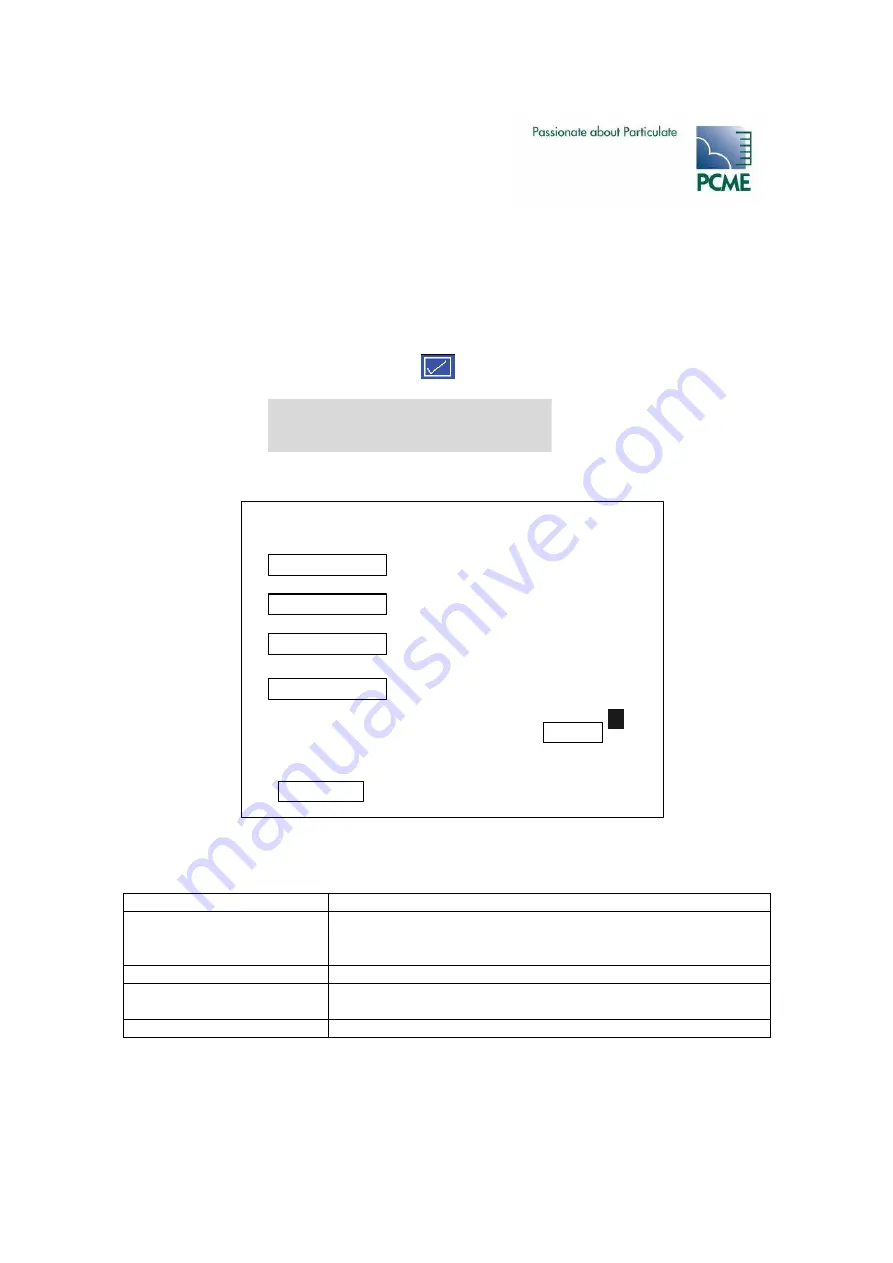
- PCME QAL 181 MANUAL: 94 -
13
CLEANING PROCEDURES
The are several controls both at the control unit and within the sensor enclosure to aid the
following cleaning procedures.
The Cleaning Screen in the Control Unit
Select ‘Quality Assurance/Self Tests’ display
Select Device = 181 Dust channel
Select “Cleaning”
The Cleaning Screen is displayed:
The Cleaning Screen provides user control of the sensor:
Entry Shutter
Place the quadrant into the shutter position. This should be done
before attempting to cleaning the measurement region to stop
dust entering the sensor.
Exit Shutter
This function is not used.
Span Element
This places the quadrant into the Span Test position. This makes
the span test element visible to aid cleaning of the span element.
Laser
Turns laser off to provide safety whist cleaning.
The Quadrant Position setting adjusts the position of the quadrant. This should not normally be
adjusted.
Cleaning
Exit
Entry Shutter
5.5
>
>
Activate
Activate
Activate
Activate
Exit Shutter
Span Element
Laser
Quadrant Position
Open / Closed
Open / Closed
Open / Closed
30
Purge Flow
On / Off
Summary of Contents for QAL 181 X
Page 2: ...PCME QAL 181 MANUAL 2...
Page 15: ...PCME QAL 181 MANUAL 15...
Page 26: ...PCME QAL 181 MANUAL 26 5 4 2 1 3...
Page 30: ...PCME QAL 181 MANUAL 30 Figure 3 3 PLUS System Daisy Chained...
Page 87: ...PCME QAL 181 MANUAL 87...