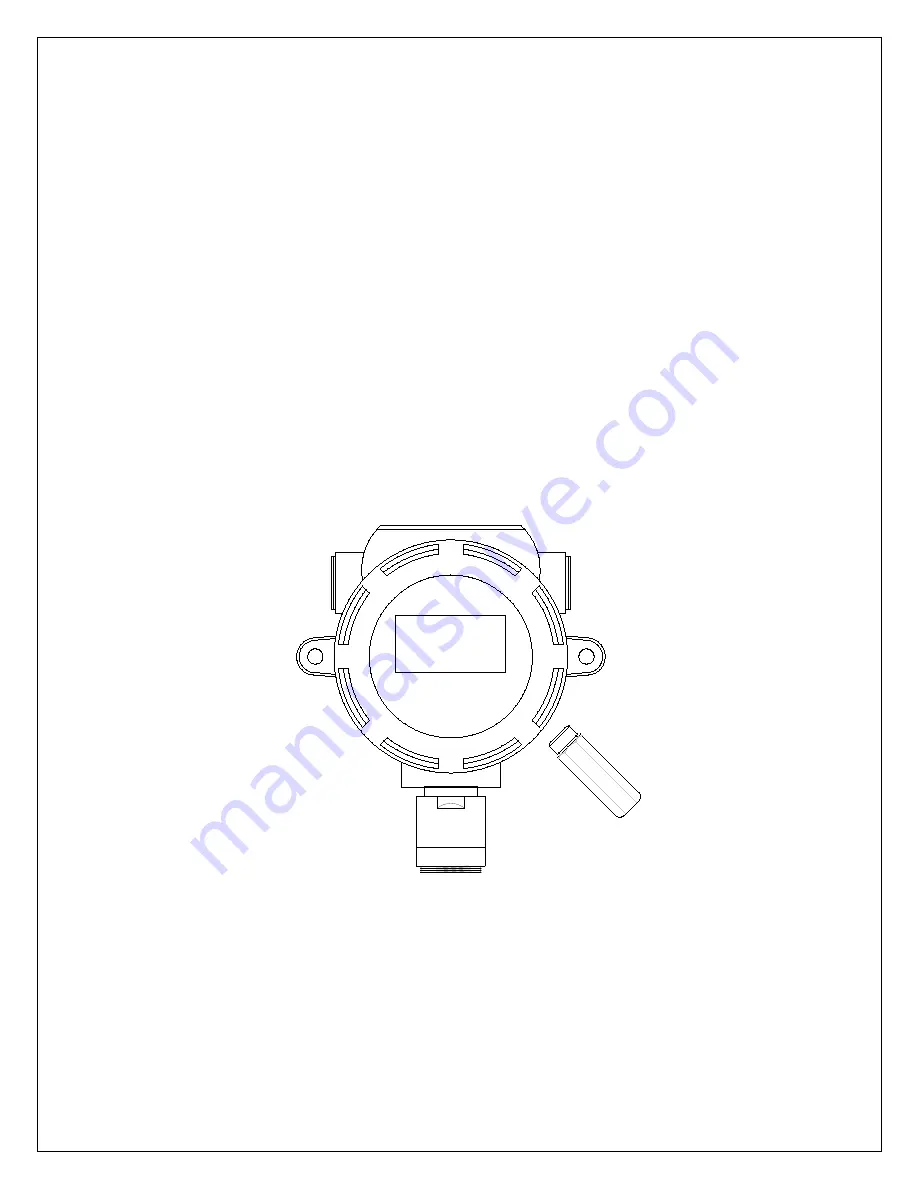
PT495 Series Detector
(Ultra1000)
Rev 5.11
25
Edit Configuration
Set Alarm Levels and Unit Address
Using the magnetic wand, activate the internal magnet sensitive switch. Refer to
figure 8 below for the position of the configuration switch. The switch is located
on the transmitter board at 4 o’clock position.
Touch the enclosure with the magnetic wand as shown in figure below. After a
few seconds the detector will enter into
Edit Config
(uration) mode and the
message is displayed on the LCD. Remove the magnet. The detector will scroll
all the configuration options one at time. Available options are shown below in
configuration menu.
Edit all configuration parameters as necessary. When completed select the Exit
to return to normal operation. Typically the configuration options are edited
during installation. All the configuration data is stored in non-volatile memory
and are retained during power down of the detector.
Alarm 1
15
Magnet
ic W
and
Edit
Config
Figure 8. Edit Configuration using magnetic wand