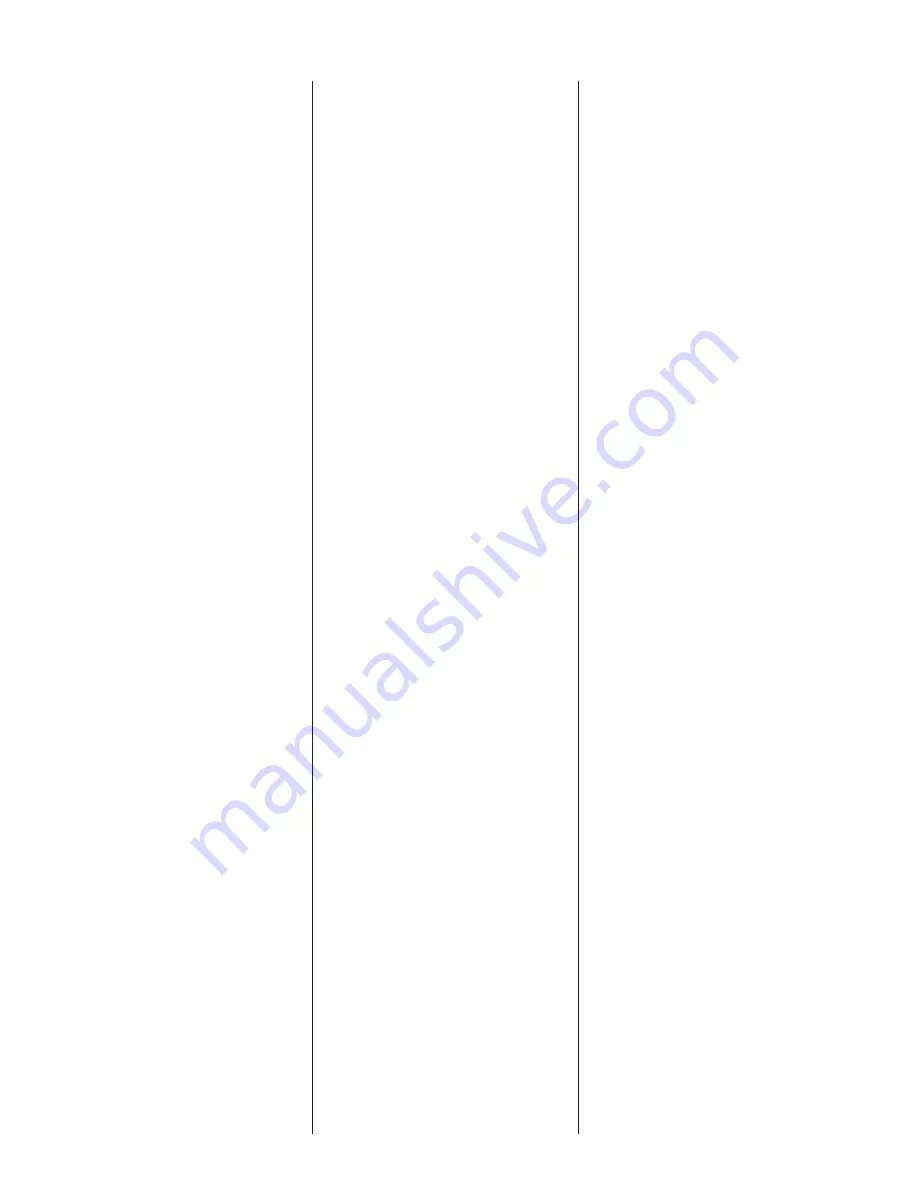
4
completely removed.
Set assembly on bench and remove
connection box. When box is lifted
off, connection wires to motor will be
exposed. These wires will probably be
burned, but each wire is tagged with a
metal marker giving the wire number. Cut
the wires.
If the leads to the connection box are
burned, a complete new connection box
with new wire must be used. The wires
are potted-in with sealing compound and
a new unit must be obtained from the
factory.
The stator is held in the housing with a
bolted-in clamp ring.
After ring is removed, turn housing
upright and bump on hardwood blocks.
This should jar the stator loose and allow
it to drop out.
Thoroughly clean housing before
replacing new stator. Replace the stator
and make all wire connections to the
connection box before replacing housing
on pump. This is important as leads must
be tucked behind the windings by using
hands up through rotor core.
IMPORTANT: Use only compression type
insulated connectors on the wires. Do
not tape leads as oil will deteriorate the
tape and cause damage to stator and
bearings.
Check top bearing. If clean and does
not turn roughly, bearings can be reused
and it is not necessary to completely
dismantle pump to change bearings. If
bearings are damaged with dirt or heat,
they must be replaced. Remember to
reinstall the upper bearing load spring.
Replace stator housing onto seal
chamber and bolt in place. Be sure seal
failure wire is connected before housing
is assembled.
Be sure O-ring seal has been replaced. If
O-ring is nicked or cut, replace with new
rings. This applies to all O-rings used in
assembly.
After all leads are reconnected in the
connection box, make a high voltage
ground test on each wire. The only wire
that should show ground is the green
power lead and the ground lead in the
auxiliary control cable.
For safety, complete pump should be
air checked under water for leaks. Lay
pump on its side for this oil filling, with
oil fill hole upright. Do not completely
fill; leave oil about one inch below plug
hole. Use only high grade transformer
oil or regular
Hydromatic
submersible
oil in this chamber. Replace plug; use
Permatex
®
on threads. Install air valve
in top plug opening of motor housing
Heat Sensors and Seal Failure
Connections:
Be sure that heat sensor wires are
connected in series with the starter coil.
Connections are provided on the terminal
strip; see wiring diagram.
Pump Operation
Starting System:
Turn H-O-A switch to Off position, then
turn on main circuit breakers.
Open all discharge valves and allow water
to rise in sump.
Turn H-O-A switch to Hand position
on one pump and notice operation. If
pump is noisy and vibrates, rotation is
wrong. To change rotation on 3ø motors,
interchange any two line leads to motor.
Do not interchange main incoming lines.
If duplex system, check second pump in
same manner.
Now set both H-O-A switches to Auto
position and allow water to rise in sump
until one pump starts. Allow pump to
operate until level drops to turn-off point.
Allow sump level to rise to start other
pump. Notice run lights on panel; pumps
should alternate on each successive
cycle of operation.
Turn both H-O-A switches to Off position
and allow sump to fill to the override
control level.
Turn both switches to Auto position and
both pumps should start and operate
together until level drops to turn-off
point.
Repeat this operation cycle several times
before leaving the job.
Check the voltage when pumps are
operating and check the amp draw of
each pump. Check amps on each wire
as sometimes a high leg will exist. One
leg can be somewhat higher, 5 to 10%,
without causing trouble. For excessive
amp draw on one leg, the power company
should be consulted.
Pump Maintenance
As the motors are oil filled no lubrication
or other maintenance is required.
If the pump is used on a Hydrorail system,
it should be lifted once every six months
and checked for corrosion and wear.
Field Service on Motor:
All submersible motors out of warranty
can be serviced in the field by any
reliable motor service shop. Any pump (in
warranty) must be returned to the factory
for service or repaired at an authorized
Hydromatic service center. Charges will
not be allowed if (in warranty) pump is
not taken to an authorized Hydromatic
service center.
Field Service on Hydromatic
Hazardous Location Pumps:
If a Hydromatic hazardous location pump
is used in a hazardous location, or if the
pump is still in warranty, the pump must
be returned to the factory for service
or repaired at an authorized Hydromatic
service center. Charges will not be
allowed if (in warranty) pump is not taken
to an authorized Hydromatic service
center. This will ensure the integrity
of the hazardous location rating of the
pump and comply with our warranty
requirements.
Disconnecting Pump Cords:
If a Hydromatic hazardous location pump
is to be removed from its location, the
pump cords may be disconnected at the
control panel (on sump mounted control
panels) and cord assembly taken with
pump. Do not reconnect power to a cord
and cap assembly while removing from
pump.
CAUTION: If cord openings from sump
to control panel are open, gases from
sump could enter panel and an explosive
condition could exist.
Replacing Cords:
The power cord and heat sensor – seal
failure cord is potted into the connection
box cap, forming the cord and cap
assembly.
If cords require replacement due to
damage or cords being too short, cord
and cap assembly must be replaced as
a complete assembly available from
factory.
Check pump for proper rotation before
returning to normal service.
Replacing Lower Seal, Impeller or
Volute:
The wet-end components may be
repaired or replaced by an authorized
Hydromatic service facility without
compromising the hazardous location
rating to the pump.
Replacing Stator:
If stator only is damaged, it may not
be necessary to completely dismantle
pump as stator and housing can be lifted
from pump without disturbing seals or
bearings.
Drain all oil from upper housing, remove
from upper housing, remove drain plug
in bottom of stator housing and remove
plug in top of housing to allow air to enter.
After chamber is drained, remove hold-
down bolts and lift off. Use care in lifting
as the seal failure connecting wire must
be disconnected before housing is
Summary of Contents for S3HRC
Page 7: ...7 Wiring Diagrams...