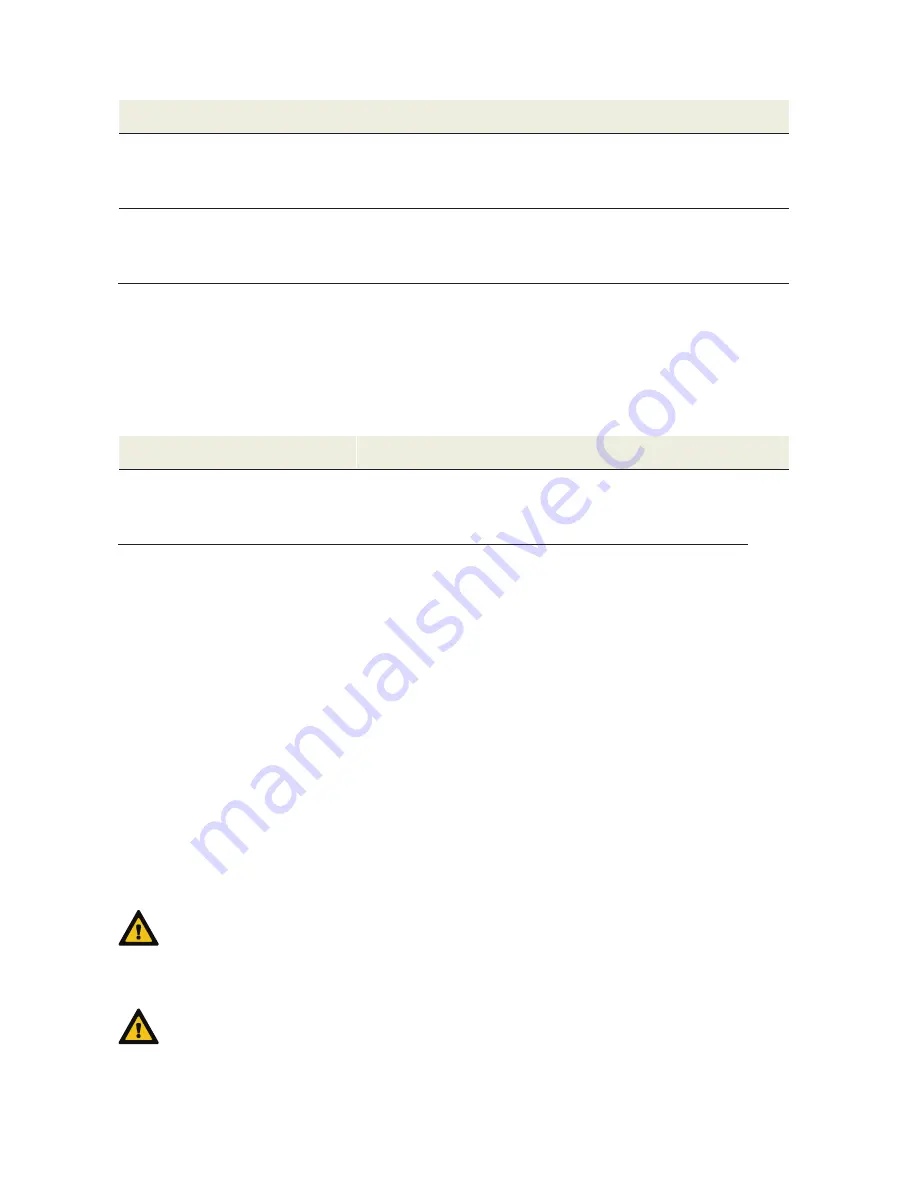
24
Abbreviation
Designation
Explanation / actions
x_out_max Maximum
outside
temperature
Setting range upper threshold: 15 °C…30 °C
If the intake temperature is above the set threshold value, the flap
of the geothermal heat exchanger opens the intake air duct for
cooling the intake air.
→
cooling function
x_out_min Minimum
outside
temperature
Setting range lower threshold: -10 °C…14.5 °C
If the intake temperature is below the set threshold value, the flap
of the geothermal heat exchanger opens the intake air duct for
heating the intake air.
→
frost protection function
Tab. 15: Parameterisation Temperature thresholds flap of the geothermal heat exchanger
2.3.2.12 Submenu Cooling brine defroster
In this menu, an optionally available brine defroster is displayed. The cooling function of the brine
defroster can be activated or deactivated. The release of the brine defroster is selected using the
navigation buttons (red background of the text) and by setting the checkmark, and is confirmed with
Enter. Furthermore, the temperature threshold for the cooling function can be selected using the
navigation buttons (red background of the text) and can be set using the b / -.
Abbreviation
Designation
Explanation / actions
x_bdt Temperature
brine defroster
Setting range: 15 °C…30 °C
If the outside temperature is above the set threshold value,
the brine defroster is activated for cooling the intake air.
→
cooling function
Tab. 16: Parameterisation temperature threshold brine defroster
Boost ventilation mode with external boost ventilation sensing device
2.3.3
In most cases, boost ventilation sensing devices are mounted in exhaust air rooms such as bathrooms,
W.C.s or kitchens in order to activate temporary maximum ventilation in these rooms for fast discharge of
increased moisture and odours.
When operating this control element, the functional properties and visualisations described for the boost
ventilation mode with LED control panel or TFT touch panel are generated. The boost ventilation mode is
started again at each activation and interrupts the current operating mode for the duration set. Following
this, the device switches back to the previously active operating mode. Manually switching the operating
mode by means of connected control panels stops the boost ventilation function.
Maintenance by the operator
2.4
Maintenance of the ventilation device and plant by the operator is limited to the periodic change of the
filters and cleaning of the supply and exhaust air valves. The filter must be checked every 3 months and
changed if necessary, however, at least every 6 months.
In this context, also check other filters available inside the ventilation plant and change them if necessary.
A replacement or cleaning of the filter mats at the exhaust air valves (e.g. bathroom, kitchen, W.C.s)
should be carried out every 2 – 3 months or at your own discretion when checking the degree of soiling.
If maintenance work is not carried out regularly, this impairs the functioning of the comfort
ventilation in the long term!
Replacement of the filter
2.4.1
The plant must not be operated without filter. During filter replacement and maintenance
work, the ventilation device must be switched off!
Two high-quality original PAUL filters are installed inside the NOVUS, which is recognisable by the
imprinted PAUL logo. The filters can be purchased online from PAUL Wärmerückgewinnung GmbH at
Summary of Contents for NOVUS 300
Page 1: ...Version 2 0_10 2014 EN...
Page 59: ...59 Dimensional sketch 3 9 5 Fig 47 Dimension drawing HRU NOVUS...
Page 60: ...60 Plant 1 circuit diagram NOVUS 3 9 6...
Page 61: ...61 Plant 2 circuit diagram NOVUS with integrated defroster 3 9 7...
Page 62: ...62 Plant 3 Terminal scheme of through terminal X10 3 9 8...