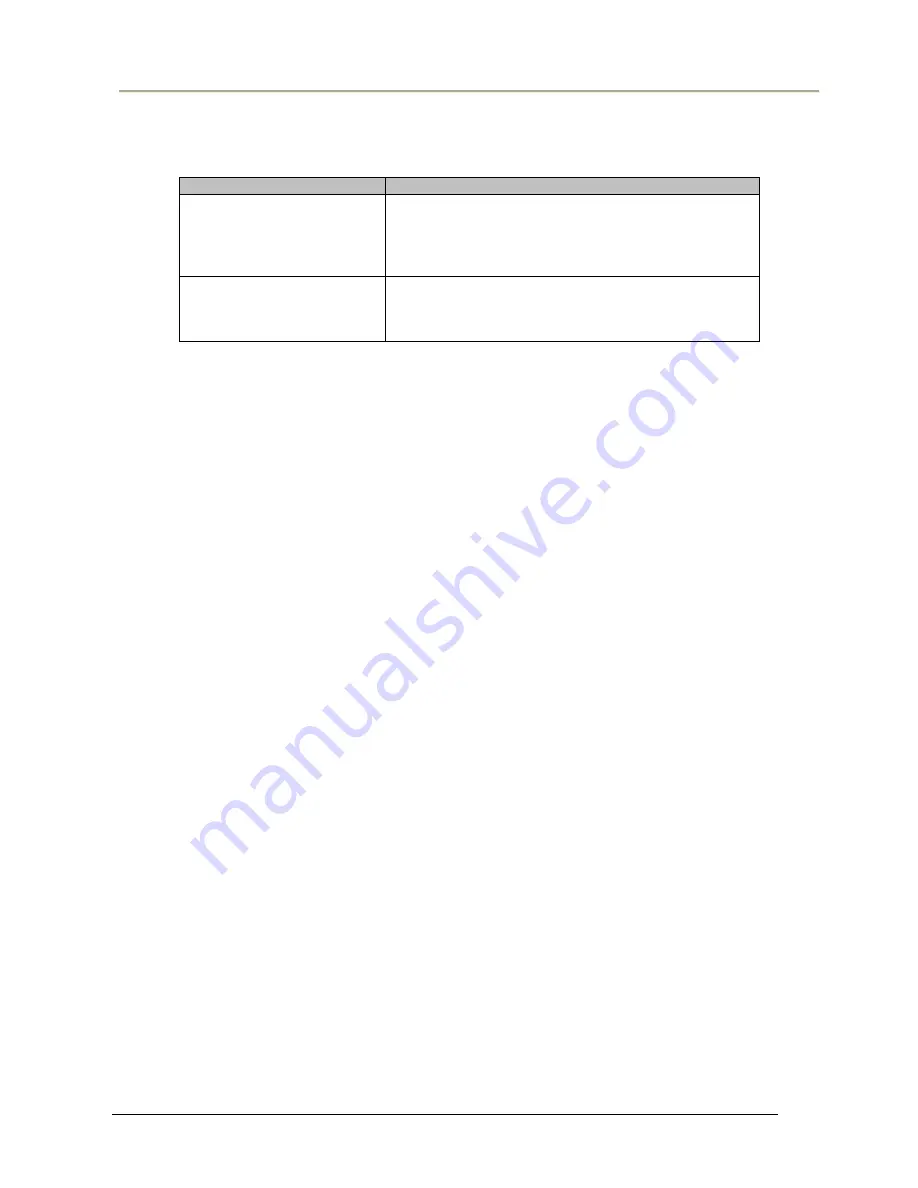
Refer to OQA Cosmetic Criteria for details.
The visibility of flow lines, sink marks, scratches, unevenness and flashes has to be judged at a distance of 30
cm, with normal overhead lighting (800–1000 lux):
Surface Area
Requirements
For highly visible surfaces
Very high appearance requirements:
9
None or very small flow lines (
≤
5mm) may occur
9
None or very small and faint injection-marks / sink-
marks may occur
9
No burrs, scratches or other defects may be visible
For surfaces which in normal
use are not or less visible
High appearance requirements:
9
Small flow lines (
≤
10mm) may occur
9
No burrs, injection marks, sink marks or other defects
may be visible
The exterior of the apparatus should be free of burrs.
Sharp edges and corners should have a minimum radius of 0.3mm whenever possible.
7.12.2 Decorative Coating Test
Samples need to be sufficiently aged before testing. They should be prepared according prescribed production
conditions and conditioned at standard atmospheric conditions for at least 3 weeks. However if the samples are
prepared within 3 weeks before testing, artificial aging in an oven at 40˚C during 3 x 24 hours is required. The
samples should be allowed to stabilize at the standard atmospheric conditions after the ageing period and
before executing the tests (in general a period of 2 hours will be sufficient).
7.12.2.1 Adhesion Test
Test methods are divided into:
a) Destructive test
This test is intended for the release of coating and printings. For this method, preparation is done using a
knife is used to cut gridlines over the area to be tested. The gridlines should be approximately 2mm
spaced.
b) Non-destructive test
This test is intended for incoming inspections of batches of products with coatings and printings.
Test Method (for both destructive and non-destructive)
Press the self-adhesive tape with a length of about 5 cm firmly onto the sample, and remove it
immediately with a jerk
at an angle which is as close as possible to 60° to the surface. Corners and sharp
edges have to be included in this test.
7.12.2.2 Resistance to Ethanol
Test method
The coating is rubbed in groups of 10 or 25 rubbing cycles (one cycle = one complete to and from
movement) with the hand tool with an average speed of 2 m/min. In the case that more than 25 cycles are
required, the felt has to be soaked after each 25th cycle with Ethanol by means of a diffuser and the test
should be continued immediately. After the last test cycle rests of the Ethanol has to be wiped off
immediately from the tested surface with a soft cloth. (See figure)
Requirement: Rcs3 = 2x25 cycles
2-10