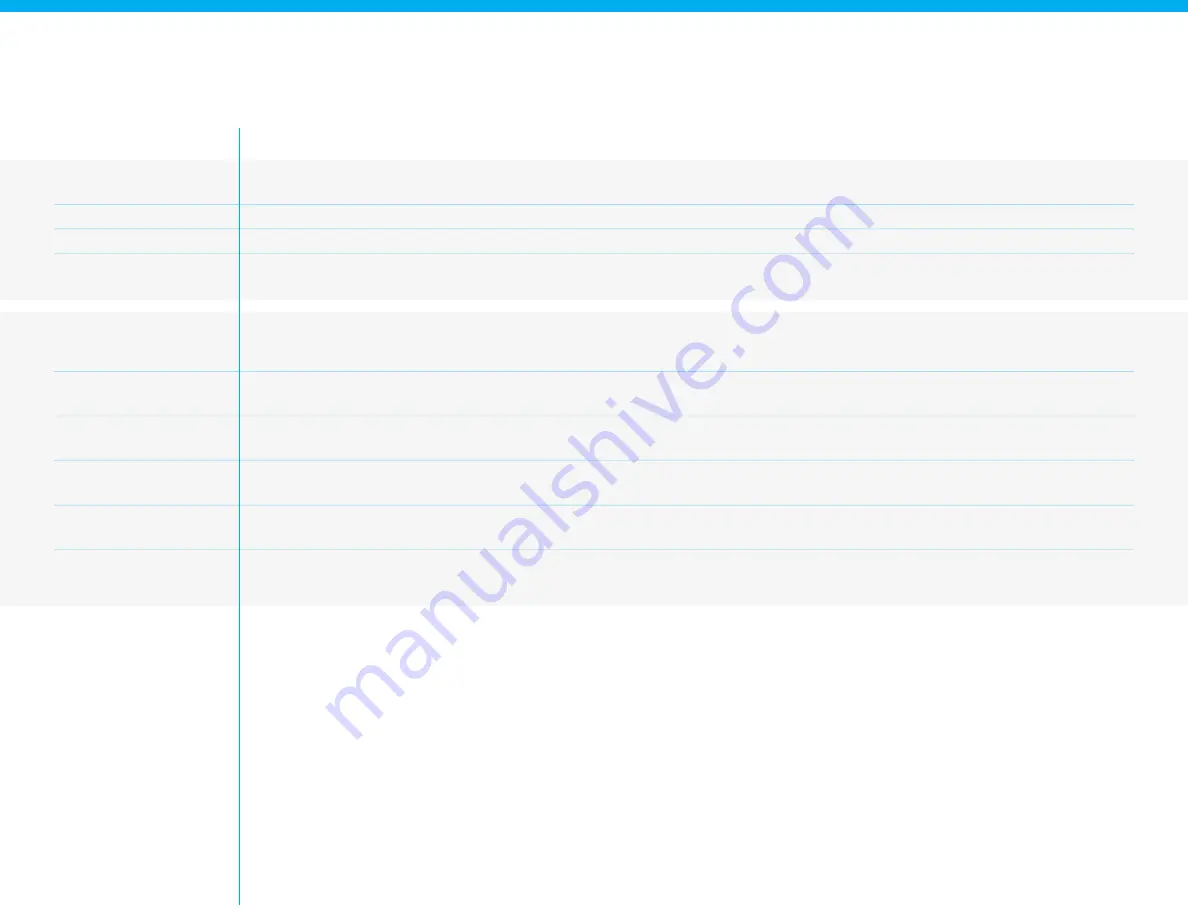
Glossary and Definitions
TERM
HARDWARE
DESCRIPTION
Bend Head
Static bending mandrels. The center of the bending area that doesn’t move.
Bend Ring
Rotating plate that carries the Bend Pin. Rotates around the Bend Head.
Bend Pin
The moving bending mandrel that is mounted on the Bend Ring. This could be a pin pressed on the Bend Ring, or an easy to replace insert
Feed Wheels
The four wheels that drive, or “feed” the wire into the bending area.
WIREWARE SCRIPT
PAUSE
Holds the script until the “Resume” button is pressed. This is equivalent to the “!” in GCode (but we don’t support that code). This is different to the
G4 GCode command in that PAUSE does not need a time parameter.
FEED x
Moves the wire an “x” amount in either inches or mm. The “x” value can be either positive (forward), or negative (backwards) Uses the feed speed
defined in the Material Profile
BEND a
Moves the Bend Ring an “a” amount in degrees. The “a” value can be either positive (Clockwise) or negative (counterclockwise). Uses the bend speed
defined in the Material Profile
REPEAT n: ... END
A loop that repeats the code between “REPEAT” and “END” an “n” number of times. Very useful when bending many copies of the same part, or
bump bending. Currently we do not support nested REPEAT loops (REPEAT within a REPEAT)
PINZ z
Moves the Bend Ring a “z” amount in either inches or mm. The “z” value can be either positive (up) or negative (down), but take in account that the
maximum travel is from 0 to -10mm, and could vary depending on your bend hardware configuration.
PINA a
Moves the Bend Pin an “a” amount in degrees. PINA is a much more convenient way to write the GCode: “G90 G1 A_ F_”. The “a” value can be
either positive (Clockwise) or negative (Counterclockwise). Uses the bend speed defined in the Material Profile
82
Summary of Contents for D.I.Wire Pro
Page 1: ...Version 19 4 16 1 ...
Page 3: ...Introduction SECTION 1 3 ...
Page 9: ...HardwareSetupAnd Safety SECTION 02 9 ...
Page 16: ...2x R25 55 2x R7 95 170 70 Bending SECTION 03 16 ...
Page 17: ...LOADING MATERIAL CLAMPING AND ALIGNMENT Bending 03 BENDING 17 ...
Page 20: ...SettingUpWireWare SECTION 04 20 ...
Page 23: ...PathMode SECTION 04 23 ...
Page 34: ...ScriptMode SECTION 05 34 ...
Page 41: ...MaterialProfileMode SECTION 06 41 ...
Page 50: ...SECTION 07 Maintenance Troubleshooting 50 ...
Page 55: ...SECTION 07 ReplacingYourBending Components 55 ...
Page 58: ...SECTION 07 ReplacingThe BendHead 58 ...
Page 67: ...SECTION 07 ChangingTheFeed Wheels 67 ...
Page 74: ...SECTION 07 ChangingTheGuides 74 ...
Page 81: ...SECTION 08 References 81 ...
Page 84: ...http www pensalabs com support pensalabs com 84 ...