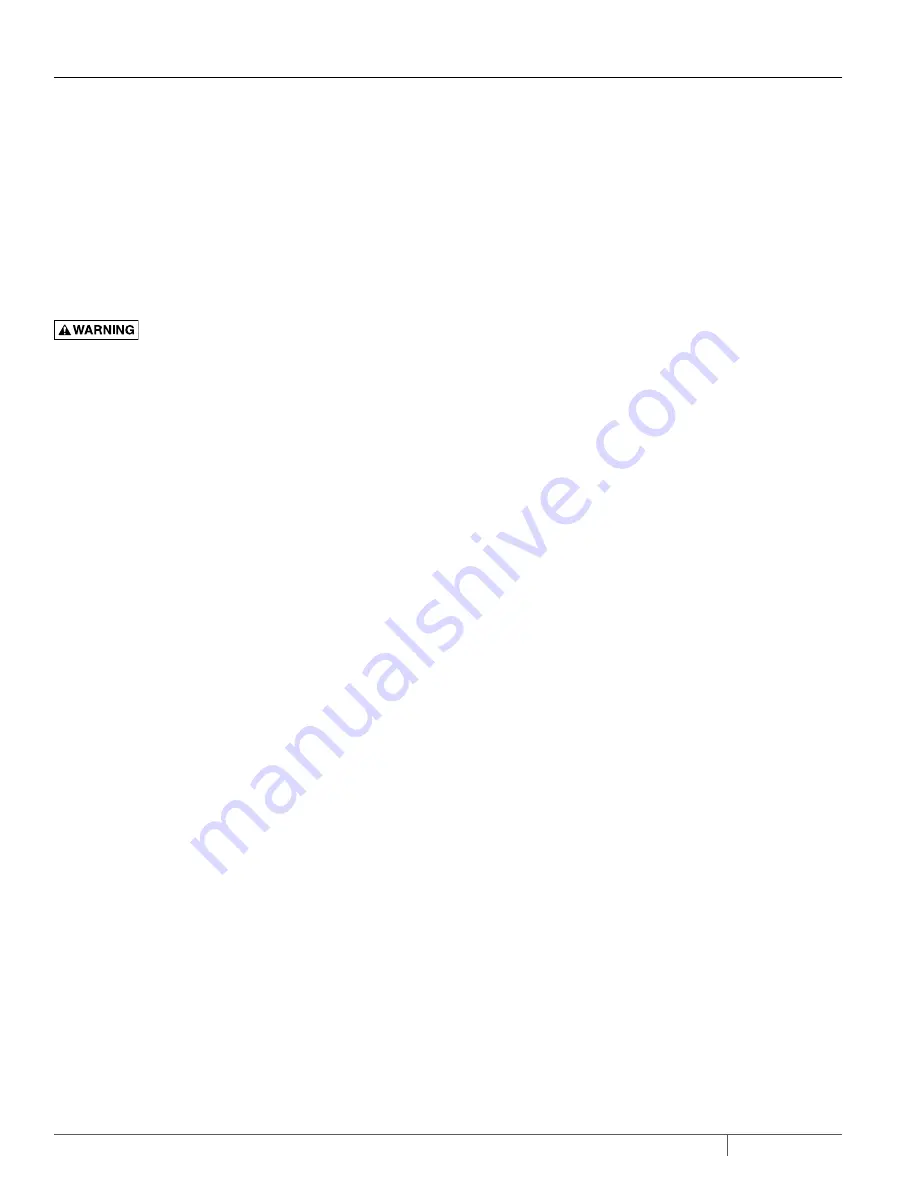
4
E-03-577 (01-23-20)
This manual contains important information for the safe use of
this product. Read completely and do not throw away.
Reasonable care and safe methods should be practiced. Check
local codes and requirements before installation.
UNPACKING PUMP
When unpacking unit, check for damage. Claims for damage must
be made at the receiving end through the delivery carrier. Damage
cannot be processed from the factory.
Before handling these pumps and controls,
always disconnect the power first. Do not smoke or use sparkable
electrical devices or flames in a septic (gaseous) or possible
septic sump.
PUMPS IN STORAGE OR NOT OPERATING
Pumps with silicon/carbide seals must have impellers manually
rotated (6 revolutions) after setting non-operational for 3 months
or longer and prior to electrical start-up.
Pumps with tungsten carbide seals must have impellers
manually rotated (6 revolutions) after setting non-operational
for 3 weeks or longer and prior to electrical start-up.
SEAL FAILURE PROBES
All hazardous location submersible pumps have two factory
installed moisture detectors (seal failure probes). They are in a
normally open series circuit in the seal chamber. Under normal
operating conditions, the circuit remains open. If the lower seal
leaks and moisture enters this chamber, the moisture would
settle to the bottom of the chamber and will complete the circuit
between the moisture detectors.
This circuit must be connected to a sensing unit and signaling
device. This is supplied in a Hydromatic
®
built control panel.
Failure to install such a device negates all warranties by
Hydromatic.
HEAT SENSORS
All motors in this family have heat sensors on or embedded in the
motor winding to detect excessive heat. This prevents damage to
the motor. If sensor trips due to excessive winding temperature,
the starter in the panel breaks power to the pump.
Once the sensor resets, the starter is automatically reset for FM
for continued operation of the pump. This circuitry is supplied in a
Hydromatic control panel.
The sensors are set to trip at 130°C.
Failure to install such circuitry would negate FM approvals and
all warranties by Hydromatic.
POWER CORDS
The power cord and heat sensor seal failure cord are potted into
the cord cap. The cords must not be spliced.
Each cable has a green lead. This is the ground wire and must be
grounded properly per NEC and/or local codes. Cords should be
inspected for abnormal wear and replaced accordingly.
OVERLOAD HEATERS
If the Hydromatic electrical panel is not used, starters with 3 leg
overload relay must be supplied on 3 phase pumps. Each leg is to
have an identical heater sized in accordance with the nameplate
amps on the motor housing. The amp draw on these submersible
motors is slightly higher than a corresponding horsepower surface
motor, so heaters must be sized by the nameplate rating.
Capacitor start single phase pumps have a run and start winding
that draws different currents. To adequately protect these
windings with the appropriate heaters, consult the factory.
The red lead is always the start winding of a pump using single
phase.
INSTALLING SUMP LEVEL CONTROLS FLOAT CONTROLS
In either simplex, duplex or triplex systems, the lower or turn-
off control is to be set to maintain a minimum level in the sump.
This level shall be no more than 3-1/4" from the top of the motor
housing down to the surface of the sewage.
The second or turn-on control is set above the lower turn-off
control. The exact distance between the two floats must be a
compromise between a frequent pumping cycle (10 starts per hour
max.) to control septicity, solids and a slower cycle for energy
economy. This distance should be determined by the engineer or
consulting engineer, depending on the conditions of
the application.
GENERAL INFORMATION
Summary of Contents for C4S(X)P Series
Page 14: ...14 E 03 577 01 23 20 NOTES...
Page 15: ...15 E 03 577 01 23 20 NOTES...