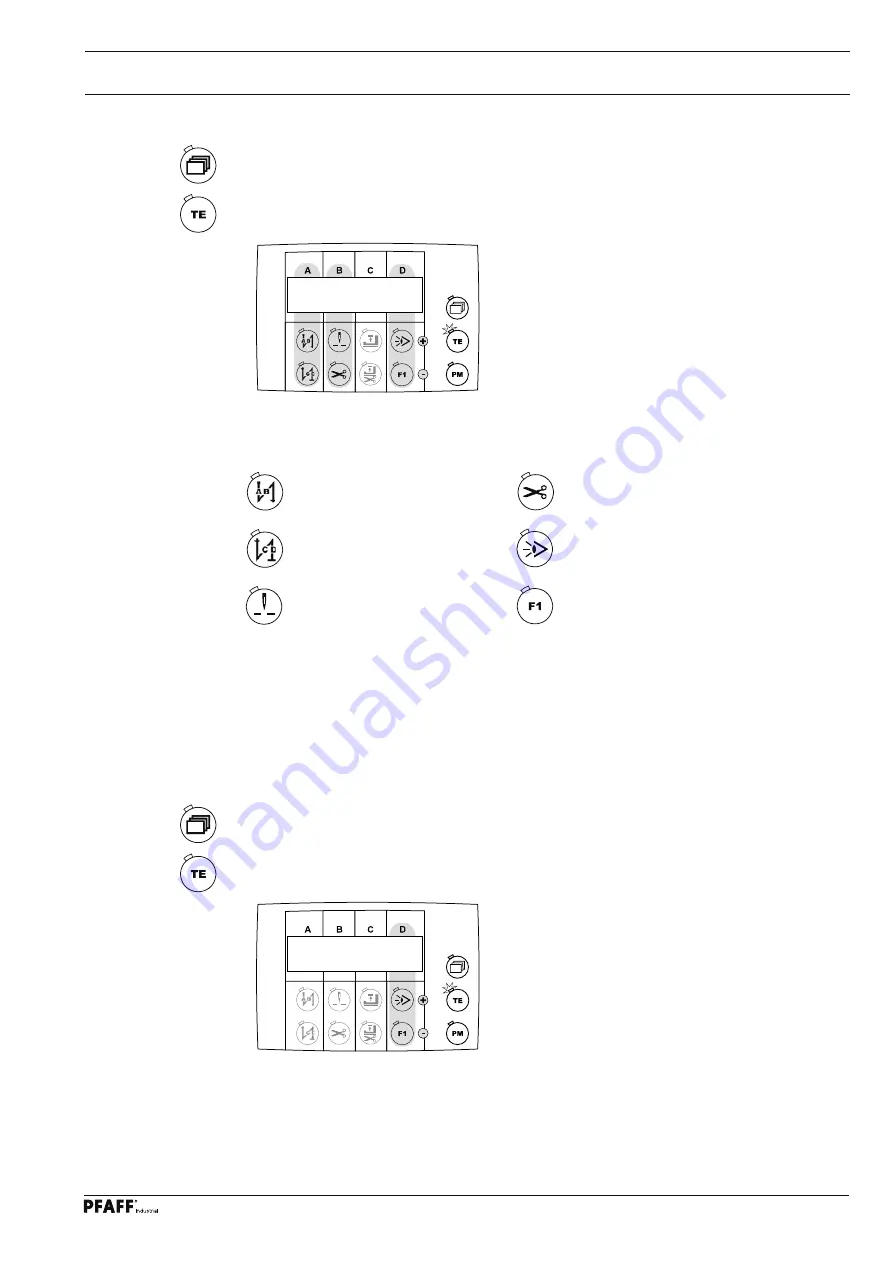
Sewing
37
9
.01.03
Selecting parameter entry
●
Call up the parameter display (press the button several times if necessary).
●
Switch on "TE / Input" (
LED lights up
).
104
1
The display will show the fi rst parameter with the corresponding setting value.
Parameters can be selected and values changed as follows:
Select the parameter
hundred digit (
A+
)
Select the parameter ten and
single digit (
B-
)
Select the parameter
hundred digit (
A-
)
Decrease the
parameter value (
D+
)
Select the parameter ten and
single digit (
B+
)
Decrease the
parameter value (
D-
)
●
Selecting parameters and changing values, see
chapter 9.03 Parameter Entry
.
9
.01.04
Selecting the maximum speed
●
Call up the speed display (press the button several times if necessary).
●
Switch on "TE / Input" (
LED lights up
).
3500
If the machine is in standstill the maximum speed will be displayed and can be
changed in hundred increments with the function key.
Summary of Contents for POWERLINE 2571 ME PLUS
Page 55: ...Note ...