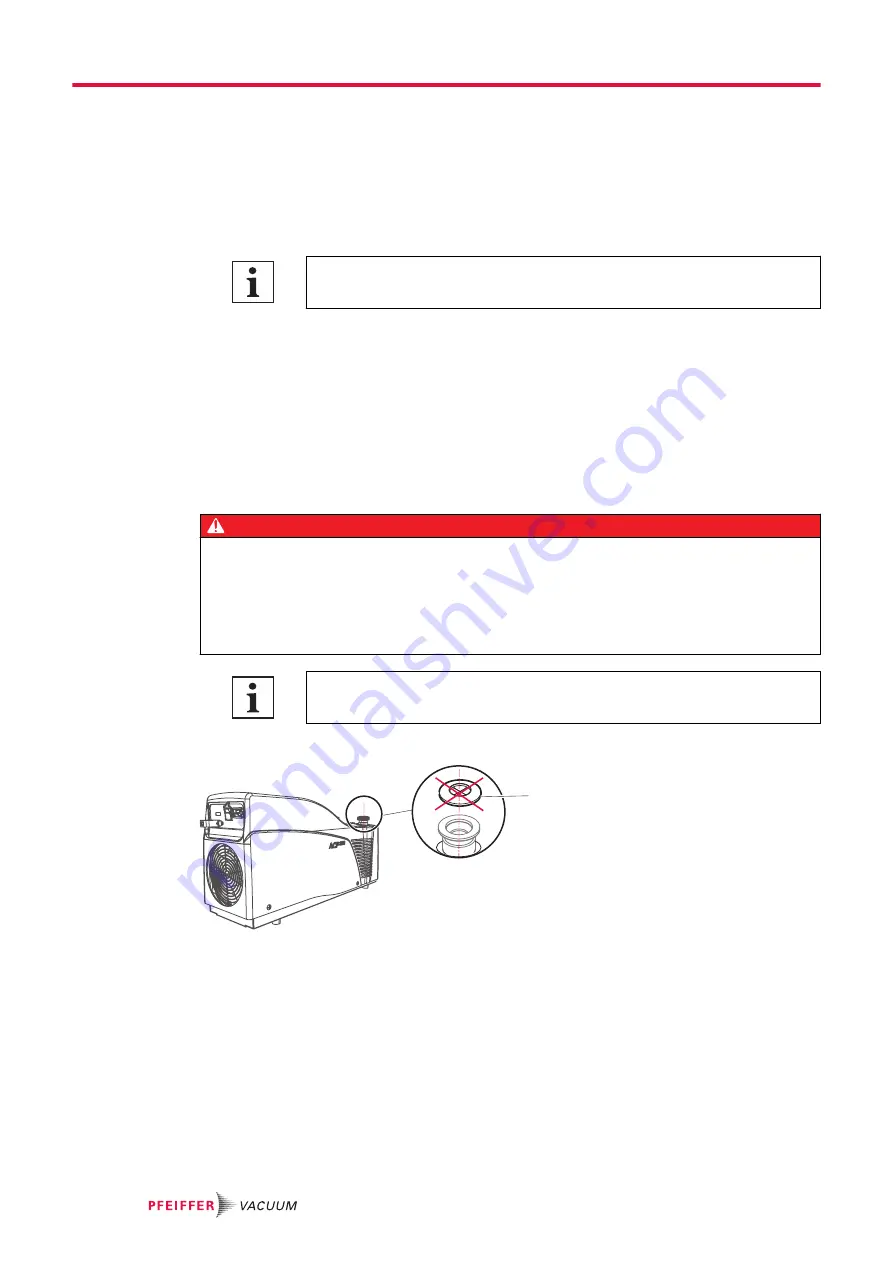
4. Remove the blanking plates used to seal the inlet and exhaust ports.
5. Keep the blanking plates, screws and washers for reuse when transporting the pump.
6. Ensure that no screws, washers or other objects are dropped into the pump inlet.
7. Fit flexible tubes in the pumping line to reduce the transmission of vibration.
8. Perform a leak test on the entire pumping line after installation.
5.2.1 Connection on the pump inlet side
Make sure that the parts or chambers connected to the inlet of our products can
withstand a negative pressure of 1·10
-3
hPa relative to atmospheric pressure.
To achieve the optimum pumping speed, make the pumping line
as short and straight as possible
and ensure that its inside diameter is not narrower than the pump inlet flange inside diameter
.
The product is not designed to withstand loads on its inlet flange which may compromise stability.
● Mechanically attach the vacuum chamber separately from the pump.
● Use only dry parts and clean, grease-free, dust-free pipelines.
● It may be necessary to install an inlet filter (particle filter or condensable filter).
● If necessary, install an isolation valve on the inlet which closes when the pump stops.
5.2.2 Connection on the pump exhaust side
DANGER
Risk of poisoning in case of contact with toxic substances and by-products generated by the
process
The vacuum pump, pumping line components and operating fluids
may potentially be contaminat-
ed
with toxic, corrosive, reactive and/or radioactive substances related to the process and harmful to
health.
► Always connect the pump exhaust to an exhaust extraction system.
Ensure that all components in the exhaust line have a maximum pressure rating
that exceeds the highest pressure the pump can generate.
Pump exhaust is equipped with an anti-noise device.
1
1
Anti-noise device
In case of connection to an exhaust pipe:
► Remove the anti-noise device on the exhaust port.
CV version
Installation
20/56
Summary of Contents for ACP 28 CP
Page 54: ......