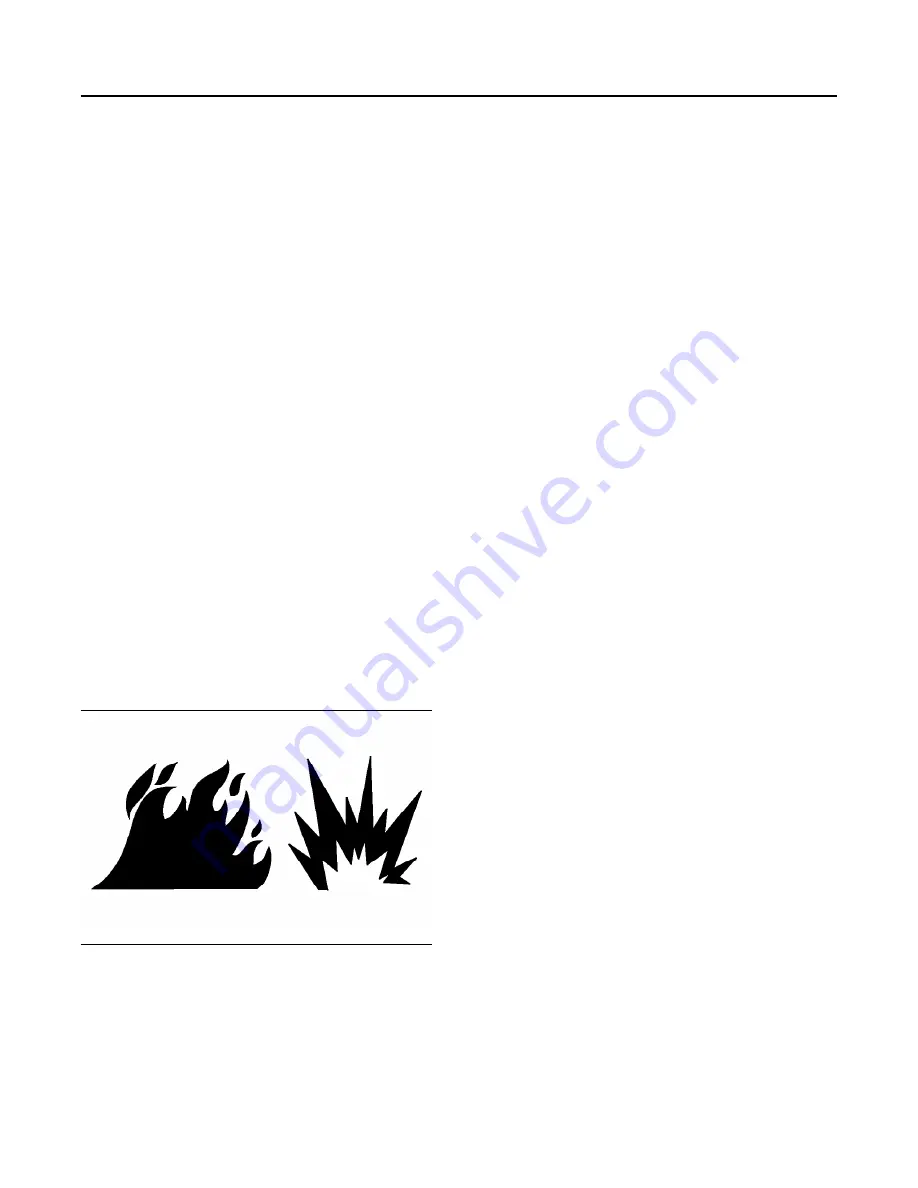
If there is contamination of the skin or eyes, wash the
affected area with a continuous supply of clean water
or with calcium hydroxide solution. Wash the area
effected for 15 to 60 minutes and obtain immediate
medical attention.
Diesel Fuel
Diesel may be irritating to the eyes, respiratory
system, and skin. Prolonged exposure to diesel may
cause various skin conditions. Appropriate personal
protective equipment should be used. Refer to
supplier Material safety Data sheets for detailed
information.
Batteries
The liquid in a battery is an electrolyte. Electrolyte is
an acid that can cause personal injury. Do not allow
electrolyte to contact the skin or the eyes.
Do not smoke whilst checking the battery electrolyte
levels. Batteries give off flammable fumes which can
explode.
Always wear protective glasses when you work with
batteries. Wash hands after touching batteries. The
use of gloves is recommended.
i06545894
Fire
Prevention
and
Explosion
Prevention
Illustration 17
g00704000
All fuels, most lubricants, and some coolant mixtures
are flammable.
Flammable fluids that are leaking or spilled onto hot
surfaces or onto electrical components can cause a
fire. Fire may cause personal injury and property
damage.
After the emergency stop button is operated, ensure
that you allow 15 minutes, before the engine covers
are removed.
Determine whether the engine will be operated in an
environment that allows combustible gases to be
drawn into the air inlet system. These gases could
cause the engine to overspeed. Personal injury,
property damage, or engine damage could result.
If the application involves the presence of
combustible gases, consult your Perkins dealer and/
or your Perkins distributor for additional information
about suitable protection devices.
Remove all flammable combustible materials or
conductive materials such as fuel, oil, and debris
from the engine. Do not allow any flammable
combustible materials or conductive materials to
accumulate on the engine.
Store fuels and lubricants in correctly marked
containers away from unauthorized persons. Store
oily rags and any flammable materials in protective
containers. Do not smoke in areas that are used for
storing flammable materials.
Do not expose the engine to any flame.
Exhaust shields (if equipped) protect hot exhaust
components from oil or fuel spray if there was a line,
a tube, or a seal failure. Exhaust shields must be
installed correctly.
Do not carry out any work on the fuel lines or tanks
that could ignite residual fuel. Grinding, welding,
cutting, chiseling, and sawing have the potential to
create a source of ignition must be avoided.
Do not weld on lines or tanks that contain flammable
fluids. Do not flame cut lines or tanks that contain
flammable fluid. Clean any such lines or tanks
thoroughly with a nonflammable solvent prior to
welding or flame cutting.
Wiring must be kept in good condition. Ensure that all
electrical wires are correctly installed and securely
attached. Check all electrical wires daily. Repair any
wires that are loose or frayed before you operate the
engine. Clean all electrical connections and tighten
all electrical connections.
Eliminate all wiring that is unattached or
unnecessary. Do not use any wires or cables that are
smaller than the recommended gauge. Do not
bypass any fuses and/or circuit breakers.
Arcing or sparking could cause a fire. Secure
connections, recommended wiring, and correctly
maintained battery cables will help to prevent arcing
or sparking.
Ensure that the engine is stopped. Inspect all lines
and hoses for wear damage, leakage or for
deterioration. Ensure that the hoses are correctly
routed. The lines and hoses must have adequate
support and secure clamps.
M0122761
15