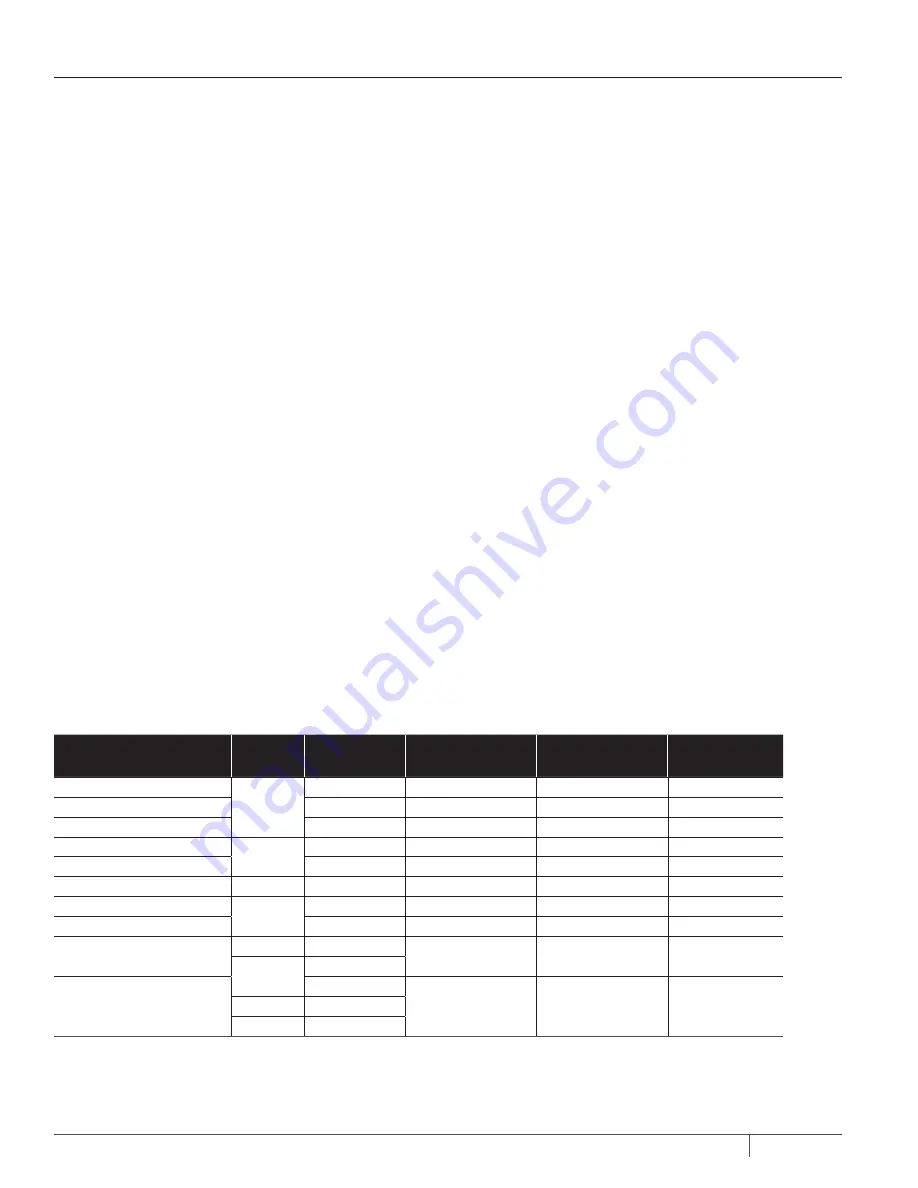
6
L-3113 (10-15-22)
ISOBUS COMMUNICATIONS
ISOBUS COMMUNICATIONS
The ProStop-E Quad supports 250 kbps ISOBUS compatible
communication using a CAN bus interface
ProStop-E Quad modules are all connected together, but
are organized in logical groups of 16.
Each CAN bus line can physically support up to 80
ProStop-E Quad nozzle bodies while maintaining individual
nozzle control. Each line can support up to 30 Amps.
Strategic power management is needed when
simultaneously actuating multiple valves within one
module, to prevent excessive power and voltage drop along
each line.
ADDRESS MANAGEMENT
Each ProStop-E Quad will have a unique CAN address and unique
ISOBUS name. The modules are arbitrary address capable and
have a default starting address of 150 (96h). On power-up the
module sends an address claimed message (PGN 00EE00h)
with its starting address. If there is only one module on the bus,
this is the end of the process. If there are multiple modules,
the ISOBUS names are compared and the higher priority name
(lower number retains the address and then the lower priority
module will increment its addresses by one, 151 and then re-send
out the claim. A spray controller can also send a request (PGN
00EA00h) for address claimed (00EE00h), which requests that
the connected ProStop-E Quads reply with their addresses and
their ISOBUS name.
MAPPING MODE
Devices in the mapping mode will wait for input on the address
line and listen for address claim messages from other devices.
Devices in mapping mode will not send responses to compete in
the address claim process until there is a signal on their address
line. See PCM 1 below for putting the devices into mapping
mode. The command must be sent to the global address (255)
so that all devices on the bus are placed in the mapping mode
simultaneously.
Upon seeing a signal on the address line input, the device
will initiate an address claim process starting at the address
immediately following the last address claim message received
since being placed in the mapping mode. If no address claim
has been received, the device will start at the specified
address. Once an address is claimed, the device will store this
address in non-volatile memory for use as the starting point
of future address claim processes instead of the default 150,
and the device will exit the mapping mode and pulse a signal
on its address line output 10ms after exiting. This mode can be
initiated every time the system starts up so that the user does
not need to do anything to map the devices.
For example, the user wants to set the address of each
device starting at 150 for the device closest to the ECU and
incrementing by 1 for each next device on the bus. The ECU
sends PCM 1 to the global address (255) with command 2
and 150 to put all devices into mapping mode and provides a
constant signal to the address line input of the first device.
The address line signal propagates along the bus, and after all
devices have received it, each device will have a unique address
corresponding to physical location rather than serial number
that persists across power cycles.
FIELD
BYTE #
BIT #
DECIMAL VALUE
TOTAL BITS
BINARY VALUE
Self config. address
0
7
1
1
1b
Industry group
6-4
2
3
010b
Device class instance
3-0
0
4
0000b
Device Class
1
7-1
6
7
000 0110b
Reserved
0
0
1
0b
Function
2
7-0
129
8
1000 0001b
Function Instance
3
7-3
2*
5
0001 0b*
ECU Instance
2-1
4
3
100b
Manufacturer Code
4
7-0
721
11
0101 1010 001b
5
7-5
Identity Number
4-0
Device Specific
21
Unit Serial
Number
6
7-0
7
7-0
ISOBUS NAME CONSTRUCTION
* Function Instance is 3 (0001 1
b
) in tootloader