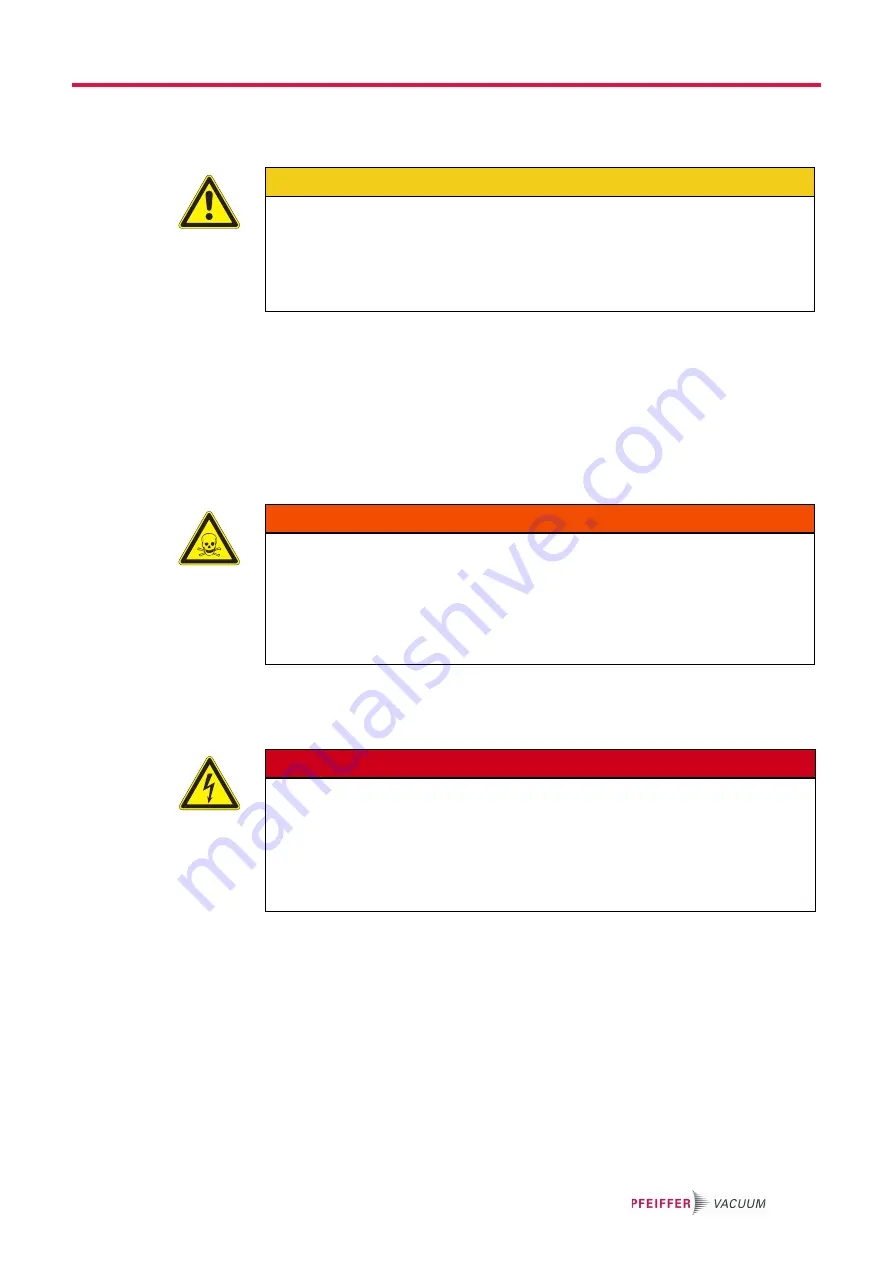
Operation
13
Connecting the ex-
haust side
Choose the cross-section of the exhaust line to be at least the size of the nominal con-
nection diameter of the vacuum pump's exhaust connection.
Piping to the pumping station must be suspended or supported.
– Physical forces from the piping system must not be allowed to act on pumping sta-
tion.
Lay piping from the pumping station sloping downward so that no condensate can flow
back into the pumps; otherwise fit a condensate separator.
– If an air trap is created in the system, then a device for draining condensation water
must be provided at the lowest point.
Connecting to the
mains power supply
Connect the pumping station electrically according to the information in the circuit dia-
gram.
6 Operation
6.1 Recommendations for the operator
• The service personnel must be advised in regular training courses on the necessity for
wearing the personal protective equipment. Working without protective equipment can
lead to serious and also lasting health damages.
CAUTION
High pressure in the exhaust line!
Danger of damage to the seals and danger of the pump bursting.
Install the line without shut-off valves on the exhaust side.
If there is danger of a build-up of excess pressure (> 1500 hPa abs.) in the lines, ob-
serve all official accident prevention safety regulations.
WARNING
Emission of toxic substances from the exhaust!
Danger of poisoning from emitted gases or vapours, which can be detrimental to health
and/or can pollute the environment, depending on the particular application.
Comply with the applicable regulations when working with toxic substances.
Only officially approved filter systems may be used to separate and remove these
substances.
DANGER
Voltage-bearing elements
Danger to life from electric shock.
The electrical connection can be carried out only by trained and authorised electri-
cians according to the information in the circuit diagram.
Disconnect the power supply and secure it against being switched back on.
Ensure the system is adequately earthed.
Summary of Contents for PP S30 596 A
Page 20: ...Technical data 20...