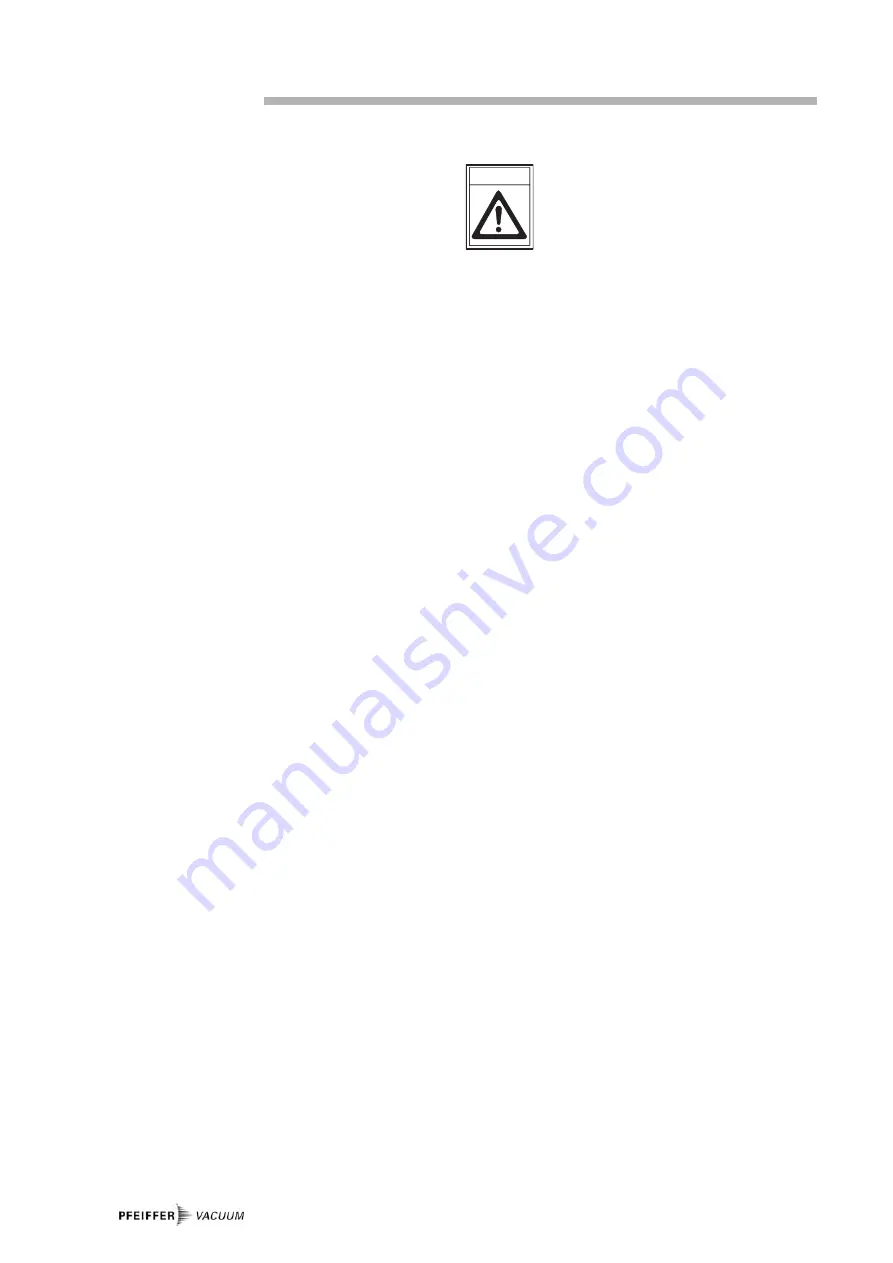
6
3. Installation
3.1. Setting Up The Pump And Location
Obey national safety regulations and safety requirements
concerning the use of vacuum and electrical equipment.
➡
Remove all packing material, remove the product from its
packing-box, remove the protective covers from the inlet
and outlet ports and keep, inspect the equipment.
➡
If the equipment is not used immediately, replace the
protective covers. Store the equipment in suitable conditi-
ons.
➡
Read and obey this manual before installing or operating
the equipment.
➡
If the equipment is brought from cold environment into a
room for operation, allow the equipment to warm up (pay
attention to water condensation on cold surfaces).
➡
Make sure ventilation is adequate if pump is installed in a
housing or if ambient temperature is elevated.
➡
Provide a firm level platform for the equipment and check
that the system to be evacuated is mechanically stable
and that all fittings are secure.
Attention: Flexible elements tend to shrink when
evacuated.
➡
Adopt suitable measures in case of differences, e. g. using
the equipment outdoors, installation in altitudes of more
than 2000 m above mean sea level, conductive pollution or
dewiness.
➡
Use fixing holes to screw-on the pump to a base plate.
➡
Ambient temperature range + 5 ... +40 °C.
➡
Where rack installation is involved, ensure adequate venti-
lation.
3.2. Connecting The Vacuum Side
➡
Remove locking cap on intake connection.
➡
Make connection between the vacuum system and pump
as short as possible.
– Ensure no mechanical forces act on the pump by a rigid
piping system; use elastic connections or bellows.
➡
Connect pump with intake connection to the apparatus.
➡
Obey maximum permitted pressures and pressure differen-
ces, see section ”Technical data”. Do not operate the
pump with overpressure at the inlet.
➡
If liquid - which would generate vapours - is present in the
system to be evacuated, a condensate trap must be fitted
upstream of the pump.
3.3. Connecting The Pressure Side
Pressure can rise to dangerous levels in exhaust
lines. Therefore, lay exhaust side lines without
shut-off units. Do not connect the exhaust side
with a closed system on account of the danger
of bursting.
In certain applications, exhaust gases and vapours can be
very hot and represent a health and/or environment hazard.
➡
Lay lines from the pump sloping downwards so that
condensate cannot run back into the pump, otherwise fit a
separator.
➡
Due to the high compression ratio of the pumps, pressure
at the outlet port might be generated being higher than the
max. permitted pressure compatible with the mechanical
stability of the system.
➡
Do not permit any uncontrolled pressurizing (e. g. make
sure that the exhaust pipeline cannot become blocked). If
you have an exhaust-isolation valve, make sure that you
cannot operate the equipment with the valve closed. Risk
of bursting!
➡
Ensure that the system design does not allow the exhaust
pipeline to become blocked.
➡
The diameter of the inlet and outlet pipeline should be at
the least as large as the diameter of the pump connection
pipelines.
CAUTION