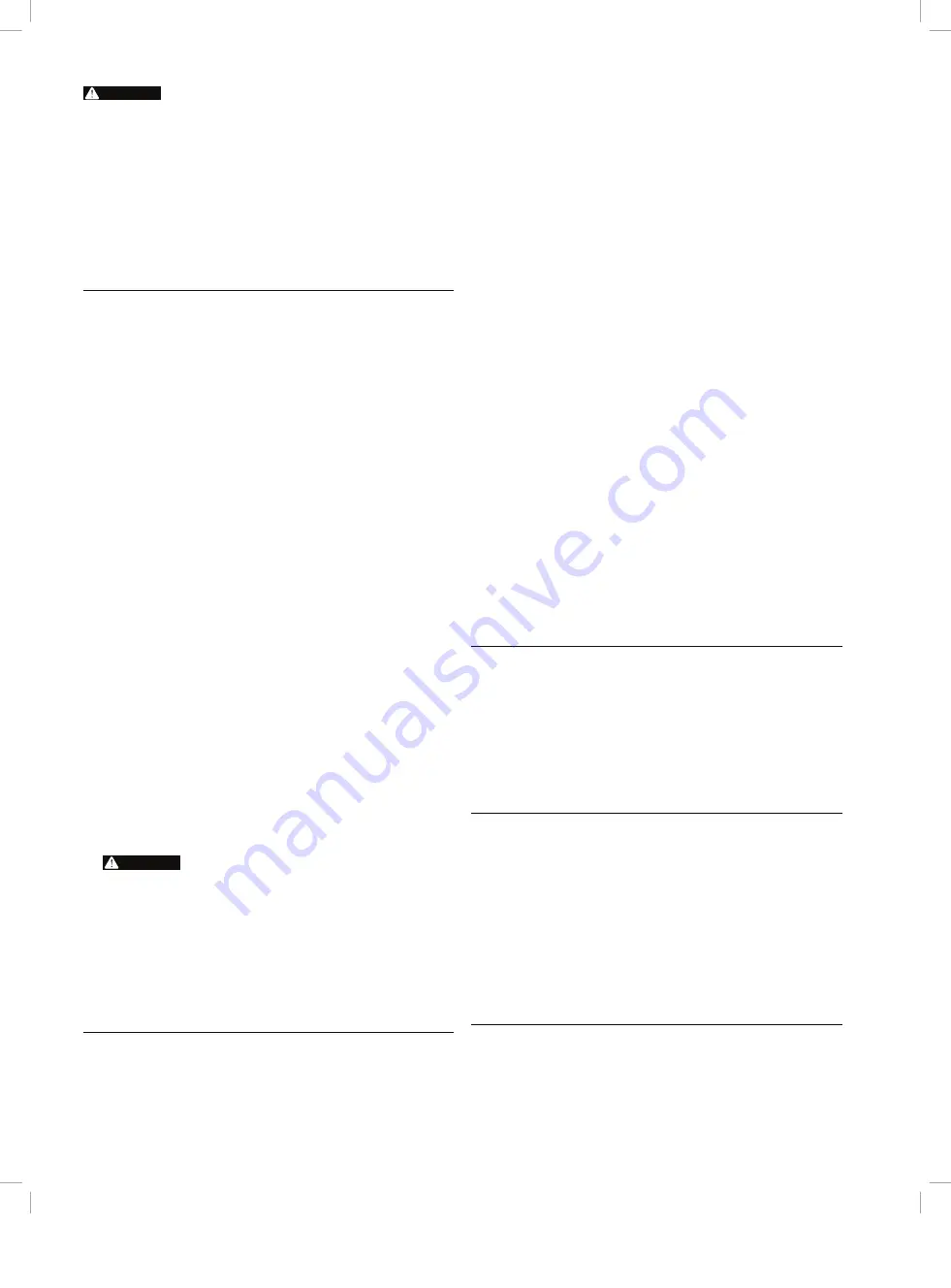
4
WARNING
Refer to
Reject to Drain, Maximum
under
RO
Production
in the Performance Table (page 5) to determine the
maximum gallon per minute waste flow rate. Verify drain has ample
capacity for this waste flow, plus all other souces of waste flow
sharing this drain.
electrical connections
The system is pre-wired at the factory. Verify that your supply
voltage matches the primary voltage on the transformer dataplate.
Available voltages are 115, 230 & 240 VAC. A ground fault protected
circuit rated at 15 Amps minimum is required. Plug-in power cord
when instructed to do so in the following section.
cartrIdge InStallatIon and actIVatIon
Remove the outer shrink-wrap and protective closure from the
1.
pre-filter (optional), TO, RO (MR) and CC cartridge (optional) or
BW 4400 cartridge (optional).
If the optional Pre-filter has been supplied, go to step to 3. If not
2.
supplied, go to step 4.
Locate the sump (clear bowl) for the pre-filter housing. Install
3.
the pre-filter cartridge into the sump. Locate the O-ring in the
small parts pack. Lightly lubricate this O-ring with a food grade
lubricant and install it into the groove in the sump. Install the
sump with pre-filter and O-ring into the pre-filter head. Use the
sump wrench to tighten the sump securely.
Install the TO cartridge into the TO head (left-hand), following
4.
the instructions on the cartridge.
Slowly open the inlet supply valve. Position a bucket underneath
5.
the RO cartridge head (center) to collect the water. Apply power
to the system by plugging the power cord into the receptacle.
Within moments, water should begin to spill out of the RO head
and into the bucket. Carbon fines and air will be flushed out
of during this time. Flush until water runs clear (2-3 minutes
typically). If the bucket requires emptying, un-plug the power
cord from the receptacle to stop the flow, then empty the bucket.
Reposition the bucket and repeat the flushing operation as
required. Once the TO cartridge has been flushed, un-plug the
power cord from the receptacle.
Install the RO cartridge into the RO head, following the
6.
instructions on the cartridge.
If the optional 7CC-BW or BW 4400 cartridge has been supplied,
7.
go to step to 8. If not supplied, go to step 9.
Remove the plug from the 7CC-BW/BW 4400 cartridge head
8.
(right-hand). Install the 7CC-BW or BW 4400 cartridge into the
head, following the instructions on the cartridge. If the optional
7CC-BW has been supplied, go to step to 9. If the optional BW
4400 cartridge has been supplied, open blend valve fully (See
figure 5). Go to step to 9.
Disconnect the tubing connecting the storage tank to the system
9.
at the storage tank and route to a drain temporarily.
WARNING
do not use this product water! It may contain a
preservative solution from the ro cartridge and should not be
consumed!
Apply power to the system by plugging the power cord into the
10.
receptacle. Within moments, water should begin to exit the
storage tank tubing. If the optional BW 4400 cartridge has been
supplied, close blend valve after 3 minutes. Allow the system to
flush for at least 1 hour or until 5 gallons of product water has
been produced. Un-plug the power cord. Re-connect the tubing
to the storage tank.
dISInfectIon
When flushing is complete, the storage tank and associated piping
must be disinfected, and then completely flushed. The steps for this
are outlined below.
Locate the 3/8" OD tubing that connects to the storage tank.
1.
Disconnect the end which connects to the fitting at the
processor. Measure 1 ounce of 5.25% bleach for every 7.5 gallons
of storage tank capacity. Pour this volume of bleach into the tube
that leads to the storage tank. Re-connect this tube to the fitting.
Apply power to the system by plugging the power cord into the
receptacle. The booster pump should begin to run and fill the
storage tank.
Once sufficient water has entered the storage tank (more
2.
than 1/4 full), demand treated water from at least one piece of
equipment the MRS is supplying water to. Once all of the air has
been purged, and a solid flow of water is observed, stop the flow
at the connected equipment. Purge the air from all remaining
pieces of connected equipment by demanding water from each
one individually.
Allow the storage tank to fill until the booster pump turns off.
3.
Allow the chlorinated water to remain in the storage tank and
distribution piping for 10 minutes.
Un-plug the power cord. Drain the storage tank by demanding
4.
water downstream and allow the storage tank to drain. Once the
storage tank is empty, stop demanding water downstream.
Apply power to the system by plugging the power cord into the
5.
receptacle. Once sufficient water has entered the storage tank
(more than 1/4 full), demand treated water from at least one piece
of equipment the MRS is supplying water to. After 5 minutes,
stop the flow at the connected equipment. Flush the lines to each
remaining piece of connected equipment by demanding water
from them for 2 minutes each.
Allow the storage tank to fill until the booster pumps turns off.
6.
Un-plug the power cord. Drain the storage tank by demanding
7.
water downstream and allow the storage tank to drain. Once the
storage tank is empty, stop demanding water downstream
Repeat steps 5-7 until no residual chlorine odor is detected from
8.
the water exiting the storage tank drain valve or connected
equipment.
blend ValVe adJuStMent - MrS-350bl only
A blend valve (below pump) and sample valve (on right-side of
processor where tank connects) have been provided to adjust and
measure the TDS level of the treated water. Adjustment should be
made when the system is processing water, and the storage tank is
isolated. When making adjustments, allow the line to flush briefly
after an adjustment is made, collect a 16 oz. sample, then measure
the TDS with a calibrated TDS meter. Close the blend valve to reduce
the TDS, open it to increase the TDS. See figure 5 for blend valve
location.
PlacIng the MrS Into SerVIce
Once the cartridges have been activated, the storage tank &
distribution piping sanitized, the MRS can be placed into service.
During normal operation, the valves on the MRS should be in the
following positions:
System inlet and outlet valves – open
A.
System by-pass valve – closed.
B.
Once the system been started-up initially, it is a good idea to
measure the outlet water flow rate and quality to verify the system’s
performance. The initial values should be recorded for future
comparison to detect any changes in performance. A Performance
Log has been provided on Page 6 to record this information.
oPeratIon
During normal operation, a continuous supply of water must be
1.
available to the system.
The system inlet and outlet valves must be open, the sample
2.
outlet and flushing valves must be closed and the drain line must
be unrestricted.
3123-42b IO Guide MRS - 112108.indd 4
9/11/09 11:15:29 AM