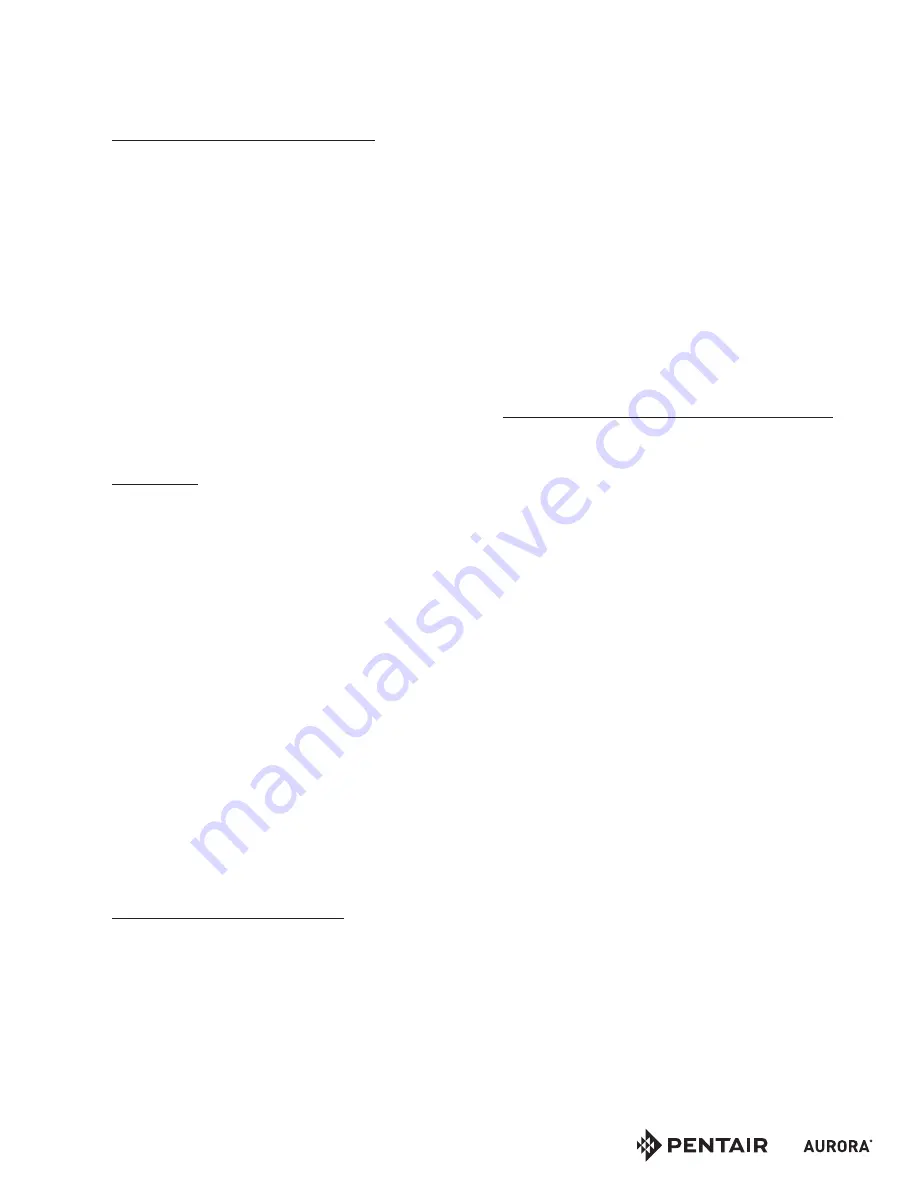
MODEL CBV-S/A GROOVED
3
ITEM
1040
DATED
JANUARY 2015
i. Flange adapter gaskets are not interchangeable with other
flange adapters.
HANDLE TURNS INDICATOR POSITION:
To adjust the handle turns indicator position to enable easier
access for viewing:
1. Fully close the valve.
2. Remove the handle retaining bolt at the hub of the handle.
3. Pull the handle straight from the valve stem (tap gently with
a soft mallet if required).
4. For models with:
a. Plastic handles; rotate the handle and turns indicator
assembly (retaining a turns indication of 0.0) and replace
the handle onto the valve stem.
b. Cast iron handles; loosen the brass knurled turns indicator
retaining ring, rotate the turns indicator to desired
position, retighten the retaining ring by hand (do not over-
tighten), and replace the handle on the valve stem.
5. Insert and tighten the valve handle retaining bolt.
6. Open the valve to ensure the handle turns freely and turns
indicator reads properly.
OPERATION:
1. If an alternate technology flowmeter is used, refer to the
instructions supplied for taking flow measurements.
2. For variable orifice flow measurement using the differential
pressure developed across the valve seat, remove the PT
Port caps from the valve using caution to avoid contact with
the hydronic fluid.
3. Insert and tighten the manometer high pressure probe to the
PT port closest to supply, and the low pressure probe to the
PT port closest to return.
4. Ensure there are no leaks at any meter probe connections.
5. Take the differential pressure measurement.
6. If the value is negative, ensure the meter connections are not
reversed. Otherwise, check the fluid flow direction in that
piping section.
7. Use the corresponding CBV-S/A Grooved performance
charts or flow calculations to convert the differential
pressure reading to the corresponding flow rate.
8. Adjust the CBV handle as required to read the required
pressure drop measurement, using the appropriate flow
coefficient for the handle setting.
9. When finished, carefully remove the meter probes to
avoid contact with the hydronic fluid, and replace the PT
port caps.
CALIBRATION MEMORY SETTING:
If desired, the memory setting may be used so that if the valve
is throttled or shut off during use or servicing, when the valve
is fully reopened, it returns precisely to the calibrated setpoint.
1. Record the valve handle turns corresponding to the
calibrated setpoint.
2. Remove the handle retaining bolt at the hub of the handle.
3. Pull the handle straight from the valve stem (tap gently with
a soft mallet if required).
4. Without turning the valve stem, for models with:
a. Plastic handles:
i. Turn the plastic memory stop clockwise until it
bottoms (finger tight only).
ii. While holding the memory stop position, turn the lock
collar clockwise until it stops against the valve bonnet.
b. Cast iron handles:
i. Turn the brass memory stop ring until the aluminum
bar contacts the step on the valve stem (finger tighten
only).
5. Replace the handle on the valve stem, ensuring the
previously recorded turns indicator reading and desired
orientation are retained.
6. Insert and tighten the valve handle retaining bolt.
7. Close the valve and then reopen fully, to ensure it turns
freely until it stops at the previously recorded calibration
setpoint.
REPLACING GLAND PACKING UNDER PRESSURE:
CBVs should provide many years of reliable service with little
or no maintenance. However, a regular schedule of inspection
for leaks is recommended. Should the valve gland packing
develop a leak, it can be replaced under pressure, avoiding the
need to depressurize and drain the system, as follows:
1. Always take necessary precautions to avoid contact with
hydronic fluid. Allow the system fluid to adjust to room
temperature if possible, or else exercise extreme caution to
avoid personal injury.
2. Record the valve handle turns corresponding to the
calibrated setpoint.
3. If the calibration memory setting feature has been
used, remove the handle as required to turn the memory
stop fully counterclockwise so that the valve can be
completely opened.
4. Open the valve fully (torque not to exceed 45 ft. lbs.).
5. The metal-to-metal service seal is now engaged. (This is not
a drip-tight seal.)
6. Carefully remove the valve packing nut very slowly,
ensuring system pressure is retained. Some escape of
hydronic fluid is normal. Be careful to avoid contact.
7. Clean the exposed portion of the valve stem, taking care not
to scratch it.
8. Remove the O-ring and gasket and replace with new
and same.
9. Replace the packing nut and tighten as required to ensure a
leak-tight seal.
10. Replace the turns indicator and memory stop mechanisms.
11. Replace the valve handle and tighten the handle
retaining nut.
12. Close the handle slightly while ensuring the valve packing
retains pressure and is drip-free.
13. Ensure the valve closes completely, reading 0.0, and opens
fully (or to the calibrated setpoint if the memory stop feature
is used).
14. Return the valve handle to the calibrated setpoint.