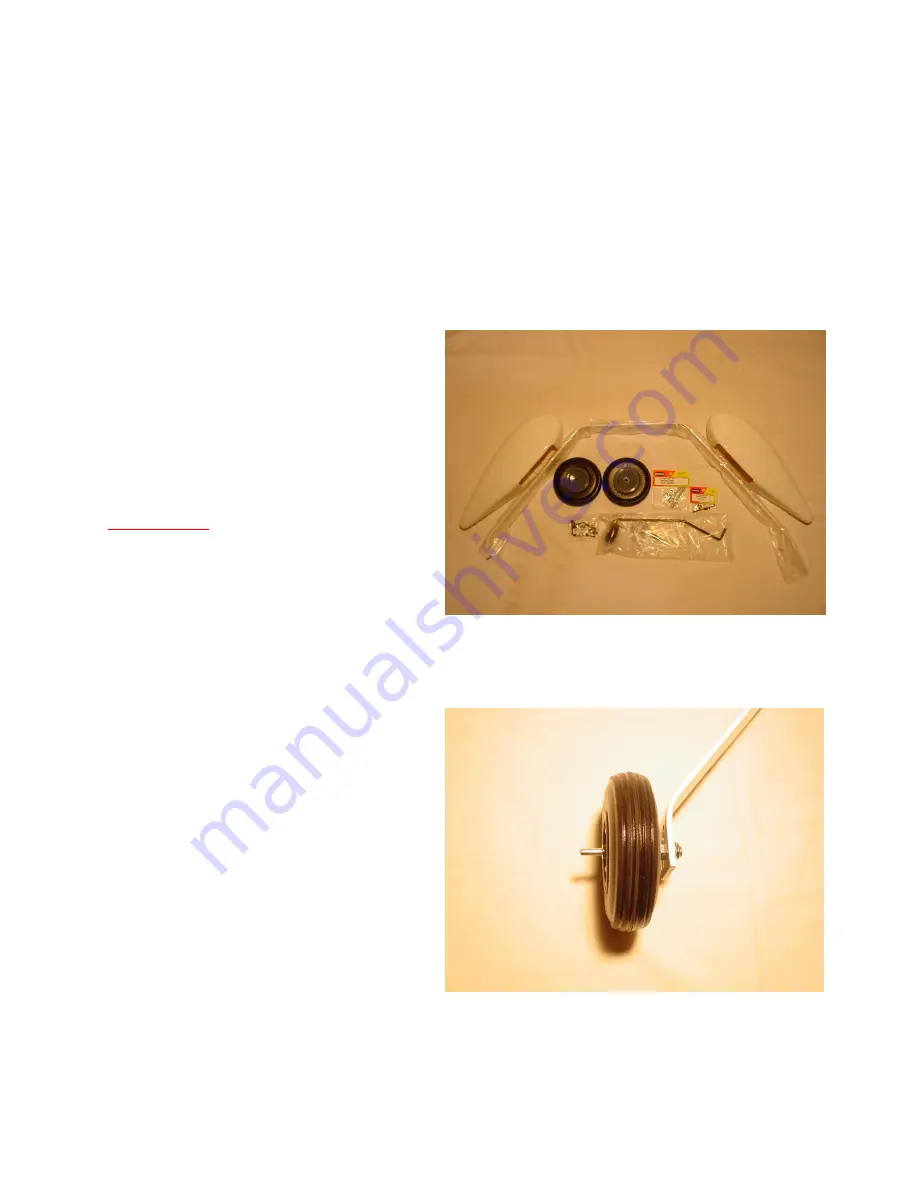
6
Chapter 3
Landing Gear and Tail Wheel Assemblies
Now that we’re ready for assembly, we are going to start with the main landing gear first. You will need to
locate the following parts to begin assembly.
Place an “
×
×
×
×
” to ensure task completion:
What you will need in this chapter for the main gear:
Aluminum main gear
One pair of 4.5” inch wheels
One pair of wheel pants
One pair of Dubro axles
Four wheel collars
Hardware pack marked “wheels”
Fuselage
Rudder
Carbon Fiber Tail wheel assembly
Not Provided:
½” and a 9/16” inch wrench
Blue loc-tite
Allen wrench for wheel collars
White wood glue such as Elmer’s or
Epoxy
Fasten the axles to the main landing gear
with the lock nuts.
Using your four wheel collars and wheels,
center you wheels on the axles. Place the
collars as close to the wheels as possible but
ensure the wheels still rotate freely. Again,
we don’t want the wheel to move from side
to side and contact the wheel pants. Also,
we recommend the use of loc-tite on the
setscrews of the wheel collars to prevent
them from vibrating loose.