC version number. Its biggest advantage
is the possibility to check for the correct ICs mounted after
production and to determine the version number of the ICs
during field service.
When the IDCODE instruction is loaded into the BST
instruction register, the identification register will be
connected between TDI and TDO of the IC. The
identification register will load a component specific code
during the CAPTURE_DATA_REGISTER state of the TAP
controller, this code can subsequently be shifted out. At
board level this code can be used to verify component
manufacturer, type and version number. The device
identification register contains 32 bits, numbered 31 to 0,
where bit 31 is the most significant bit (nearest to TDI) and
bit 0 is the least significant bit (nearest to TDO);
see Fig.10.