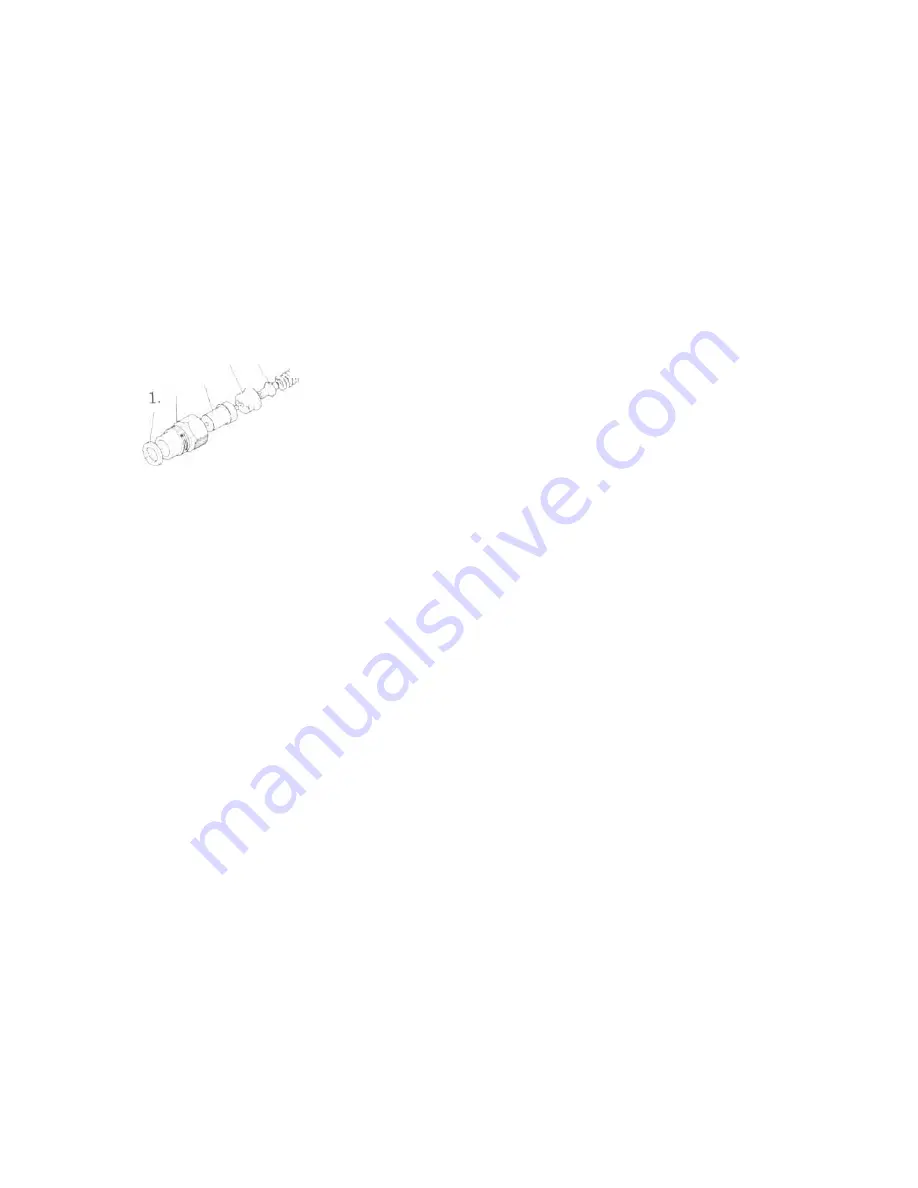
Reassembly/Adjustment
A. Before fitting a new nozzle assembly, soak it in
heated light oil (50°-60°C) to remove anti-corro-
sive agent from the nozzle. Then, slide the body
on the needle valve so that they slide smoothly.
B. Turn the nozzle body upside down, fit the shim,
spring, rod, piece and nozzle in this order, and
tighten with a nozzle nut.
2. 3.
8. 9' -
7.
5. 6.
4.
1. Gasket
2
.
Nozzle nut
Tightening
torque 8 - 10
kgf.m
Air Cleaner
- Construction/Function
The cyclonic air cleaner houses a paper element
which removes dirt or dust from air drawn in.
-
Inspection/Replacement
A. At every 100-200 hours of operation, take out the
element and clean it by blowing compressed air (
pressure lower than 100psi.)
B. When oil or soot is stuck to the element, soak it
in synthetic detergent for approximately 15
minutes. Then, rinse it in the detergent
several times, and wash it in clean water.
Finally, leave to dry.
C. When operating the machine in dusty environ-
ment, increase service frequency.
D. At every sixth cleaning or every year, replace the
element.
3. Nozzle
1118
4. Spacer
5. Rod
6. Spring
F
7. Shims
8. Body
9. Nut
E. After cleanina the element, put a light inside
the
element, and check it for cracks, holes or wear.
If damage is found or the gasket is broken,
replace the element.
Do not install the element until completely dry.
C. After reassembly, inspect the injection
pressure of the nozzle.
Adjust the pressure with adjusting shims using a
nozzle tester so that the injection starts at 120kg/
cm
2
1,707psi 116ats. (The pressure increases or
decreases about 10kg/cm
2
142psi 9.7ats with a
shim of 0.1 mm thick.)
D. Spray condition
a. Fuel drops should not be mixed in the spray
pattern.
b. Fuel should be sprayed in conical shape with
respect to the nozzle axis.
c. Check that the fuel is sprayed in a circular
shape when tested.
d. Hold the pressure at 100kg/cm
2
, 97ats, lower
by 20kg/cm
2
, 20ats, than specified (120kg/ cm
2
) and check that no test oil drops from the
nozzle tip.
Summary of Contents for 103-06
Page 1: ...Perkins 100 Series 103 06 103 09 103 10 Perama M25 M30...
Page 2: ......
Page 7: ...ENGINE DIAGRAMS...
Page 8: ...Engine cross sectional views...
Page 38: ......
Page 56: ...WIRING DIAGRAMS Perama 103 06 103 09 103 10 15 amp alternator 103 09 103 10 35 amp alternator...
Page 59: ......
Page 73: ......
Page 77: ......