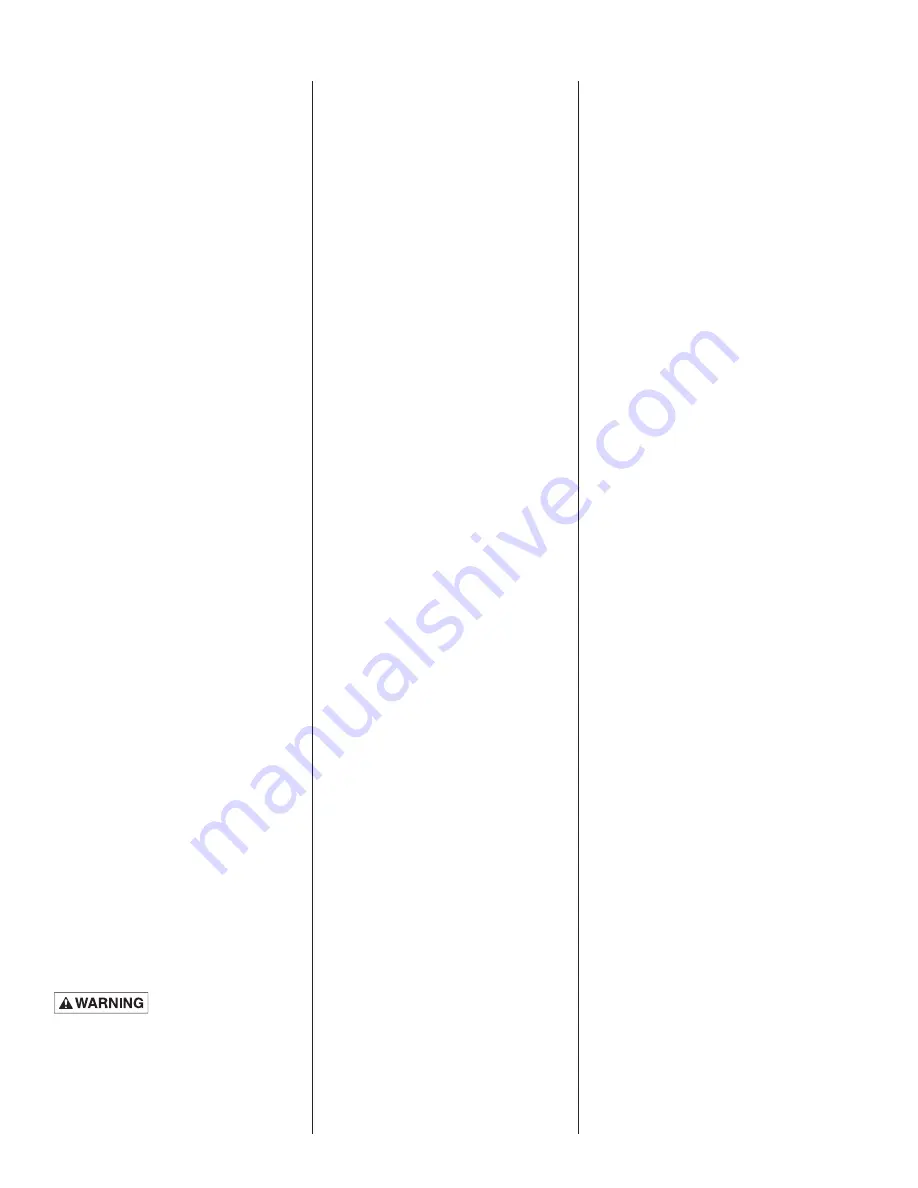
2
General Information
Attention:
This manual contains important
information for the safe use of this
product. Read this manual completely
before using this product and refer to
it often for continued safe product use.
Reasonable care and safe methods
should be practiced. Check local codes
and requirements before installation.
Unpacking Pump:
When unpacking unit, check for concealed
damage. Claims for damage must be made
at the receiving end through the delivery
carrier. Damage cannot be processed
from the factory.
Safety Warnings
DANGER: Risk of electrical shock or
electrocution. May result in serious
injury, death or fire hazard. Installer
must disconnect all electrical sources
prior to installation, handling or servicing.
Only qualified personnel may install this
system. NFPA 70/National Electric Code
(NEC) or local codes must be followed.
System must be properly grounded
according to NEC. Do not lift pump by
power cord.
DANGER: Biohazard risk. Once wastewater
source has been connected to system,
biohazard risk exists. Installer(s) and/
or service personnel must use proper
personal protective equipment and follow
handling procedures per OSHA 29 CFR
1910.1030 when handling equipment after
wastewater source has been connected
to system.
DANGER: Risk of asphyxiation. Installer(s)
and/or service personnel must use proper
personal protective equipment and follow
OSHA 29 CFR 1910.146 or OSHA 29 CFR
1926. Pump may be installed in a location
classified as a confined space.
DANGER: Cutting risk. Risk of serious
cutting or amputation exists. Disconnect
all power sources prior to servicing the
pump. Pump may start without warning.
Pumps are not approved for use in
swimming pools, recreational water
installations, decorative fountains or any
installation where human contact with
the pumped fluid is common.
CALIFORNIA PROPOSITION 65
WARNING:
This product and related
accessories contain chemicals known to
the State of California to cause cancer,
birth defects or other reproductive harm.
Pumps in Storage or Not Operating:
Pumps with carbon ceramic seals must
have impellers manually rotated (six
revolutions) after sitting non-operational
for three months or longer and prior to
electrical start-up.
Pumps with tungsten carbide seals must
have impellers manually rotated (six
revolutions) after sitting non-operational
for three weeks or longer and prior to
electrical start-up.
Seal Failure:
An electrode is installed in the seal
chamber so if any water enters the
chamber through the first seal, the
electrode will be energized and a signal
will be transmitted to the sensing unit at
ground surface causing an alarm function
to energize.
In operation the seal failure unit indicates
only that there is some water in the seal
chamber. The pump will continue to
operate without damage, but the seal
should be checked immediately after
failure is indicated.
NOTE: Failure to install such a device
negates all warranties by Hydromatic®.
Seal Failure Probes:
All hazardous location submersible
pumps have two factory installed
moisture detectors (seal failure probes).
They are in a normally open series circuit
in the seal chamber. Under normal
operating conditions, the circuit remains
open. If the lower seal leaks and moisture
enters this chamber, the moisture would
settle to the bottom of the chamber and
will complete the circuit between the
moisture detectors.
This circuit must be connected to a
sensing unit and signaling device. This
is supplied in a Hydromatic built control
panel.
Pump:
The submersible pumps are supplied for
one and three-phase and for 208, 230, 460
or 575 volts. Power cable is supplied with
the green wire for ground. Be sure green
wire is connected to an approved ground.
Heat Sensors:
All motors have heat sensor units
embedded in the motor winding to
detect excessive heat. The heat sensors
are set to trip at 105°C, and 120°C for
hazardous location, so it will not operate
if dangerous heat occurs. The sensors
automatically reset when motor cools to
safe temperature.
The sensors are connected in series with
the motor starter coil so that the starter
is tripped if the heat sensor opens. The
motor starter is equipped with overload
heaters so all normal overloads are
protected by the starter.
Once sensor re sets, the starter is to be
re set for FM for continued operation of
the pump. This circuitry is supplied in a
Hydromatic control panel.
NOTE: Failure to install such circuitry
would negate FM approvals and all
warranties by Hydromatic.
IMPORTANT: If Hydromatic electrical
starting equipment is not supplied, the
heat sensor circuit must be connected
in series with the starter coil or warranty
is void.
Power Cords:
The power cord and heat sensor seal
failure cord are potted into the connection
box cap. The cords must not be spliced.
NOTE: Each cable has a green lead. This
is the ground wire and must be grounded
properly per NEC and/or local codes.
Cords should be inspected for abnormal
wear and replaced accordingly.
Sump Level Control:
The sump level is controlled by
Hydromatic float switch controls. The
float is held in position in the sump by a
weight attached to the power cord above
the float. The cord supports the float and
is adjusted for height from the surface.
Typical duplex systems use three
controls: one set at turn-off, one set at
turn-on for one pump, and one set for
turn-on for two pumps. Pumps alternate
operation on each successive cycle.
Two pumps operate together only if
sump level rises to the third or override
control. The override control also brings
on the second pump in case of failure
of the first pump. Extra floats with
appropriate controls can be supplied for
alarm functions. Triplex systems use four
controls: one set at turn-off, one set at
turn-on for one pump, one set at turn-on
for two pumps, and one set at turn-on
for three pumps. Pumps alternate each
successive cycle.
Three pumps operate together only if
sump level rises to the fourth control
(second override). This control also
brings on the third pump in case of failure
of either or both of the first two pumps.
Alarm Controls:
The alarm level is usually set above the
override level so the alarm will signal only
if the override level is exceeded.However,
some engineers prefer to have the alarm
level set below the override level as it
is possible for one pump to fail and the
other pump to operate on the override
level with the sump level never reaching
the alarm level. This is particularly true in
cases of low inflow capacity.
Electrical Control Panel:
It is recommended that the Hydromatic
control panel be used with all pumps as
Summary of Contents for S3HRC
Page 7: ...7 Wiring Diagrams...