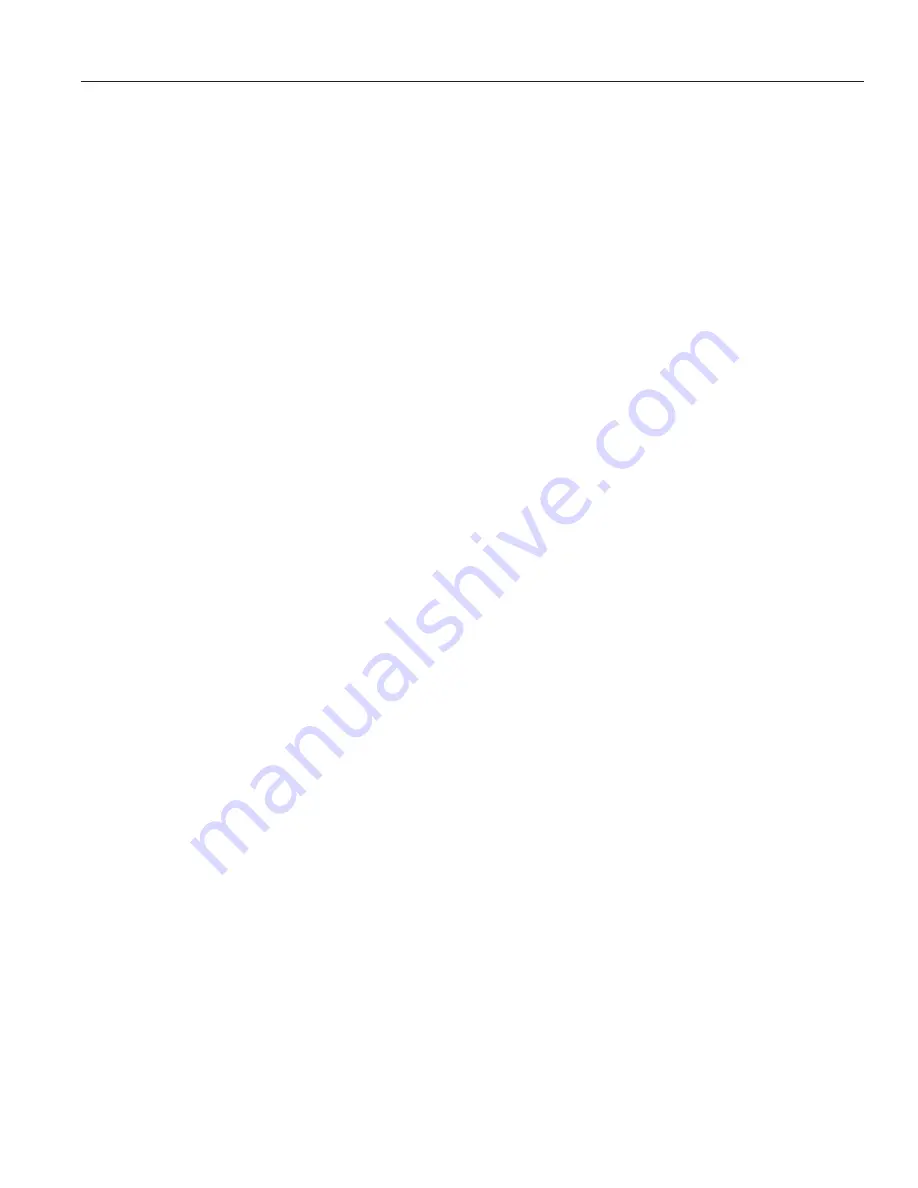
Fairbanks Nijhuis™
11/12/12
Intelliboost™ Water Booster System
Basic Operation Manual
15
NOTICE: The suction pipe requires a check valve or isolation valve.
1. Close to discharge isolation valve.
NOTICE: Please see “Starting” before proceeding any further.
CHECKING DIRECTION OF ROTATION
NOTICE: Do not disconnect the motor from the shaft to check the direction of rotation. If you remove the coupling,
then you must adjust the shaft position when you reinstall it. This must be done before starting the pump.
Danfoss Drive Preventive Maintenance Instruction
PM Checklist
r
Vacuum dust and dirt from heat sink fins
r
Clean or replace as conditions require intake air filters (125 Hp constant torque models, 150 Hp variable torque
models and larger have filters located behind the intake louver panels)
r
Check ventilation fans for proper operation and clean as needed.
r
Confirm VFD’s ventilation clearances have not been obstructed
r
Check electrical connections and re-torque as needed. If possible, perform an IR thermal scan of the VFD’s
power input and power output.
r
Check line voltage
r
Check motor & output phase balance
r
Inspect DC buss capacitors (older drives)
r
Record the VFD’s parameter settings using MCT-10
r
Confirm the VFD doors and covers are in place and properly closed
2. Clean the drive’s interior.
a. Dirt coating drive circuit boards and other components can interfere with proper cooling and even provide a path
for electricity to short out along unintended paths. This can cause erratic operation and possibly damage to drive
components.
b. Corroded electrical connections can cause excess heat build-up, short circuits, erratic drive operation, and even
component damage.
c. This should be done after the installation of the drives is complete and before power is applied to the drive. The
main point here is to ensure that no metal filings or other installation-related dirt are inside the drive or its option
enclosure.
d. If the drive is installed in an area where a lot of construction work will be performed, it is best to keep the drive
covered while it is not in operation. Of course, if it is being used, the drive must be uncovered so that cooling air
can be freely supplied to it. After the construction is complete it will be important to clean the interior of the drive.
Low pressure, clean, dry air or similar commercial products can be used to clean dirt off of circuit boards. While
a vacuum cleaner can be used to collect falling dirt, it is important to ensure that circuit boards are not damaged
by the use of a powerful vacuum cleaner on the boards. Inspect drive connectors for dirt or corrosion.
e. In a normal environment, the drive’s interior should be inspected annually and cleaned, if necessary. In dirty
environments, more frequent inspection is required. The level of dirt found inside the drive can be used to dictate
the frequency of inspections and cleanings that is required.
3. Clean air filters (if any).
a. Many VLT drives have no air filters. However, some sizes and enclosure styles do use air filters in conjunction
with their fan cooling systems. For these drives it is important to periodically inspect and clean or replace the
filter element.
b. Because the loading of the air filters can vary dramatically from one installation to another, it is important to
initially check the air filters frequently to establish the required inspection interval