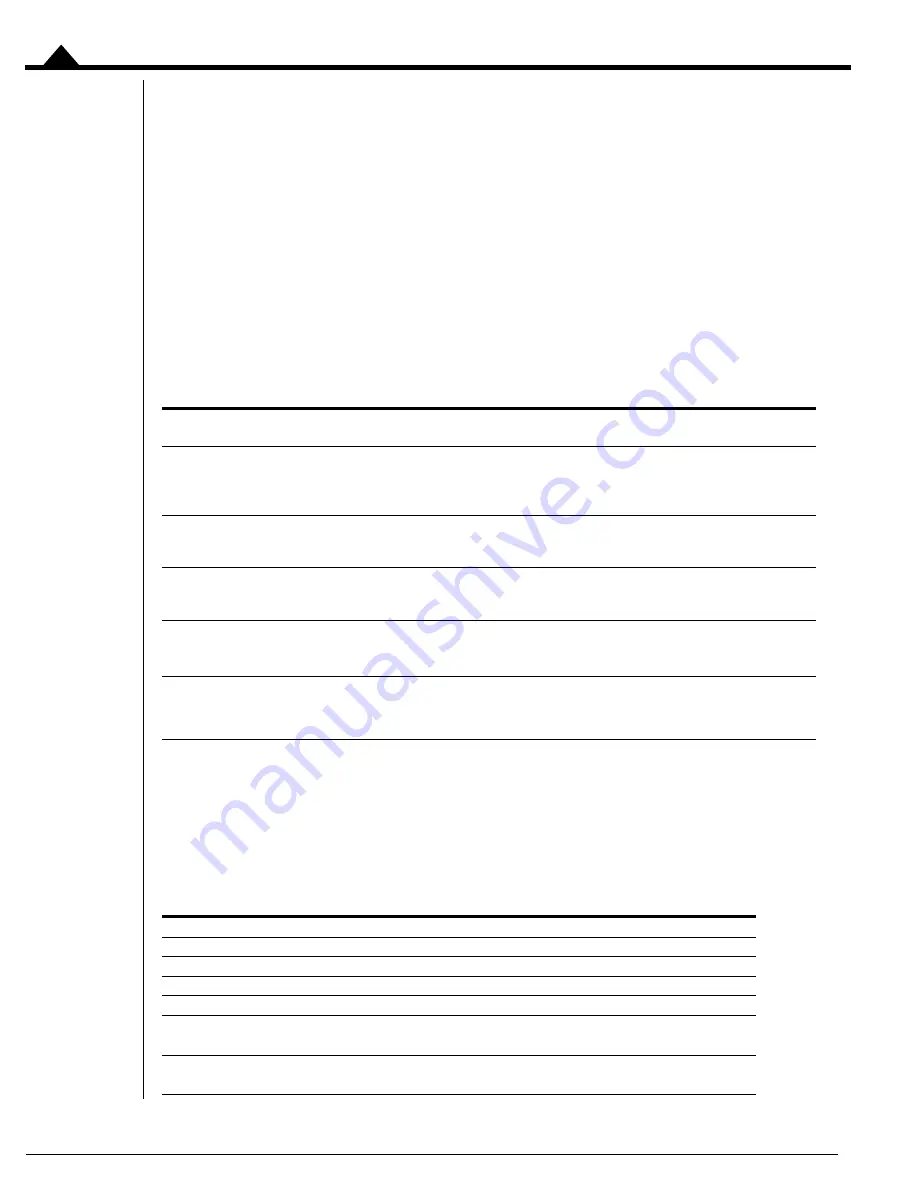
50
ION/CME N-Series Digital Drive Developer Kit User Manual
3
3.4
Conversion Factors, Defaults and
Limits
To correctly control various N-Series ION features it may be helpful to know certain drive-specific scale factors. The
following tables summarize these values.
3.4.1
Conversion Factors, Low Power Units
The following table provides electrical conversion factors for low power level N-Series ION units (P/Ns:
DD4X1X0056/02).
These factors convert various integer Magellan IC command arguments (referred to as having units of counts) to
physical quantities such as amperage, volts, etc... For more information on the Magellan Motion Control IC refer to
the
Magellan Motion Control IC User Guide
. For more information on C-Motion commands refer to the
C-Motion/PRP
II Programming Reference
.
* Some C-Motion commands specifying a current may have a scaling of two times this value. Refer to the Magellan Motion Control IC
User Guide for more information.
3.4.2
Defaults & Limits, Low Power Units
The following table provides default values, low limits and high limits for various specifiable drive-related parameters
for low power level N-Series ION units (P/Ns: DD4X1X0056/02).
Unit
Example C-Motion
Commands
Scaling
Example usage
Amps
GetCurrentLoopValue
.231 mA/count*
A command request to read the
ActualCurrent parameter returns a value
12,345. This corresponds to a current of
12,345 counts * 0.231 mA/count = 2.851A
Volts
SetDriveFaultParameter
GetBusVoltage
10.0 mV/count
To set an overvoltage threshold of 50V, the
command value should be 50 V *1,000 mV/
V / 10.0 mV/count = 5,000
Temperature
SetDriveFaultParameter
GetTemperature
.00391 °C/count
To set an overtemperature threshold of
65 °C, the command value should be 65 °C
/ .0039 °C/count = 16,624
I
2
t continuous
current
SetCurrent
.231 mA/count
To set an I
2
t continuous current of 1.0A, the
command value should be 1.0A * 1,000 mA/
A / 0.231 mA/count = 4,329
I
2
t energy
SetCurrent
.00588 A
2
Sec/count
To set an I
2
t energy of 5.0 A
2
Sec, the
command value should be 5.0 A
2
Sec /
0.00588 A
2
Sec/count = 850
Setting
Default Setting
Low Limit
High Limit
Overtemperature limit
75.0 °C
0 °C
75.0 °C
Overtemperature hysteresis
5.0 °C
0 °C
25.0 °C
Overvoltage limit
60.0 V
10.0 V
60.0 V
Undervoltage limit
10.0 V
10.0 V
56.0 V
I
2
t continuous current limit,
Brushless DC motor
1.5 A
0.0 A
1.5 A
I
2
t continuous current limit, DC
Brush motor
1.5 A
0.0 A
1.5 A
Summary of Contents for CME N Series
Page 6: ...vi ION CME N Series Digital Drive Developer Kit User Manual ...
Page 8: ...viii ION CME N Series Digital Drive Developer Kit User Manual ...
Page 30: ...30 ION CME N Series Digital Drive Developer Kit User Manual 1 ...
Page 58: ...58 ION CME N Series Digital Drive Developer Kit User Manual 3 7 6 7 6 PP LQFK ...
Page 69: ...ION CME N Series Digital Drive Developer Kit User Manual 69 4 ...
Page 70: ...70 ION CME N Series Digital Drive Developer Kit User Manual 4 ...